Service costs as much as fuel
Page 86
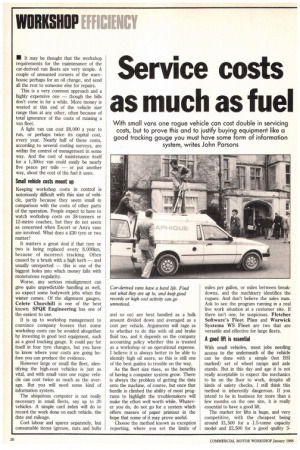
Page 87
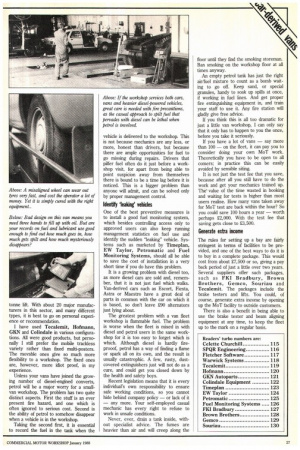
If you've noticed an error in this article please click here to report it so we can fix it.
With small vans one rogue vehicle can cost double in servicing costs, but to prove this and to justify buying equipment like a good tracking gauge you must have some form of information system, writes John Parsons • It may be thought that the workshop requirements for the maintenance of the car-derived van fleets are very simple. A couple of unwanted corners of the warehouse perhaps for an oil change, and send all the rest to someone else for repairs.
This is a very common approach and a highly expensive one — though the bills don't come in for a while. More money is wasted at this end of the vehicle size range than at any other, often because of total ignorance of the costs of running a van fleet.
A light van can cost £8,000 a year to run, or perhaps twice its capital cost, every year. Nearly half of these costs, according to several costing surveys, are within the control of management in some way. And the cost of maintenance itself for a 1,300cc van could easily be nearly five pence per mile — or put another way, about the cost of the fuel it uses.
Small vehicle costs mount up Keeping workshop costs in control is notoriously difficult with this size of vehicle, partly because they seem small in comparison with the costs of other parts of the operation_ People expect to have to watch workshop costs on 38-tonners or 12-metre coaches, but they do not seem as concerned when Escort or Astra vans are involved. What does a 230 tyre or two matter?
It matters a great deal if that tyre or two is being replaced every 8,0001cm, because of incorrect tracking. Often caused by a brush with a high kerb — and usually unreported — this is one of the biggest holes into which money falls with monotonous regularity.
Worse, any serious misalignment can give quite unpredictable handling as well, so expect some bodywork jobs when the winter comes. Of the alignment gauges, Celete Churchill is one of the best known. SPQR Engineering has one of the easiest to use.
It is up to workshop management to convince company bosses that some workshop costs can be avoided altogether by investing in good test equipment, such as a good tracking gauge. It could pay for itself in four tyre changes, but you have to know where your costs are going before you can produce the evidence.
However large or small the fleet, identifying the high-cost vehicles is just as vital, and with small vans one rogue vehicle can cost twice as much as the average. But you will need some kind of information system.
The ubiquitous computer is not really necessary in small fleets, say up to 20 vehicles. A simple card index will do to record the work done on each vehicle, the date and mileage.
Cost labour and spares separately, but consumable items (grease, nuts and bolts and so on) are best handled as a bulk amount divided down and averaged as a cost per vehicle. Arguments will rage as to whether to do this with oil and brake fluid too, and it depends on the company accounting policy whether this is treated as a workshop or an operational expense. I believe it is always better to be able to identify high oil users, as this is still one of the best guides to trouble on the way.
As the fleet size rises, so the benefits of having a computer system grow. There is always the problem of getting the data onto the machine, of course, but once that hurdle is climbed the ability of most programs to highlight the troublemakers will make the effort well worth while. Whatever you do, do not go for a system which offers masses of paper printout in the hope that some of it may prove useful.
Choose the method known as exception reporting, where you set the limits of miles per gallon, or miles between breakdowns, and the machinery identifies the rogues. And don't believe the sales man. Ask to see the program running in a real live work situation at a customer site. If there isn't one, be suspicious. Fletcher Software's Fleet Plan and Warwick Systems WS Fleet are two that are versatile and effective for large fleets.
A good lift is essential With small vehicles, most jobs needing access to the underneath of the vehicle can be done with a simple (but BSI marked) set of wheel ramps and axle stands. But in this day and age it is not really acceptable to expect the mechanics to lie on the floor to work, despite all kinds of safety checks, I still think this method is inherently dangerous. If you intend to be in business for more than a few months on the one site, it is really essential to have a good lift.
The market for lifts is huge, and very competitive, with the cheapest being around £1,500 for a 1.5-tonne capacity model and £2,500 for a good quality 3 tonne lift. With about 20 major manufacturers in this sector, and many different types, it is best to go on personal experience or recommendation.
I have used Tecalemit, Hofmann, GliN and Colindale in various configurations. All were good products, but personally I still prefer the mobile trackless variety rather than fixed multi-posters. The movable ones give so much more flexibility to a workshop. The fixed ones are, however, more idiot proof, in my experience.
Unless your vans have joined the growing number of diesel-engined converts, petrol will be a major worry for a smallvan workshop. The problem has two quite distinct aspects. First the stuff is an ever present fire hazard, and one which is often ignored to serious cost. Second is the ability of petrol to somehow disappear when a vehicle is in the workshop.
Taking the second first, it is essential to record the fuel in the tank when the
vehicle is delivered to the workshop. This is not because mechanics are any less, or more, honest than drivers, but because there are ample opportunities for fuel to go missing during repairs, Drivers that pilfer fuel often do it just before a workshop visit, for apart from being able to point suspicion away from themselves there is bound to be a time lag before it is noticed. This is a bigger problem than anyone will admit, and can be solved only by proper management control.
Identify 'leaking' vehicles One of the best preventive measures is to install a good fuel monitoring system, which besides controlling access only to approved users can also keep running management statistics on fuel use and identify the sudden "leaking" vehicle. Systems such as marketed by Timeplan, EW Taylor, Petrornatic and Fuel Monitoring Systems, should all be able to save the cost of installation in a very short time if you do have this problem.
It is a growing problem with diesel too, as more diesel cars are sold and, remember, that it is not just fuel which walks. Van-derived cars such as Escort, Fiesta, Astra or Maestro have a great deal of parts in common with the car on which it is based, so don't leave £90 alternators just lying about.
The greatest problem with a van fleet workshop is flammable fuel. The problem is worse when the fleet is mixed in with diesel and petrol users in the same workshop for it is too easy to forget which is which. Although diesel is hardly firepr000f, petrol has a way of finding a flame or spark all on its own, and the result is usually catastrophic. A few, rusty, dustcovered extinguishers just will not do as a cure, and could get you closed down by the health and safety boys.
Recent legislation means that it is every individual's own responsibility to ensure safe working conditions, so you cannot hide behind company policy — or lack of it — any more. Your self-employed casual mechanic has every right to refuse to work in unsafe conditions.
Never, ever, drain a tank inside, without specialist advice. The fumes are heavier than air and will creep along the floor until they find the smoking storeman. Ban smoking on the workshop floor at all times anyway.
An empty petrol tank has just the right air/fuel mixture to count as a bomb waiting to go off. Keep sand, or special granules, handy to soak up spills at once, if working in fuel lines. And get proper fire extinguishing equipment in, and train your staff to use it. Any fire station will gladly give free advice.
If you think this is all too dramatic for just a little van workshop, I can only say that it only has to happen to you the once, before you take it seriously.
If you have a lot of vans — say more than 100 — on the fleet, it can pay you to consider doing your own MoT work. Theoretically you have to be open to all comers; in practice this can be easily avoided by sensible siting.
It is not just the test fee that you save, because after all you still have to do the work and get your mechanics trained up. The value of the time wasted in booking and waiting for tests is higher than most users realise. How many vans taken away for MoT test are back within the hour? So you could save 100 hours a year — worth perhaps £2,000. With the test fee that saving gets close to £3,500.
Generate extra income The rules for setting up a bay are fairly stringent in terms of facilities to be provided, and one of the best ways to do it is to buy in a complete package. This would cost from about 27,500 or so, giving a pay back period of just a little over two years. Several suppliers offer such packages, such as FKI Bradbury, Brown Brothers, Gemco, Souriau and Tecalemit. The packages include the brake testers and lifts. You could, of course, generate extra income by opening up the MoT facility to outside customers.
There is also a benefit in being able to use the brake tester and beam aligning equipment at any time, to keep the fleet up to the mark on a regular basis.