HINTS ON MAINTENANCE,
Page 26
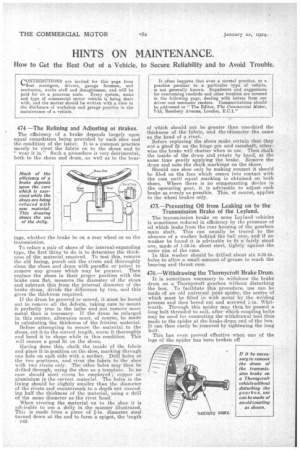
If you've noticed an error in this article please click here to report it so we can fix it.
How to Get the Best Out of a Vehicle, to Secure Reliability and to Avoid Trouble.
CONTRIBUTIONS are invited for this page from fleet rnavagers, drivers, garage foremen, and mechanics, works staff and draughtsmen; and will be paid for on a generous scale. Every system, make and type of commercial motor vehicle is being dealt with, and the matter should be written with a view to the disclosure of workshop and garage practice in the maintenance of a vehicle. It often happens that even a normal practice, or a practice peculiar to a particular type of vehicle, is not generally known. Expedients and suggestions for overcoming roadside and other troubles are covered in the following page, dealing with letters from our driver and mechanic readers. Communications should be addressed to "The Editor The Commercial Motor, 7-15, Rosebery Avenue, London, E.C.1."
474 —The Relining and Adjusting ot Brakes.
The efficiency of a brake depends largely upon equal retardation being provided by each shoe and the condition of the latter. It is a common practice merely to rivet the fabric on to the shoes and to " wear it in." Such a procedure is very detrimental, both to the shoes and drum, as well as to the bear ings, whether the biake transmission.
To reface a pair of shoes of the internal-expanding type, the first thing to do is to determine the thickness of the material required. To test this, remove the old facing, punch out the rivets and thoroughly clean the shoes and drum with paraffin or petrol to remove any grease which may be present. Then replace the shoes in their proper position with the brake cam fiat, measure the diameter of the shoes and subtract this from the internal diameter of the brake drum, divide the difference by two, and this gives the thickness required.
If the drum be grooved or scored, it must be bored out to remove all the defects, taking care to mount it perfectly true in the lathe and not remove more metal than is necessary. If the drum be enlarged in this matter, allowance must, of course, be made in calculating the thickness of the friction material.
Before attempting to secure the material to the shoes, cut it to the correct length, warm it thoroughly and bend it to shape while in this condition. This will ensure a good fit on the shoes.
Having done this, chalk the inside of the fabric and place it in position on the shoe, marking through one hole on each side with a scriber. Drill holes at the two positions, and rivet the fabric to the shoe with two rivets only. The other holes may then be drilled through, using the shoe as a template. In no ease should steel rivets be employed ; copper or aluminium is the correct material. The holes in the lining should be slightly smaller than the diameter of the rivets and countersunk to a depth not exceeding half the thickness of the material, using a drill of the same diameter as the rivet head.
When riveting the material on to the shoe it is advisable to use a dolly in the manner illustrated. This is made from a piece of 1-in. diameter steel turned down at the end to form a spigot, the 1ength
042
of which should not be greater than one-third the thickness of the fabric, and the 'diameter the same as the head of a rivet.
Before replacing the shoes make certain that they are a geod fit on the hinge pin and camshaft, otherwise the brake will chatter when in use. Then chalk the inside of the drum and rotate by hand, at the same time gently applying the brake. Remove the drum and note the chalk markings on the shoes. Should one shoe only be making contact it should be filed on the face which comes into contact with the cam until equal marking is obtained on both shoes. Where there is no compensating device in the operating gear, it is advisable to adjust each brake as evenly as possible. This, of course, applies to the wheel brakes only.
475.—Preventing Oil from Leaking on to the Transmission Brake of the Leyland.
The transmission brake on some Leyland vehicles is sometimes reduced in efficiency by the presence of oil which leaks from the rear housing of the gearbox main shaft. This can usually be traced to the absence of a washer behind the ball race, and if no washer be found it is advisable to fit a fairly stout one, made of 1-32-in, sheet steel, tightly against the outer rim of the race.
In this washer should be drilled about six 3-32-in. holes to allow a small amount of grease to reach the bearing and thrust race.
476.—Withdrawing the Thornycroft Brake Drum.
It is sometimes necessary to withdraw the brake drum on a Thornycroft gearbox without disturbing the box. To facilitate this procedure, use can be made of an old universal joint spider, the centre of which must be filled in with metal by the welding process and then bored out and screwed 1-in. Whitworth. Through this spider may then be passed a long bolt threaded to suit, after which coupling bolts may be used for connecting the withdrawal tool thus made to the spider at the brake-drum end of the box. It can then easily be removed by tightening the long bolt.
This has even proved effective when one of the legs of the spider has been broken off