GROUND CRUISE
Page 35
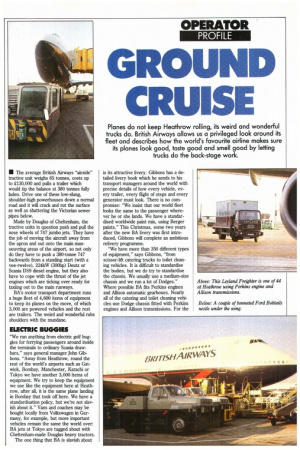
Page 36

Page 37
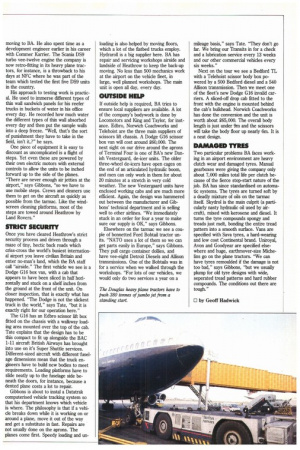
If you've noticed an error in this article please click here to report it so we can fix it.
Planes do not keep Heathrow rolling, its weird and wonderful trucks do. British Airways allows us a privileged look around its fleet and describes how the world's favourite airline makes sure its planes look good, taste good and smell good by letting trucks do the back-stage work.
• The average British Airways "aside" tractive unit weighs 65 tonnes, costs up to £130,000 and pulls a trailer which would tip the balance at 380 tonnes fully laden. Drive one of these low-slung, shoulder-high powerhouses down a normal road and it will crack and rut the surface as well as shattering the Victorian sewer pipes below.
Made by Douglas of Cheltenham, the tractive units in question push and pull the nose wheels of 747 jumbo jets. They have the job of moving the aircraft away from the apron and out onto the main manoeuvring areas of the airport, so not only do they have to push a 380-tonne 747 backwards from a standing start (with a vee-twelve), 224kW (300hp) Deutz or Scania DS9 diesel engine, but they also have to cope with the thrust of the jet engines which are ticking over ready for taxiing out to the main runways.
BA's motor transport department runs a huge fleet of 4,600 items of equipment to keep its planes on the move, of which 3,000 are powered vehicles and the rest are trailers. The weird and wonderful rubs shoulders with the mundane.
ELECTRIC BUGGIES
"We rim anything from electric golf buggies for ferrying passengers around inside the terminals to ordinary Scania drawbars," says general manager John Gibbons. "Away from Heathrow, round the rest of the world's airports such as Gatwick, Bombay, Manchester, Karachi or Tokyo we have another 3,000 items of equipment. We try to keep the equipment we use like the equipment here at Heathrow, after all, it is the same plane landing in Bombay that took off here. We have a standardisation policy, but we're not slavish about it." Vans and coaches may be bought locally from Volkswagen in Germany, for example, but more important vehicles remain the same the world over: BA jets at Tokyo are tugged about with Cheltenham-made Douglas heavy tractors.
The one thing that BA is slavish about is its attractive livery. Gibbons has a detailed livery book which he sends to his transport managers around the world with precise details of how every vehicle, every trailer, every flight of steps and every generator must look. There is no compromise: "We insist that our world fleet looks the same to the passenger wherever he or she lands. We have a standardised worldwide paint mix, using Berger paints." This Christmas, some two years after the new BA livery was first introduced, Gibbons will complete an ambitious relivery programme.
"We have more than 350 different types of equipment," says Gibbons, "from scissor-lift catering trucks to toilet cleaning vehicles. It is difficult to standardise the bodies, but we do try to standardise the chassis. We usually use a medium-size chassis and we run a lot of Dodges." Where possible BA fits Perkins engines and Allison automatic gearboxes. Nearly all of the catering and toilet cleaning vehicles use Dodge chassis fitted with Perkins engines and Allison transmissions. For the company's large road-going fleet, Gibbons has decided to standardise on Scania: "Our cargo vehicles are now mainly Scania 112 drawbars and artics. More and more of our heavy buses are Scania too," he says. BA also has several Leyland Freighters, fitted with Perkins engines and Allison boxes. The company has found them reliable and rugged.
When the vee-twelve Deutz aircooled engines wear out on the Douglas plane tractors, Gibbons is replacing them with DS9 Scania turbo engines. Again, he wants spare parts commonality througout the fleet: "We try to buy British, but where there are products which are clearly better made abroad we will go abroad." The scissor-lift platforms which are used to raise containers into the freight holds of big 747 jumbos, for instance, are made by Lantis in America. They cost about .280,000 each.
LAND ROVERS
Most of the vans and mini-buses which zoom around Heathrow are based on Ford Transits: the Sherpas which BA used to run have disappeared. Gibbons finds that different airports wear out their vehicles in different ways and at different rates. "We use Land Rovers all over the world," he says, "including the Falkland Islands and the Ascension Islands. At one time, our Land Rovers were only lasting 12 months in the Falldands. It was the mud and the ruts and the terrible roads." Now that the new Falkland Islands airport has been built the rate of vehicle wear has improved considerably. Heathrow's coach fleet is dominated by the Leyland National — "a revolutionary design in its time", says vehicle and equipment engineering manager Bernie Tate. Gatwick has nearly all of the Leyland articulated buses in the BA fleet. The company found that the articulated turning platform in the centre made the buses unsuitable for a lot of high-volume passenger work. Two of the articulated buses have now been fitted out as mobile exhibition vehicles and they travel around Britain showing the company's 40,000 staff new developments or special promotions.
BA runs more than 200 Lansing electric tugs for pulling baggage trains around the airport, especially around Terminal Four. "We worked closely with Lansing to make sure we got exactly what we wanted," says Gibbons. Lansing sent an engineer down to British Airways to work with Gibbons' technical engineers and once the correct design had been hammered out, Lansing put the unit into production. It is now a best seller with airlines all round the world, and not just BA, says Gibbons.
On average 29 different vehicles service a large modern passenger jet, clustering like ants around the entrance to their nest. There are air-conditioners mounted on trucks, refuelling tankers, toilet emptiers, baggage tugs, catering scissorlift box vans, powered conveyors, heavy Douglas tractor units, cleaning vehicles to rise up and wash things like windscreens, freight container elevators, and so on.
"Passengers nowadays walk off a plane and expect a quick turn-round," says Gibbons. "Three-and-a-half hours is the mini mum long haul turn-round time, and in that time we have to clean the plane, disinfect it, take the food on and off, remove the litter and re-fuel it. It can get really hairy out there." There are frequent bumps and nudges, and virtually every vehicle you see on the aprons at Heathrow bears the scars of the scrum with scrapes down the side, a dent in the panels, a smashed corner or two. It is a constant Forth Bridge battle for Gibbons' workshops to keep things looking neat and tidy. Part of the problem is the immense pressure the ground support crews work under, and the other part is that drivers are not allocated their own vehicles. They are expected to jump into whatever is required, when required. Every airline's vehicles are dented.
"Our drivers don't hang about out there," says Tate. "They haven't got the time." For BA, after all, a vehicle is a means to an end and not an end in itself. "We make it a condition of being a British Airways driver that he or she has to have a full HGV 1 and a full PSV licence," says Gibbons. "In the course of a day they could drive a truck, a coach full of passengers or crew and a Vauxhall Carlton estate car."
BROAD BRUSH
Gibbons attitude to the job is to be as flexible as possible, wherever possible. He works with a broad brush, out of necessity. He is not a career-long British Airways man, like Tate. Gibbons worked for the National Freight Consortium member-company BRS Western before moving to BA. He also spent time as a development engineer earlier in his career with Commer Karrier. The Scania DS9 turbo vee-twelve engine the company is now retro-fitting in its heavy plane tractors, for instance, is a throwback to his days at NFC where he was part of the team which tested the first five DS9 units in the country.
His approach to testing work is practical. He used to immerse different types of thin wall sandwich panels for his reefer trucks in buckets of water in his office every day. He recorded how much water the different types of thin wall absorbed every day and then put the sample walls into a deep freeze. "Well, that's the sort of punishment they have to take in the field, isn't it,?" he says.
One piece of equipment it is easy to discount as uncomplicated is a flight of steps. Yet even these are powered by their own electric motors with external controls to allow the units to be inched forward up to the side of the planes. "There are never enough air jetties at the airport," says Gibbons, "so we have to use mobile steps. Crews and cleaners use them to get on the aircraft as quickly as possible from the tarmac. Like the windscreen cleaning platforms, most of the steps are towed around Heathrow by Land Rovers."
STRICT SECURITY
Once you have cleared Heathrow's strict security process and driven through a maze of tiny, hectic back roads which criss-cross the world's busiest international airport you leave civilian Britain and enter no-man's land, which the BA staff call "airside." The first vehicle we see is a Dodge G16 box van, with a cab that appears to have been sliced in half horizontally and stuck on a shelf inches from the ground at the front of the unit. On closer inspection, that is exactly what has happened. "The Dodge is not the slickest truck in the world," says Tate, "but it is exactly right for our operation here."
The G16 has an Edbro scissor lift box fitted on the chassis with a walkway loading area mounted over the top of the cab. Tate explains that the design has to be this compact to fit up alongside the BAC 1-11 aircraft British Airways has brought into use on it's Super Shuttle services. Different-sized aircraft with different fuselage dimensions mean that the truck engineers have to build new bodies to meet requirements. Loading platforms have to slide neatly up to the fuselage side beneath the doors, for instance, because a dented plane costs a lot to repair.
Gibbons is about to instal a Datatrak computerised vehicle tracking system so that his department knows which vehicle is where. The philosophy is that if a vehicle breaks down while it is working on or around a plane, move it out of the way and get a substitute in fast. Repairs are not usually done on the aprons. The planes come first. Speedy loading and un
loading is also helped by moving floors, which a lot of the flatbed trucks employ. Hydraroll is a big supplier here. BA has repair and servicing workshops airside and landside of Heathrow to keep the back-up moving. No less than 500 mechanics work at the airport on the vehicle fleet, in large, well planned workshops. The main unit is open all day, every day.
OUTSIDE HELP
If outside help is required, BA tries to ensure local suppliers are available. A lot of the company's bodywork is done by Locomotors and King and Taylor, for instance. Edbro, Norwich Coachworks and Telehoist are the three main suppliers of scissors lift chassis. A Dodge G16 scissor box van will cost around £60,000. The next sight on our drive around the aprons of Terminal Four is one of BA's new Danish Vestergaard, de-icer units. The older three-wheel de-icers have open cages on the end of an articulated hydraulic boom, and men can only work in them for about 20 minutes at a stretch in very cold weather. The new Vestergaard units have enclosed working cabs and are much more efficient. Again, the design was hammered out between the manufacturer and Gibbons' technical department and is selling well to other airlines. "We immediately stuck in an order for four a year to make sure our supply is OK," says Gibbons.
Elsewhere on the tarmac we see a couple of bonnetted Ford Bobtail tractor units. "NATO uses a lot of them so we can get parts easily in Europe," says Gibbons. They pull cargo container dollies, and have vee-eight Detroit Diesels and Allison transmissions. One of the Bobtails was in for a service when we walked through the workshops. "For lots of our vehicles, we would only do two services a year on a mileage basis," says Tate. "They don't go far. We bring our Transits in for a check and a lubrication service every 13 weeks and our other commercial vehicles every six weeks."
Next on the tour we see a Bedford TL with a Telehoist scissor body box powered by a 500 Bedford diesel and a 540 Allison transmission. Then we meet one of the fleet's new Dodge G16 invalid carriers. A sliced-off drop cab fitted to the front with the engine is mounted behind the cab's bulkhead. Norwich Coachworks has done the conversion and the unit is worth about £65,000. The overall body length is just under 9m and the scissors will take the body floor up nearly 6m. It is a neat design.
DAMAGED TYRES
Two particular problems BA faces working in an airport environment are heavy clutch wear and damaged tyres. Manual gearboxes were giving the company only about 7,000 miles total life per clutch because of the fierce stop-start nature of the job. BA has since standardised on automatic systems. The tyres are turned soft by a deadly mixture of oils on the tarmac itself. Skydrol is the main culprit (a particularly nasty hydraulic oil used by aircraft), mixed with kerosene and diesel. It turns the tyre compounds spongy and treads just melt, bonding the entire tread pattern into a smooth surface. Vans are specified with Sava tyres, a hard-wearing and low cost Continental brand. Uniroyal, Avon and Goodyear are specified elsewhere and huge, earthmover-size Michelins go on the plane tractors. "We can have tyres remoulded if the damage is not too bad," says Gibbons, "but we usually plump for old tyre designs with wide, seperated tread patterns and hard rubber compounds. The conditions out there are tough."
0 by Geoff Hadwick