Quality saves money
Page 78
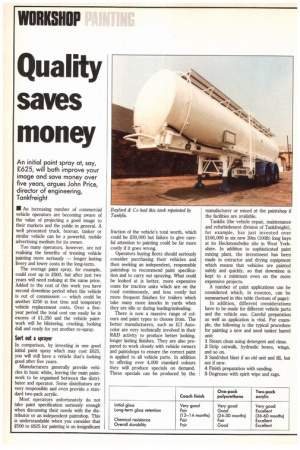
Page 79
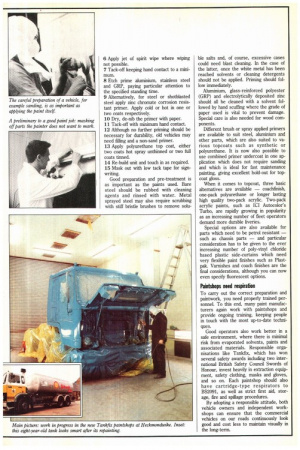
If you've noticed an error in this article please click here to report it so we can fix it.
An initial paint spray at, say, £625, will both improve your image and save money over five years, argues John Price, director of engineering, Tankfreight
• An increasing number of commercial vehicle operators are becoming aware of the value of projecting a good image to their markets and the public in general. A well presented truck, boxvan, tanker or similar vehicle can be a powerful, mobile advertising medium for its owner.
Too many operators, however, are not realising the benefits of treating vehicle painting more seriously — longer lasting livery and lower costs in the long-term.
The average paint spray, for example, could cost up to 2500, but after just two years will need redoing at the same price. Added to the cost of this work you have second downtime period when the vehicle is out of conunission — which could be another 2250 in lost time and temporary vehicle replacement costs. Over a fiveyear period the total cost can easily be in excess of 21,250 and the vehicle paintwork will be blistering, cracking, looking dull and ready for yet another re-spray.
Sort out a sprayer In comparison, by investing in one good initial paint spray which may cost 2625, you will still have a vehicle that's looking good after five years.
Manufacturers generally provide vehicles in basic white, leaving the main paintwork to be organised between the distributor and operator. Some distributors are very responsible and even provide a standard two-pack acrylic.
Most operators unfortunately do not take paint specification seriously enough when discussing their needs with the distributor or an independent paintshop. This is understandable when you consider that 2500 to 2625 for painting is an insignificant fraction of the vehicle's total worth, which could be 230,000 but failure to give careful attention to painting could be far more costly if it goes wrong.
Operators buying fleets should seriously consider purchasing their vehicles and then seeking an independent, responsible paintshop to recommend paint specification and to carry out spraying. What could be looked at is better, more expensive coats for tractive units which are on the road continuously, and less costly but more frequent finishes for trailers which take many more knocks in yards when they are idle or during loading/unloading.
There is now a massive range of colours and paint types to choose from. The better manufacturers, such as ICI Autocolor are very technically involved in their R&D activity to produce better looking, longer lasting finishes. They are also prepared to work closely with vehicle owners and paintshops to ensure the correct paint is applied to all vehicle parts. In addition to offering over 4,000 standard colours they will produce specials on demand. These specials can be produced by the manufacturer or mixed at the paintshop if the facilities are available.
Tankfix (the vehicle repair, maintenance and refurbishment division of Tankfreight), for example, has just invested over 2100,000 in six new 30m (100ft) long bays at its Heckmondwike site in West Yorkshire. In addition to sophisticated paint mixing plant, the investment has been made in extractor and drying equipment which means that vehicles are painted safely and quickly, so that downtime is kept to a minimum even on the more expensive projects.
A number of paint applications can be considered which, in essence, can be summarised in this table (bottom of page): In addition, different considerations have to be made for different vehicle parts and the vehicle use. Careful preparation as well as application is vital. For example, the following is the typical procedure for painting a new and used tanker barrel unit: 1 Steam clean using detergent and rinse.
2 Strip catwalk, hydraulic hoses, wings, and so on.
3 Sand/shot blast if an old unit and fill, but not if new.
4 Finish preparation with sanding.
5 Degrease with spirit wipe and rags.
6 Apply jet of spirit wipe where wiping not possible.
7 Tack-off keeping hand contact to a minimum.
8 Etch prime aluminium, stainless steel and GRP, paying particular attention to the specified standing time.
9 Alternatively, for steel or shotblasted steel apply zinc chromate corrosion resistant primer. Apply cold or hot in one or two coats respectively.
10 Dry, de-nib the primer with paper.
11 Tack-off with minimum hand contact.
12 Although no further priming should be necessary for durability, old vehicles may need filling and a non-sand primer.
13 Apply polyurethane top coat, either two coats hot spray unthinned or two full coats tinned.
14 Re-build unit and touch in as required.
15 Mask out with low tack tape for signwriting.
Good preparation and pre-treatment is as important as the paints used. Bare steel should be rubbed with cleaning agents and rinsed with water. Metal sprayed steel may also require scrubbing with stiff bristle brushes to remove solu
ble salts and, of course, excessive cases could need blast cleaning. In the case of the latter, once the white metal has been reached solvents or cleaning detergents should not be applied. Priming should follow immediately.
Aluminium, glass-reinforced polyester (GRP) and electrolytically deposited zinc should all be deaned with a solvent followed by hand scuffing where the grade of paper used is vital to prevent damage. Special care is also needed for wood components.
Different brush or spray applied primers are available to suit steel, aluminium and other parts, which are also suited to various topcoats such as synthetic or polyurethane. It is now also possible to use combined primer undercoat in one application which does not require sanding and which is ideal for fast maintenance painting, giving excellent hold-out for topcoat gloss.
When it comes to topcoat, three basic alternatives are available — coachfinish, one-pack polyurethane or longer lasting high quality two-pack acrylic. Two-pack acrylic paints, such as ICI Autocolor's Turbo, are rapidly growing in popularity as an increasing number of fleet operators demand more durable liveries.
Special options are also available for parts which need to be petrol resistant — such as chassis parts — and particular consideration has to be given to the ever increasing number of poly-vinyl chloride based plastic side-curtains which need very flexible paint finishes such as Plastpak. Varnishes and coach finishes are the final considerations, although you can now even specify fluorescent options.
Paintsheps need respiration To carry out the correct preparation and paintwork, you need properly trained personnel. To this end, many paint manufacturers again work with paintshops and provide ongoing training, keeping people in touch with the most up-to-date techniques.
Good operators also work better in a safe environment, where there is minimal risk from evaporated solvents, paints and associated materials. Responsible organisations like Tankfix, which has won several safety awards including two international British Safety Council Swords of Honour, invest heavily in extraction equipment, safety clothing, masks and gloves, and so on. Each paintshop should also have cartridge-type respirators to BS2091, as well as strict first aid, storage, fire and spillage procedures.
By adopting a responsible attitude, both vehicle owners and independent workshops can ensure that the commercial vehicles on our roads continuously look good and cost less to maintain visually in the long-term.