Progress in Plywood Bodies
Page 68
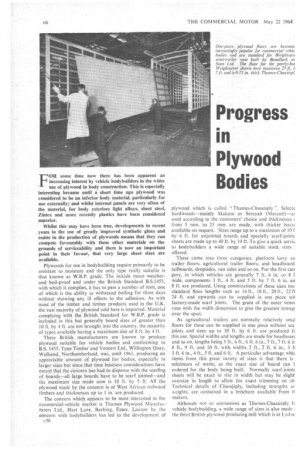
Page 69
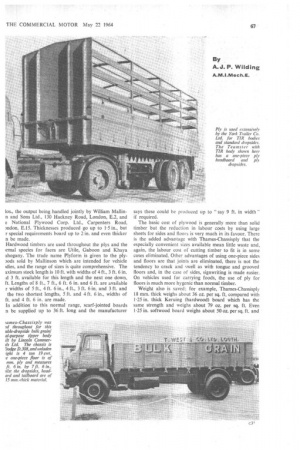
Page 70
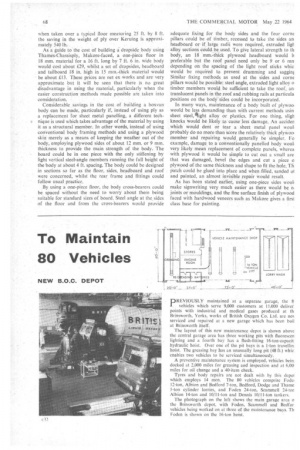
If you've noticed an error in this article please click here to report it so we can fix it.
By A. J. P. Wilding
A.110.1.141ech.E.
OR some time now there has been apparent an increasing interest by vehicle bodybuilders in the wider use of plywood in body construction. This is especially interesting because until a short time ago plywood was considered to be an inferior body Material, particularly for use externally; and whilst internal panels are very often of the material, for body exteriors light alloys, sheet steel,. Zintex and more recently plastics have been considered superior.
Whilst this may have been true, developments in recent years in the use of greatly improved synthetic glues and resins in the production of plywoods means that they can compete favourably with these other materials on the grounds of serviceability and there is now an important point in their favour, that very large sheet sizes are available.
Plywoods for use in bodybuilding require primarily to be resistant to moisture and the only type really suitable is that known as W.B.P. grade. The initials mean weatherand boil-proof and under the British Standard B.S.1455, with which it complies, it has to pass a number of tests, one of which is the ability to withstand boiling for three days without showing any ill effects to the adhesion. As with most of the timber and timber products used in the U.K. the vast majority of plywood sold here is imported. Material complying with the British Standard for W.B.P. grade is included in this but generally board sizes Of greater than 10 ft. by 4 ft. are not brought into the country, the majority of types available having a maximum size of 8 ft. by 4 ft
Three British manufacturers are known to produce plywood suitable for vehicle bodies and conforming to B.S. 1455. Tyne Timber and Veneers Ltd., Willington Quay, Wallsertd, Northumberland, Was, until 1961, producing an appreciable amount of plywood. for bodies, especially in larger sizes but since.that time business considerations have meant that the concern has had to dispense with the scarfing of boards—all large boards have to be scarf. jointed—and the maximum size made now is 10 ft. by 5 ft. All the plywood made by the concern is of West African redwood timbers and thicknesses up to 1 in. are produced. .
The concern which appears to be most interested in the commercial-vehicle market is Thames Plywood Manufacturers Ltd., Hart Lane, Barking, Essex. Liaison by the concern with bodybuilders has led to the development of c30 plywood which is called Thames-Chassisply ". Selectc hardwoods—mainly Makore or Serayah (Mera nti)—ar used according to the customers' choice and thicknesses from 5 mm. to 25 mm. are made, with thicker boarc available on request. Sizes range up to a maximum of 10 f by 6 ft. for unjointed boards and specially scarf-jointe sheets are made up to 40 ft. by 10 ft. To give a quick servic to bodybuilders a wide range of suitable stock sizes offered.
These come into three categories: platform lorry au trailer floors; agricultural trailer floors; and headboard tailboards, dropsides, van sides and so on. For the first cat( gory, in which vehicles are generally 7 ft. 6 in. or 8 f wide, components 3 ft., 4 ft. and 5 ft. by 7 ft. 6 in. an 8 ft. are produced. Using combinations of these sizes ma standard floor lengths such as 16 ft., 18 ft., 20 ft., 22 ft 24 ft. and upwards can be supplied . in one piece wit factory-made scarf joints. The grain of the outer venet runs with the width dimension to give the greatest strengt over the span.
As agricultural trailers are normally relatively srnal floors for these can be supplied in one piece without• sca joints and sizes up to 10 ft. by 6 ft. are produced ft this use. Special widths and lengths are made for headboan and so on, lengths being 5,ft., 6 ft., 6 ft. 6 in., 7 ft., 7 ft. 6 ir 8 ft., 9 ft. and 10 ft. with widths 2 ft., 2 ft. 6 in., 3 f 3 ft. 6 in., 4 ft., 5 ft. and 6 ft. A particular advantage whic stems from this great variety of sizes is that there is minimum of waste, as the exact size of board can I ordered for the body being built. Normally scarf-joint( sheets will he exact to size in width but may be slight Oversize in •length to allow for exact trimming on sit Technical details of -Chassisply, including strengths ar weights, are contained in a brochure available from ti makers.
Although not so convenient as Thames-Chassisply It vehicle bodybuilding, a -wide range of sizes is also made the third British plywood producing mill which is at Lydne
los., the output being handled jointly by William MaIlin n and Sons Ltd., 130 Hackney Road, London, E.2, and e National Plywood Corp. Ltd., Carpenters Road, )ndon, E.15. Thicknesses produced go up to 1.5 in., but r special requirements board up to 2 in, and even thicker n be made.
Hardwood timbers are used throughout the plys and the ormal species for faces are Utile, Gaboon and Khaya ahoga.ny. The trade name Plyform is given to the plyDods sold by Mallinson which are intended for vehicle dies, and the range of sizes is quite comprehensive. The aximum stock length is 10 ft. with widths of 4 ft., 3 ft. 6 in. id 3 ft. available for this length and the next one down, ft. Lengths of 8 ft., 7 ft., 6 ft. 6 in. and 6 ft. are available ✓ widths of 5 ft., 4 ft. 6 in., 4 ft., 3 ft. 6 in. and 3 ft. and the two shortest lengths, 5 ft. and 4 ft. 6 in., widths of ft. and 4 ft. 6 in. are made.
In addition to this normal range, scarf-jointed boards n be supplied up to 36 ft. Tong and the manufacturer
says these could be produced up to "say 9 ft. in width" if required.
The basic cost of plywood is generally more than solid timber but the reduction in labour costs by using large sheets for sides and floors is very much in its favour. There is the added advantage with Thames-Chassisply that the especially convenient sizes available mean little waste and, again, the labour cost of cutting timber to fit is in some eases eliminated. Other advantages of using one-piece sides and floors are that joints are eliminated, there is not the tendency to crack and swell as with tongue and grooved floors and, in the case of sides, signwriting is made easier. On vehicles used for carrying foods, the use of ply for floors is much more hygenic than normal timber.
Weight also is saved; for example, Thames-Chassisply 18 mm. thick weighs about 36 oz. per sq. ft. compared with 1-25 in. thick Keruing (hardwood) board which has the same strength and weighs about 79 oz. per sq. ft. Even 1.-25 in. softwood board weighs about 50 oz. per sq. ft. and when taken over a typical floor measuring 25 ft. by 8 ft. the saving in the weight of ply over Keruing is approximately 540 lb.
As a guide to the cost of building a dropside body using Thames-Chassisply, Makore-faced, a one-piece floor in 18 mm. material for a 16 ft. long by 7 ft. 6 in. wide body would cost about £29, whilst a set of dropsides, headboard and tailboard 18 in. high in 15 mm.-thick material would be about £13. These prices are net ex works and are very approximate but it will be seen that there is no great disadvantage in using the material, particularly when the easier construction methods made possible are taken into consideration.
Considerable savings in the cost of building a boxvan body can be made, particularly if, instead of using ply as a replacement for sheet metal panelling, a different technique is used which takes advantage of the material by using it as a structural member. In other words, instead of using conventional body framing methods and using a plywood skin merely as a means of keeping the weather out of the body, employing plywood sides of about 12 mm. or 9 rum. thickness to provide the main strength of the body. The board could be in one piece with the only stiffening by light vertical steel-angle members running the full height of the body at about 4 ft. spacing. The body could be designed in sections so far as the floor, sides, headboard and roof were concerned, whilst the rear frame and fittings could follow usual practice.
By using a one-piece floor, the body cross-bearers could be spaced without the need to worry about them being suitable for standard sizes of board. Steel angle at the sides of the floor and from the cross-bearers would provide
adequate fixing for the body sides and the four come pillars could be of .timber, recessed to take the sides an headboard orif large radii were required, extruded lie alloy sections could, be used. To give lateral strength to th body, an 18 'mm.-thick plywood headboard would b preferable but the roof panel need only be 9 or 6 run depending on the spacing of the light roof sticks whic would be required to prevent drumming and sagging Similar fixing methods as used at the sides and come pillars would be possible: steel angle, extruded light alloy o timber members would be sufficient to take the roof, an translucent Panels in the roof and rubbing rails at particula positions on the body' sides could be incorporated.
In many ways, maintenance of a body built of plywoo. would be less demanding than with current methods usin sheet steel, gight alloy or plastics. For one thing, sligh knocks would be likely to cause Jess damage. An accider which would dent or tear a .sheet metal panel wout probably do no more-than Score the relatively thick plywoo member • and repairing would, generally be simpler. Fe example, damage to a conventionally panelled body •woul very likely mean replacement of complete panels, wherea with plywood it would be simple to cut out a small are that was damaged, bevel the edges and cut a piece o plywood of the same thickness and shape to fit the hole. Th patch could be glued into place and when filled, sanded c}l and painted, an almost invisible repair would result.
As has been stated earlier, using one-piece sides wont, make signwriting very much easier as there would be 'n. joints or mouldings, and the fine surface finish of plywood faced with hardwood veneers such .as Makore gives a first class base for painting.