TRANSPORTER: TOP SERVICE
Page 46
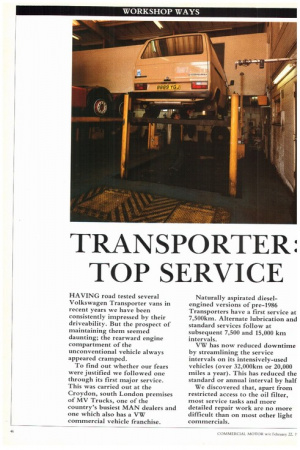
Page 47
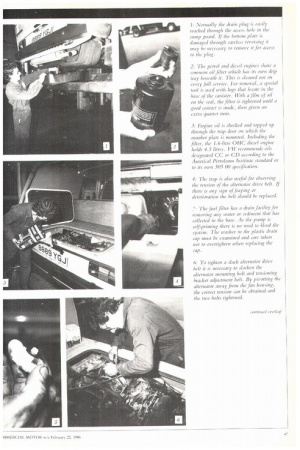
Page 48
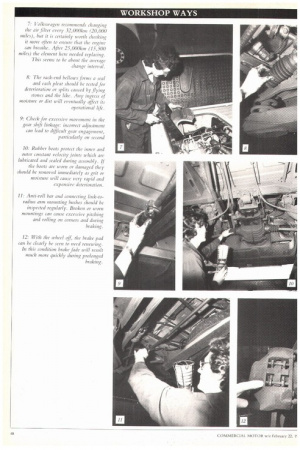
Page 49
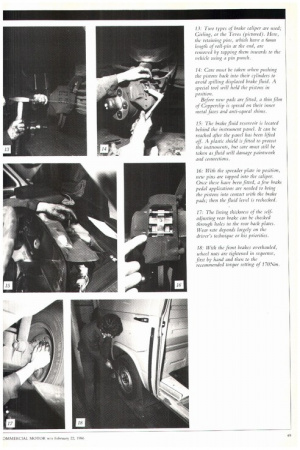
If you've noticed an error in this article please click here to report it so we can fix it.
HAVING road tested several Volkswagen Transporter vans in recent years we have been consistently impressed by their driveability. But the prospect of maintaining them seemed daunting; the rearward engine compartment of the unconventional vehicle always appeared cramped.
To find out whether our fears were justified we followed one through its first major service. This was carried out at the Croydon, south London premises of MV Trucks, one of the country's busiest MAN dealers and one which also has a VW commercial vehicle franchise. Naturally aspirated dieselengined versions of pre-1986 Transporters have a first service at 7,500km. Alternate lubrication and standard services follow at subsequent 7,500 and 15,000 km intervals.
VW has now reduced downtime by streamlining the service intervals on its intensively-used vehicles (over 32,000km or 20,000 miles a year). This has reduced the standard or annual interval by half We discovered that, apart from restricted access to the oil filter, most service tasks and more detailed repair work are no more difficult than on most other light commercials.
1: Normally the drain plug is easily reached thrott,Qh the at•CeSS hole in the sump guard. If the bottom plate is damaged thrallgh careless reversing it may he necessary to remove it for access to the pitIg.
2.. The petrol and diesel engines share a fannnanoil filter which has its otiM drip tray beneath it. This is cleaned out on every .hill s'rvice. For removal, a special tool is used with lugs that locate in the hose of the amister. With a film of oil on the seal, the filter is lightened until a ,good contact is made, then ,ivettan extra cplarter nem 3: Engine oil is checked and topped up through the trap door on which the number plate is mounted. Including the .filter, the 1.6-litre OHC diesel engine holds 4.5 litres. VW recommetuis oils designated CC or CD according to the Anterical Petroleum Institute standard or to its own 505 00 specification.
4: The trap is also useful for observing the tension of the alternator drive belt. If there is any sign of fraying or deterioration the belt should be replaced.
'thefile! filter has a drain facility for removing any water or sediment that has collected in the base. AS the pump is self-priming there is no need to bleed the system. The washer in the plastic drain cap must be examined and care taken not to overtighten when replacing the cap.
6: To tighten a slack alternator drive belt it is Necessary to slacken the alternator mounting ho it and tensioning bracket adjustment bolt. By pivotting the altenlafor away._from the fait housing, the correct tension can K. Obtained and the two bolts tightened. 7: Volkswagen recommends changing the air filter every 32,000km (20,000 miles), but it is certainly worth checking it more often to ensure that the engine can breathe. After 25,000km (15,500 miles) the element here needed replacing. This seems to be about the average change interval.
8: The rack-end bellows forms a seal and each pleat should be tested for deterioration or splits caused by flying stones and the like. Any ingress of inoisture or dirt will eventually affect its operational life.
9: Check for excessive movement in the gear 510 linkage: incorrect adjustment can lead to difficult gear engagement, particularly on second 10: Rubber boots protect the inner and outer constant velocity joints which are lubricated and sealed during assembly. If the boots are worn or damaged they should be removed immediately as grit or moisture will cause very rapid and expensive deterioration.
11: Anti-roll bar and connecting link-toradius arm mounting bushes should be inspected regularly. Broken or worn mountings can cause excessive pitching and rolling on corners and during braking.
12: With the wheel off, the brake pad can be clearly be seen to need renewing. In this condition brake fade will result much more quickly during prolonged braking. 13: Two types of brake caliper are used; Girling, or the Teves (pictured). Here, the retaining pins, Lvhich have a 6m in length of roll-pin at the end, are removed by tapping them inwards to the vehicle using a pin punch.
14: Care must be taken when pushing the pistons back into their cylinders to avoid spilling displaced brake _fluid. A special tool hold the pistons in position.
Before new pads are fitted, a thin film of Copperslip is spread on their inner metal _faces and anti-squeal shims.
15: The brake fluid reservoir is located behind the instrument panel. It can be reached after the panel has been lifted off. A plastic shield is fitted to protect the instruments, but care must still be taken as fluid will damage paintwork and connections.
16: With the spreader plate in position, new pins are tapped into the caliper. Once these have been _fitted, a few brake pedal applications are needed to bring the pistons into contact with the brake pads; then the fluid level is rechecked.
17: The lining thickness of the selfadjusting rear brake Can be checked through holes in the rear back plates. Wear rate depends hugely on the driver's technique or his priorities.
18: With the front brakes overhauled, wheel nuts are tightened in sequence, first by hand and then to the recommended torque setting of 170Ntn.