LOST FOLPINICIO
Page 60
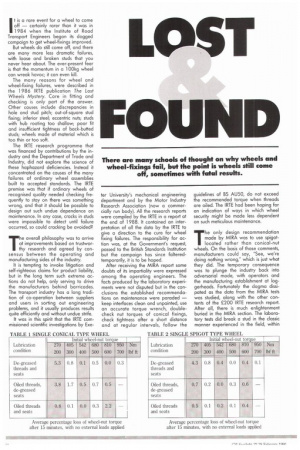
Page 61
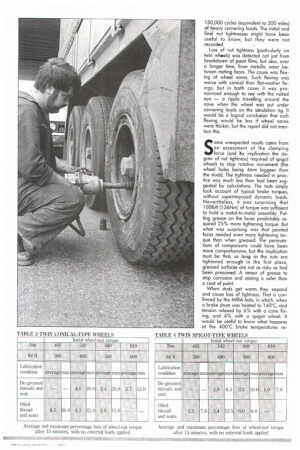
Page 62
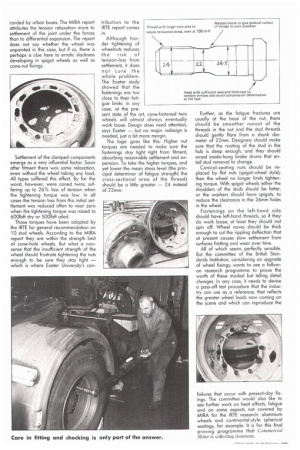
If you've noticed an error in this article please click here to report it so we can fix it.
There are many schools of thought on why wheels and wheel-fixings fail, but the point is wheels still come off, sometimes with fatal results.
It is a rare event for a wheel to come off certainly rarer than it was in 1984 when the Institute of Road Transport Engineers began its dogged campaign to get wheel-fixings improved.
But wheels do still come off, and there are many more less dramatic failures, with loose and broken studs that you never hear about. The ever-present fear is that the momentum in a 100kg wheel can wreak havoc; it can even kill.
The many reasons for wheel and wheel-fixing failures, were described in the 1986 IRTE publication The Lost Wheels Mystery. Care in fitting and checking is only part of the answer. Other causes include discrepancies in hole and stud pitch; out-of-square stud fixing; inferior steel; eccentric nuts; studs with hub rooting too shallow; poor fit and insufficient tightness of back-butted studs; wheels made of material which is too thin or too soft.
The IRTE research programme that was financed by contributions by the industry and the Department of Trade and Industry, did not explore the science of these haphazard deficiencies. Instead it concentrated on the causes of the many failures of ordinary wheel assemblies built to accepted standards. The IRTE premise was that if ordinary wheels of recognised quality needed checking frequently to stay on there was something wrong, and that it should be possible to design out such undue dependence on maintenance_ In any case, cracks in studs were impossible to detect until failure occurred, so could cracking be avoided? The overall philosophy was to arrive at improvements based on trustworthy research and agreed by consensus between the operating and manufacturing sides of the industry.
It is tempting to invoke litigation and self-righteous claims for product liability, but in the long term such extreme actions do not help, only serving to drive the manufacturers behind barricades. The transport industry has a long tradition of co-operation between suppliers and users in sorting out engineering problems, and it usually produces results quite efficiently and without undue strife.
It was in this spirit that the IRTE commissioned scientific investigations by Exe
ter University's mechanical engineering department and by the Motor Industry Research Association (now a commercially run body). All the research reports were compiled by the IRTE in a report at the end of 1988. It contained an interpretation of all the data by the IRTE to give a direction to the cure for wheel fixing failures. The responsibility for action was, at the Government's request, passed to the British Standards Institution but the campaign has since falteredtemporarily, it is to be hoped.
After receiving the MIRA report some doubts of its impartiality were expressed among the operating engineers. The facts produced by the laboratory experiments were not disputed but in the conclusions the established recommendations on maintenance were paraded keep interfaces clean and unpainted, use an accurate torque wrench, doublecheck nut torques of conical fixings, check tightness after a short distance and at regular intervals, follow the guidelines of BS AU50, do not exceed the recommended torque when threads are oiled. The IRTE had been hoping for an indication of ways in which wheel security might be made less dependent on such meticulous maintenance.
The only design recommendation made by MIRA was to use spigotlocated rather than conical-nut wheels. On the basis of those comments, manufacturers could say, "See, we're doing nothing wrong," which is just what they did. The temporary consequence was to plunge the industry back into adversarial mode, with operators and the manufacturing establishment at loggerheads. Fortunately the dogma dissipated as the data from the MIRA tests was studied, along with the other contents of the £200 IRTE research report. After all, there is much enlightenment buried in the MIRA section. The laboratory tests did break a stud in the classic manner experienced in the field, within 150,000 cycles (equivalent to 300 miles) of heavy cornering loads. The initial and final nut tightnesses might have been useful to know, but they were not recorded.
Loss of nut tightness (particularly on twin wheels) was detected not just from breakdown of paint films, but also, over a longer time, from metallic wear between mating faces. The cause was flexing of wheel naves. Such flexing was worse with conical than flat-washer fixings, but in both cases it was pronounced enough to see with the naked eye — a ripple travelling around the nave when the wheel was put under cornering loads on the simulation rig. It would be a logical conclusion that such flexing would be less if wheel naves were thicker, but the report did not mention this.
Some unexpected results came from an assessment of the clamping force (and by implication the degree of nut tightness) required of spigot wheels to stop rotative movement (the wheel holes being 4mm biggeer than the studs). The tightness needed in practice was much less than had been suggested by calculations. The tests simply took account of typical brake torques, without superimposed dynamic loads. Nevertheless, it was surprising that 100Ibft (136Nm) of torque was sufficient to hold a metal-to-metal assembly. Putting grease on the faces predictably required 25% more tightening torque. But what was surprising was that painted faces needed even more tightening torque than when greased. The permutations of comparisons could have been more comprehensive, but the implication must be that, so long as the nuts are tightened enough in the first place, greased surfaces are not as risky as had been presumed. A smear of grease to stop corrosion and seizing is safer than a coat of paint.
When studs get warm they expand and cause loss of tightness. That is confirmed by the MIRA tests, in which, when a brake drum was heated to 140°C, stud tension relaxed by 6% with a cone fixing, and 4% with a spigot wheel. It would be useful to know what happens at the 400°C brake temperatures re corded by urban buses. The MIRA report attributes the tension relaxation more to settlement of the joint under the forces than to differential expansion. The report does not say whether the wheel was unpainted in this case, but if so, there is perhaps a clue here to erratic slackness developing in spigot wheels as well as cone-nut fixings.
Settlement of the clamped components emerge as a very influential factor. Soon after fitment there was some relaxation, even without the wheel taking any load. All types suffered this effect. By far the worst, however, were coned twins, suffering up to 26% loss of tension when the tightening torque was low. In all cases the tension loss from this initial settlement was reduced often to near zero when the tightening torque was raised to 600Ibft dry or 50016ft oiled.
Those torques have been adopted by the IRTE for general recommendation on 10 stud wheels. According to the MIRA report they are within the strength limit of cone-hole wheels. But what a nonsense that the insufficient strength of the wheel should frustrate tightening the nuts enough to be sure they stay tight — which is where Exeter University's con
tribution to the IRTE report comes in.
Although harder tightening of wheelnuts reduces the risk of tension-loss from settlement, it does not cure the whole problem. The Exeter study showed that the fastenings are too close to their fatigue limits: in any case, at the present state of the art, cone-fastened twin wheels will almost always eventually work loose. Design does need attention, says Exeter — but no major redesign is needed, just a bit more margin.
The logic goes like this: Higher nut torques are needed to make sure the fastenings stay tight right from fitment, absorbing reasonable settlement and expansion. To take the higher torques, and yet lower the mean stress level (the principal determiner of fatigue strength) the cross-sectional area of the threads should be a little greater — 24 instead of 22mm. Further, as the fatigue fractures are usually at the base of the nut, there should be smoother runout of the threads in the nut and the stud threads should gently flare from a shank diameter of 22mm. Designers should make sure that the rooting of the stud in the hub is deep enough, and they should avoid inside-hung brake drums that entail stud removal to change.
Conical-seating nuts should be replaced by flat nuts (spigot-wheel style); then the wheel no longer limits tightening torque. With spigot wheels either the shoulders of the studs should be fatter, or the washers should have spigots, to reduce the clearance in the 26mm holes in the wheel.
Fastenings on the left-hand side should have left-hand threads, so if they do work loose, at least they should not spin off. Wheel naves should be thick enough to cut the rippling deflection that at present causes slow settlement from surfaces fretting and wear over time.
All of which seems perfectly sensible. But the committee of the British Standards Institution, considering an upgrade of wheel fixings, wants to see a followon research programme to prove the worth of these modest but telling detail changes. In any case, it needs to devise a pass-off test procedure that the industry can use as a reference, that reflects the greater wheel loads now coming on the scene and which can reproduce the
failures that occur with present-day fixings. The committee would also like to see further work on heat effects, fatigue and on some aspects not covered by MIRA for the IRTE research: aluminium wheels and continental-style spherical seatings, for example. It is for this final proving programme that Commercial Motor is collecting donations.