Looking ahead
Page 46
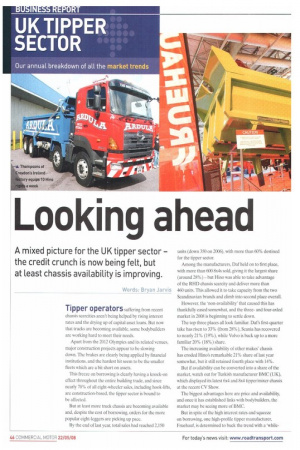
Page 47

If you've noticed an error in this article please click here to report it so we can fix it.
A mixed picture for the UK tipper sector the credit crunch is now being felt, but at least chassis availability is improving.
Words: Bryan Jarvis Tipper operators suffering from recent chassis scarcities aren't being helped by rising interest rates and the drying up of capital asset loans. But now that trucks are becoming available, some bodybuilders are working hard to meet their needs.
Apart from the 2012 Olympics and its related venues, major construction projects appear to be slowing down. The brakes are clearly being applied by financial institutions, and the hardest hit seem to be the smaller fleets which are a bit short on assets.
This freeze on borrowing is clearly having a knock-on effect throughout the entire building trade, and since nearly 70% of all eight-wheeler sales, including hook-lifts, are construction-based, the tipper sector is bound to be affected.
But at least more truck chassis are becoming available and, despite the cost of borrowing, orders for the more popular eight-leggers are picking up pace.
By the end of last year, total sales had reached 2,150 units (down 350 on 2006), with more than 60% destined for the tipper sector.
Among the manufacturers, Daf held on to first place, with more than 600 8x4s sold, giving it the largest share (around 28%) — but Hino was able to take advantage of the RHD chassis scarcity and deliver more than 460 units. This allowed it to take capacity from the two Scandinavian brands and climb into second place overall.
However. the non-availability' that caused this has thankfully eased somewhat, and the threeand four-axled market in 2008 is beginning to settle down.
The top three places all look familiar. Dars first-quarter take has risen to 33% (from 28%), Scania has recovered to nearly 21% (19%), while Volvo is back up to a more familiar 20% (18%) share.
The increasing availability of other makes' chassis has eroded Hino's remarkable 21% share of last year somewhat, but it still retained fourth place with 14%.
But if availability can be converted into a share of the market, watch out for Turkish manufacturer BNIC (UK), which displayed its latest 6x4 and 8x4 tipper/mixer chassis at the recent CV Show.
The biggest advantages here are price and availability, and once it has established links with bodybuilders, the market may be seeing more of B/v1C.
But in spite of the high interest rates and squeeze on borrowing, one high-profile tipper manufacturer, Fruehauf, is determined to buck the trend with a 'while you-wait' body fit scheme that joint managing director Matthew Wordsworth believes will make it market leader within three years.
He has backed his forecast with a i500,000 investment in a new steel body production line, which has a capacity of eight bodies a week on a single shift. The line includes a new 800-tonne press that can process 12m-long, lOmm steel plate, a new plasma cutter and body jigs, and has a capacity of eight bodies a week on a single shift.
Called Formula Fruehauf, the range comprises a 24yd" aluminium aggregate body, a 24y& aluminium insulated version with split tailgate, and a 20yd' high-grade steel muckaway body. Each stock unit is supplied with a Hyva FCT149 ram and a choice of sheeting systems.
With revised mountings and a number of additional 'bolt-on' options, the bodies should meet the needs of at least 75% of the rigid tipper market according to Freuhauf's other joint MD, Niall Wordsworth. Through the use of dedicated fitting teams, a tipper will be ready to drive away in not more than two hours.
Making headway
But while Fruehauf lays its plans to capture the tipper market, others are making headway in different directions.
Weightlifter, for example, has opened a factory at Dalmeny near Edinburgh, which will build the full range of rigid tippers and trailers in steel and aluminium.
The site will operate as a one-stop shop that can add all the options, carry out repairs and offer the usual backup for all Scottish hauliers within a radius of, say, 150 miles.
Products will include the Weightlifter PPG Smoothliner, Ultralight and bulkers in aluminium, as well as steel versions. Its target is to have a staff of 30 tradesmen mostly building between 125 and 175 tippers, hookand skip-loaders a year, but to also be involved in vehicle, chassis and sheet repairs.
Weightlifter's Dave Young has seen a growing need for reputable providers of local support in various outer regions. He is already looking to provide something similar in England's South-West.
Another busy producer of steel rigid tippers is Thompsons of Croydon, which began the year with a healthy order book — but according to sales director Scott Burton, its lead times were too far out.
Chassis deliveries have started to improve, but he anticipates slightly reduced sales this year, which will only start to pick up by next spring.
The Croydon factory and its Charlton Tippers Dover plant are bodying 35 vehicles a week and despite a slowing of the Irish construction market, Thompsons' Ireland factory equips 10 Hino rigids a week, some for the UK market.
An expanding sector is the grab tipper market, and as a UK Palfinger agent, it supplied 120 Epsilon grabs last year, so with the body systems it's a lucrative market.
Everyone's local supplier
Another company in sympathy with local requirements is Boweld Truck Bodies. It has developed a rather unusual method of becoming everyone's local bodybuilder, despite being located along the Dee estuary in Flintshire.
Like other suppliers, Boweld has been bedeviled by chassis shortages, although some makes — mainly Dafs, Scanias and Hinos — are filtering through a little bit faster.
But Boweld has countered the shortages by appointing several strategically placed engineering workshops as fitting agents, and delivering its pre-built tipping bodies for the agencies to fit onto their chassis.
This well spread group includes Logan Ingles in Cumbernauld; Colledge Trailers, Middlesbrough; Tadleybased Boulter Tippers; Neath Coachworks, Glamorgan; one in Cork, Ireland; and another to be appointed in South-East England. In effect, the customer is getting a high-quality steel body supplied on a local basis.
Boweld steel tipper bodies are produced in a new factory off the A55 at Halkyn. They're all jig-built and fully seam-welded using a series production process and then loaded four at a time on to a 44-tonne flatbed trailer.
Bolted securely together, they're then transported to the appropriate fitting centre, ready for mounting.
The factory is currently building eight to 12 tipper bodies a week for 8x4 rigids but Bowed expects the number to grow throughout the year.
"There are plenty of negative factors out there," says managing director George Bowden, "the credit squeeze, chassis and material shortages, and some formidable rivals — but this is our way of looking for success". •