SAFETY FIRST TIPPER STUDY
Page 158
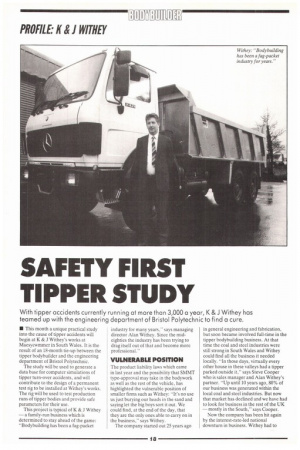
Page 159
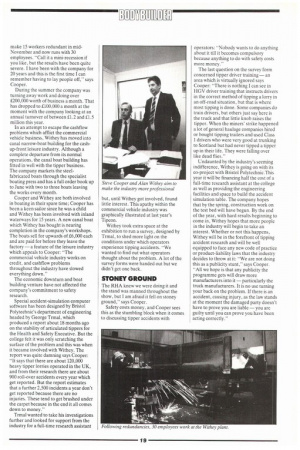
If you've noticed an error in this article please click here to report it so we can fix it.
With tipper accidents currently running at more than 3,000 a year, K & J Withey has teamed up with the engineering department of Bristol Polytechnic to find a cure.
• This month a unique practical study into the cause of tipper accidents will begin at K & J Withey's works at Maesycwmmer in South Wales. It is the result of an 18-month tie-up between the tipper bodybuilder and the engineering department of Bristol Polytechnic.
The study will be used to generate a data base for computer simulations of tipper turn-over accidents, and will contribute to the design of a permanent test rig to be installed at Withey's works. The rig will be used to test production runs of tipper bodies and provide safe parameters for their use.
This project is typical of K & J Withey — a family-run business which is determined to stay ahead of the game: "Bodybuilding has been a fag-packet industry for many years," says managing director Alan Withey. Since the mideighties the industry has been trying to drag itself out of that and become more professional,
VULNERABLE POSITION
The product liability laws which came in last year and the possibility that SMMT type-approval may take in the bodywork as well as the rest of the vehicle, has highlighted the vulnerable position of smaller firms such as Withey: "It's no use us just burying our heads in the sand and saying let the big boys sort it out. We could find, at the end of the day, that they are the only ones able to carry on in the business," says Withey.
The company started out 25 years ago
in general engineering and fabrication, but soon became involved full-time in the tipper bodybuilding business. At that time the coal and steel industries were still strong in South Wales and Withey could find all the business it needed locally. "In those days, virtually every other house in these valleys had a tipper parked outside it," says Steve Cooper who is sales manager and Alan Withey's partner. "Up until 10 years ago, 80% of our business was generated within the local coal and steel industries. But now that market has declined and we have had to look for business in the rest of the UK — mostly in the South," says Cooper.
Now the company has been hit again by the interest-rate-led national downturn in business. Withey had to make 15 workers redundant in midNovember and now runs with 30 employees. "Call it a mini-recession if you like, but the results have been quite severe. I have been with the company for 20 years and this is the first time I can remember having to lay people off," says Cooper.
During the summer the company was turning away work and doing over £200,000 worth of business a month. That has dropped to £100,000 a month at the moment with the company looking at an annual turnover of between £.1.2 and £15 million this year.
In an attempt to escape the cashflow problems which afflict the commercial vehicle business, Withey has moved into canal narrow-boat building for the cashup-front leisure industry. Although a complete departure from its normal operations, the canal boat building has fitted in well with the tipper business. The company markets the steelfabricated boats through the specialist boating press and has a full order book up to June with two to three boats leaving the works every month.
Cooper and Withey are both involved in boating in their spare time; Cooper has been a keen sailor since he was a child and Withey has been involved with inland waterways for 15 years. A new canal boat which Withey has bought is nearing completion in the company's workshops. The boats sell for upwards of £6,000 each and are paid for before they leave the factory — a feature of the leisure industry which appeals to Cooper: "The commercial vehicle industry works on credit, and cashflow problems throughout the industry have slowed everything down."
The economic downturn and boat building venture have not affected the company's commitment to safety research.
Special accident-simulation computer software has been designed by Bristol Polytechnic's department of engineering headed by George Trmal, which produced a report about 18 months ago on the stability of articulated tippers for the Health and Safety Executive. But the college felt it was only scratching the surface of the problem and this was when it became involved with Withey. The report was quite damning says Cooper: "It says that there are about 120,000 heavy tipper lorries operated in the UK, and from their research there are about 900 roll-over accidents every year which get reported. But the report estimates that a further 2,500 incidents a year don't get reported because there are no injuries. These tend to get brushed under the carpet because in the end it all comes down to money."
Trmal wanted to take his investigations further and looked for support from the industry for a full-time research assistant but, until Withey got involved, found little interest. This apathy within the commercial vehicle industry was graphically illustrated at last year's Tipcon.
Withey took extra space at the exhibition to run a survey, designed by Trmal, to shed more light on the conditions under which operators experience tipping accidents. "We wanted to find out what operators thought about the problem. A lot of the survey forms were handed out but we didn't get one back.
STONEY GROUND
The RHA knew we were doing it and the stand was manned throughout the show, but I am afraid it fell on stoney ground," says Cooper.
Safety costs money, and Cooper sees this as the stumbling block when it comes to discussing tipper accidents with operators: "Nobody wants to do anything about it till it becomes compulsory because anything to do with safety costs more money."
The last question on the survey form concerned tipper driver training — an area which is virtually ignored says Cooper: "There is nothing I can see in HGV driver training that instructs drivers in the correct method of tipping a lorry in an off-road situation, but that is where most tipping is done. Some companies do train drivers, but others just say here is the truck and that little knob raises the tipper. When the miners' strike happened a lot of general haulage companies hired or bought tipping trailers and used Class 1 drivers who were very good at trunking to Scotland but had never tipped a tipper up in their life. They were falling over like dead flies."
Undaunted by the industry's seeming indifference, Withey is going on with its co-project with Bristol Polytechnic.This year it will be financing half the cost of a full-time research assistant at the college as well as providing the engineering facilities and space to build the accident simulation table. The company hopes that by the spring, construction work on the test bed will have begun. By the end of the year, with hard results beginning to come in, Withey hopes that more people in the industry will begin to take an interest. Whether or not this happens, Withey will be in the forefront of tipping accident research and will be well equipped to face any new code of practice or product-liability laws that the industry decides to throw at it: "We are not doing this as a publicity stunt," says Cooper. "All we hope is that any publicity the programme gets will draw more manufacturers into it — particularly the truck manufacturers. It is no use turning your back on the problem. If there is an accident, causing injury, as the law stands at the moment the damaged party doesn't have to prove you are liable — you are guilty until you can prove you have been acting correctly."