MOULDING A FUTUR
Page 126
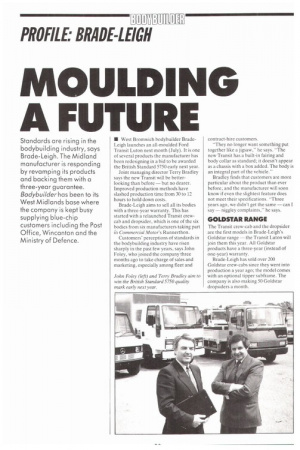
Page 127
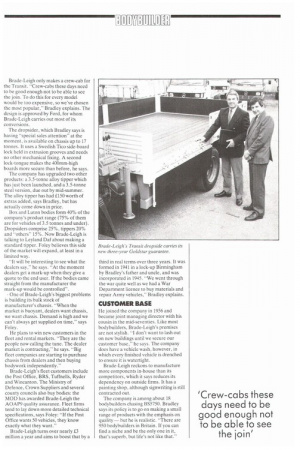
If you've noticed an error in this article please click here to report it so we can fix it.
• West Bromwich bodybuilder BradeLeigh launches an all-moulded Ford Transit Luton next month (July). It is one of several products the manufacturer has been redesigning in a bid to be awarded the British Standard 5750 early next year.
Joint managing director Terry Bradley says the new Transit will be betterlooking than before — but no dearer. Improved production methods have slashed production time from 30 to 12 hours to hold down costs.
Brade-Leigh aims to sell all its bodies with a three-year warranty. This has started with a relaunched Transit crewcab and dropsider, which is one of the six bodies from six manufacturers taking part ih Commercial Motor's Runnerthon.
Customers' perceptions of standards in the bodybuilding industry have risen sharply in the past few years, says John Foley, who joined the company three months ago to take charge of sales and marketing, especially among fleet and John Foley (left) and Terry Bradley aim to win the British Standard 5750 quality mark early next year. "They no longer want something put together like a jigsaw," he says. "The new Transit has a built-in fairing and body collar as standard; it doesn't appear as a chassis with a box added. The body is an integral part of the vehicle."
Bradley finds that customers are more particular about the product than ever before, and the manufacturer will soon know if even the slightest feature does not meet their specifications. -Three years ago, we didn't get the same — can I say — niggley complaints," he says.
The Transit crew-cab and the dropsider are the first models in Brade-Leigh's Goldstar range — the Transit Luton will join them this year. All Goldstar products have a three-year (instead of one-year) warranty.
Brade-Leigh has sold over 200 Goldstar crew-cabs since they went into production a year ago; the model comes with an optional tipper subframe. The company is also making 50 Goldstar dropsiders a month. Brade-Leigh only makes a crew-cab for the Transit. "Crew-cabs these days need to be good enough not to be able to see the join. To do this for every model would be too expensive, so we've chosen the most popular," Bradley explains. The design is approved by Ford, for whom Brade-Leigh carries out most of its conversions.
The dropsider, which Bradley says is having "special sales attention" at the moment, is available on chassis up to 17 tonnes. It uses a Swedish Tico side-board lock held in extrusion grooves and needs no other mechanical fixing. A second lock-tongue makes the 400mm-high boards more secure than before, he says.
The company has upgraded two other products: a 3.5-tonne alloy tipper which has just been launched, and a 3.5-tonne steel version, due out by mid-summer. The alloy tipper has had £150 worth of extras added, says Bradley, but has actually come down in price.
Box and Luton bodies form 40% of the company's product range (75% of them are for vehicles of 3.5 tonnes and under). Dropsiders comprise 25%. tippers 20% and "others" 15%. Now Brade-Leigh is talking to Leyland Daf about making a standard tipper. Foley believes this side of the market wilt expand, at least in a limited way.
It will be interesting to see what the dealers say," he says. "At the moment dealers get a mark-up when they give a quote to the end user. If the bodies came straight from the manufacturer the mark-up would be controlled".
• One of Brade-Leigh's biggest problems is building its bulk stock of manufacturer's chassis. "When the market is buoyant, dealers want chassis, we want chassis. Demand is high and we can't always get supplied on time," says Foley.
He plans to win new customers in the fleet and rental markets. "They are the people now calling the tune. The dealer market is contracting," he says. "Big fleet companies are starting to purchase chassis from dealers and then buying bodywork independently."
Brade-Leigh's fleet customers include the Post Office, BRS, Tuffnellk, Ryder and Wincanton. The Ministry of Defence, Crown Suppliers and several county councils also buy bodies: the MOD has awarded Brade-Leigh the AOAP9 quality assurance. Fleet firms tend to lay down more detailed technical specifications, says Foley: "If the Post Office wants 50 vehicles, they know exactly what they want."
Brade-Leigh turns over nearly £3 million a year and aims to boost that by a
third in real terms over three years. It was formed in 1941 in a lock-up Birmingham by Bradley's father and uncle, and was incorporated in 1945. "We went through the war quite well as we had a War Department licence to buy materials and repair Army vehicles," Bradley explains.
He joined the company in 1956 and became joint managing director with his cousin in the mid-seventies. Like most bodybuilders, Brade-Leigh's premises are not stylish. "1 don't want to lash out on new buildings until we secure our customer base," he says. The company does have a vehicle wash, however, in which every finished vehicle is drenched to ensure it is watertight.
BradeLeigh reckons to manufacture more components in-house than its competitors, which it says reduces its dependency on outside firms. It has a painting shop, although signwriting is still contracted out.
The company is among about 18 bodybuilders chasing BS5750. Bradley says its policy is to go on making a small range of products with the emphasis on quality — but he is realistic. "There are 950 bodybuilders in Britain. If you can find a niche and be the only one in it, that's superb, but life's not like that.''