Reliable but check
Page 75
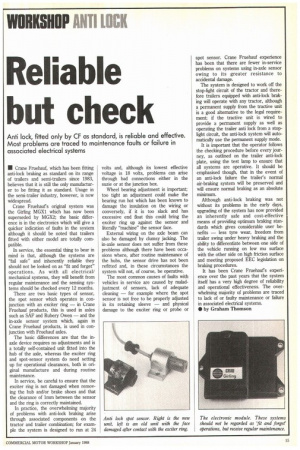
If you've noticed an error in this article please click here to report it so we can fix it.
Anti lock, fitted only by CF as standard, is reliable and effective. Most problems are traced to maintenance faults or failure in associated electrical systems
• Crane Fruehauf, which has been fitting anti-lock braking as standard on its range of trailers and semi-trailers since 1983, believes that it is still the only manufacturer to be fitting it as standard. Usage in the semi-trailer industry, however, is now widespread.
Crane Fruehauf s original system was the Girling MGX1 which has now been superseded by MGX2; the basic differ ence is in the electronics which will give a quicker indication of faults in the system although it should be noted that trailers fitted with either model are totally compatible.
In service, the essential thing to bear in mind is that, although the systems are "fail safe" and inherently reliable they should not be looked on as "fit and forget" operations. As with all electrical/ mechanical systems, they will benefit from regular maintenance and the sensing systems should be checked every 12 months.
There are two basic types of sensor, the spot sensor which operates in con junction with an exciter ring — in Crane Fruehauf products, this is used in axles such as SAF and Rubery Owen — and the in-axle sensor system which, again in Crane Fruehauf products, is used in conjunction with Fruehauf axles.
The basic differences are that the inaxle device requires no adjustments and is a totally self-contained unit fitted into the hub of the axle, whereas the exciter ring and spot-sensor system do need setting up for operational clearances, both in original manufacture and during routine maintenance.
In service, be careful to ensure that the exciter ring is not damaged when remov ing the hub and/or brake shoes and that the clearance of lmm between the sensor and the ring is correctly maintained.
In practice, the overwhelming majority of problems with anti-lock braking arise through associated components on the tractor and trailer combination; for example the system is designed to run at 24 volts and, although its lowest effective voltage is 18 volts, problems can arise through bad connections either in the suzie or at the junction box.
Wheel bearing adjustment is important; too tight an adjustment could make the bearing run hot which has been known to damage the insulation on the wiring or conversely, if it is too slack and has excessive end float this could bring the exciter ring up against the sensor and literally "machine" the sensor face.
External wiring on the axle beam can also be damaged by clumsy jacking. The in-axle sensor does not suffer from these problems although there have been occasions where, after routine maintenance of the hubs, the sensor drive has not been refitted and, in these circumstances the system will not, of course, be operative.
The most common causes of faults with vehicles in service are caused by maladjustment of sensors, lack of adequate cleaning — for example where the spot sensor is not free to be properly adjusted in its retaining sleeve — and physical damage to the exciter ring or probe or spot sensor. Crane Fruehauf experience has been that there are fewer in-service problems on systems using in-axle sensor owing to its greater resistance to accidental damage.
The system is designed to work off the stop-light circuit of the tractor and therefore trailers equipped with anti-lock braking will operate with any tractor, although a permanent supply from the tractive unit is a good alternative to the legal requirement; if the tractive unit is wired to provide a permanent supply as well as operating the trailer anti lock from a stoplight circuit, the anti-lock system will automatically use the permanent supply mode.
It is important that the operator follows the checking procedure before every journey, as outlined on the trailer anti-lock plate, using the test lamp to ensure that all systems are operative. It should be emphasised though, that in the event of an anti-lock failure the trailer's normal air-braking system will be preserved and will ensure normal braking as an absolute minimum.
Although anti-lock braking was not without its problems in the early days, upgrading of the system has now provided an inherently safe and cost-effective means of providing optimum braking standards which gives considerable user benefits — less tyre wear, freedom from trailer swing under heavy braking and the ability to differentiate between one side of the vehicle running on low mu surface with the other side on high friction surface and meeting proposed EEC legislation on braking procedures.
It has been Crane Fruehauf s experience over the past years that the system itself has a very high degree of reliability and operational effectiveness. The overwhelming majority of problems are traced to lack of or faulty maintenance or failure in associated electrical systems.
• by Graham Thomson