LV on quality
Page 32
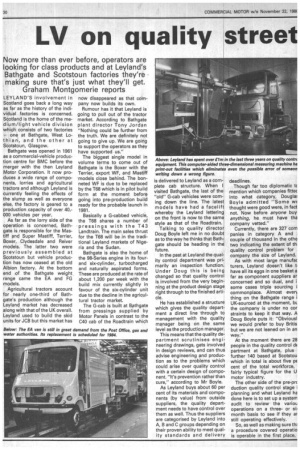
Page 33

If you've noticed an error in this article please click here to report it so we can fix it.
Now more than ever before, operators are looking for class products and at Leyland's Bathgate and Scotstoun factories they're making sure that's just what they'll get.
Graham Montgomerie reports
LEYLAND'S involvement in Scotland goes back a long way as far as the history of the individual factories is concerned. Scotland is the home of the medium/light vehicle division which consists of two factories — one at Bathgate, West Lothian, and the other at Scotstoun, Glasgow.
Bathgate was opened in 1961 as a commercial-vehicle production centre for BMC before the merger with the then Leyland Motor Corporation. It now produces a wide range of components, lorries and agricultural tractors and although Leyland is currently feeling the effects of the slump as well as everyone else, the factory is geared to a production capacity of over 40,000 vehicles per year.
As far as the lorry side of the operation is concerned, Bathgate is responsible for the Mastiff and Super Mastiff, Terrier, Boxer, Clydesdale and Reiver models. The latter two were previously assembled at Scotstoun but vehicle production has now ceased at the old Albion factory. At the bottom end of the Bathgate weight range came the EA and FG models.
Agricultural tractors account for nearly one-third of Bathgate's production although the Leyland market has decreased along with that of the UK overall. Leyland used to build the skid units for JCB but this market has now disappeared as that company now builds its own.
Rumour has it that Leyland is going to pull out of the tractor market. According to Bathgate plant director Tony Jordan "Nothing could be further from the truth. We are definitely not going to give up. We are going to support the operators as they have supported us."
The biggest single model in volume terms to come out of Bathgate is the Boxer with the Terrier, export WF, and Mastiff models close behind. The bonneted WF is due to be replaced by the 168 which is in pilot build form at the moment before going into pre-production build ready for the probable launch in 1981.
Basically a G-cabbed vehicle, the T68 shares a number of pressings with the T43 Landtrain. The main sales thrust for the 168 will be in the traditional Leyland markets of Nigeria and the Sudan.
Bathgate is also the home of the 98-Series engine in its fourand six-cylinder, turbocharged and naturally aspirated forms. These are produced at the rate of about 1,200 per week with the build mix currently slightly in favour of the six-cylinder unit due to the decline in the agricultural tractor market.
The G-cab is built at B,athgate from pressings supplied by Motor Panels in contrast to the C40 cab of the Roadtrain which
is delivered to Leyland as a complete cab structure. When I visited Bathgate, the last of the "old" G-cab vehicles were coming down the line. The lates models have had a facelif whereby the Leyland lettering
on the front is now to the sam style as that of the Roadtrain. Talking to quality directo Doug Boyle left me in no doub as to the way he thinks that Bath gate should be heading in the future.
In the past at Leyland the quak, ity control department was prk manly an inspection function Under Doug this is being changed so that quality contro is involved from the very begin fling at the product design stag right through to the finished arti cle.
He has established a structur which gives the quality depart ment a direct line through t management with the qualit manager being on the samb level as the production manager This means that the quality department scrutinises engineering drawings, gets involved in design reviews, and can thus advise engineering and production as to the problems which could arise over quality control with a certain design of component. "It's prevention rather than cure," according to Mr Boyle.
As Leyland buys about 60 per cent of its materials and components (by value) from outside suppliers, the quality department needs to have control over them as well. Thus the suppliers are categorised by Leyland into A, B and C groups depending on their proven ability to meet quality standards and delivery deadlines.
Though far too diplomatic tc mention which companies fittec into what category, Dougla; Boyle admitted "Some wt thought were good were, in fact not. Now before anyone buy anything, he must have tha company vetted."
Currently, there are 327 corn panies in category A and couple of thousand in the othe two indicating the extent of th, quality control problem for company the size of Leyland.
As with most large manufac turers, Leyland doesn't like t,
have all its eggs in one basket a far as component suppliers ar concerned and so dual, and i some cases triple sourcing i commonplace. Almost even, thing on the Bathgate range i UK-sourced at the moment, Ix.
the company is under no cor straints to keep it that way. A Doug Boyle puts it: "Obviousl we would prefer to buy Britis but we are not leaned on in an way."
At the moment there are 28 people in the quality control tit partment at Bathgate, plus further 140 based at Scotstou which in total is about five pc cent of the total workforce, fairly typical figure for the U motor industry.
The other side of the pre-prc duction quality control stage i planning and what Leyland ha done here is to set up a system audit to review the variou operations on a threeor si) month basis to see if they at still operating effectively.
So, as well as making sure tht a procedure covered operatio is operable in the first place, check is also made to see that this is repeated as time goes by. "If you don't try to improve, you're only going to get worse," said Doug Boyle.
It is a well-known and oftquoted fact that the end product is only as good as the standard of the individual production stages. Whereas a few years ago, inspection and quality control concerned the completed component only, now it is involved in all the production stages to the extent that Leyland has invested over £1 m on quality control measuring equipment in the last three years.
Or, put another way, "We're putting our money where our mouth is" in the words of Doug Boyle.
This expenditure has included buying three dimensional measuring equipment with print-out facilities which eliminates the error of someone writing something down. Always ready with he right word for the occasion Doug Boyle stressed, "I have to take opinion out. If I'm going to hammer somebody flat because of a quality problem then it's facts that I want."
Every product in the Bathgate range now goes on a chassis dynamometer for approximately 30 minutes. Leyland has two of these as well as a humidity test chamber which is large enough to take a complete EA van. This is used to accelerate the weathering process and can provide temperatures up to 60°C (140°F) and up to 100 per cent humidity.
Leyland claims that this test chamber can tell the quality control people in 24 hours whether the paint finish will blister in three or six months time.
As well as investing in meteorology equipment, Leyland has spent a lot of time and money controlling paint quality. Bathgate is the only Leyland factory to have an anodic electrophoretic paint shop, though the company is looking at the possibilities of converting to a cathodic process for further improvements in corrosion and chip resistance.
Like most other manufacturers, Leyland uses a vehicle audit inspection system whereby a vehicle (out of all the product range) is taken from the end of the line and gone over with the proverbial fine tooth comb.
One lorry and one tractor are stripped each day and this procedure also applies to engines and axles which are taken apart to the last nut and bolt and checked.
As about 50 per cent of Leyland production is shipped overseas in ckd form, this same stripdown procedure is applied to the export "vehicle packs". The export models are shipped out in crates containing all the components (literally down to the last nut and bolt) necessary to assemble four complete chassis. Two of these crates are unpacked and the components stripped down and checked every month.
Over at Scotstoun, the Albion factory is undergoing a drastic rebuild, reflecting the change in Leyland's long-term planning policy. The last vehicle to be built at Scotstoun (a Viking busl rolled off the line on October 24. The factory is to become a specialist manufacturing unit for gearboxes and axles to feed the other Leyland factories.
Currently, Scotstoun builds the Leyland five-ton front axle, the transfer box for the Reiver bogie, the nine-ton axle for the Chieftain (which doubles up in the 18 ton bogie for the Reiver, Bison and Constructor) the tenton Clydesdale axle, and the five-speed constant-mesh gear
box with overdrive top for thi Reiver and Clydesdale.
The big news from the Albior plant earlier this year was the announcement that ZF gear boxes would be built by Leylan( under licence from the Gerrnar company. The agreement wal signed last February and is t( run for 12 years.
The gearbox in question is thr synchromesh 86-36 which wil be built at a rate of 300 per weel for the sole use of Leyland. Thr licensing agreement does no allow LV to sell the Scotstoun built box to anyone else.
Production of the ZF gearbo) is scheduled to begin in 1982 and it is expected that it will talc( about four months to build up tc the full scheduled productior rate.
Again, as part of the overal Leyland component rationalisa tion plan, the production of tilt Leyland hub reduction axles is t( be transferred from Lancashirt to Scotland where they will hr manufactured to the same basil design as the Albion mediurr axle.
Currently, the 11and 13 tonne Leyland axle casing is 2 three-piece design using a cast iron bowl and steel axle tube: with all the associated bracken-) welded on afterwards — process which Leyland does no now regard as being particularl) cost-effective.
The Albion axle casings arr pressed and are claimed to be a: strong as the Leyland design bu considerably lighter. The cost o the axle transfer is likely to IN around E2m on top of the E7rr being invested in the ZF produc tion line, again proving that no all of the massive Leyland finan cial programme is beinc invested in Lancashire.