Safety measures: (6) Interference fits
Page 28
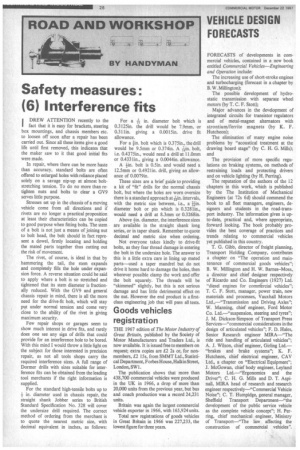
If you've noticed an error in this article please click here to report it so we can fix it.
I DREW ATTENTION recently to the I fact that it is easy for brackets, steering box mountings, and chassis members etc. to loosen off soon after a repair has been carried out. Since all these items give a good life until first removed, this indicates that the maker saw to it that good initial fits were made.
In repair, where there can be more haste than accuracy, standard bolts are often offered to enlarged holes with reliance placed solely on a savage nip-up at almost boltstretching tension. To do no more than retighten nuts and bolts to clear a 0V9 serves little purpose.
Stresses set up in the chassis of a moving vehicle come from all directions and if rivets are no longer a practical proposition at least their characteristics can be copied to good purpose when fitting bolts. The stem of a bolt is not just a means of joining nut to bolt head, the bolt should in fact represent a dowel, firmly locating and holding the mated parts together thus cutting out the risk of movement.
The rivet, of course, is ideal in that by hammering the tail, the stem expands and completely fills the hole under expansion force. A reverse situation could be said to apply where a bolt is so stretched and tightened that its stem diameter is fractionally reduced. With the GV9 and general chassis repair in mind, there is all the more need for the drive-fit bolt, which will stay put under normal tension and come very close to the ability of the rivet in giving maximum security.
Few repair shops or garages seem to show much interest in drive fits, and rarely does one see any sign of drills that could provide for an interference hole to be bored. With this mind I would throw a little light on the subject for those interested in precision repair, as not all tools shops carry the required interference sizes. A full range of Dormer drills with sizes suitable for interference fits can be obtained from the leading tool merchants if the right information is supplied.
For the standard high-tensile bolts up to + in. diameter used in chassis repair, the straight shank Jobber series to British Standard Specification No. 328 will cover the undersize drill required. The correct method of ordering from the merchant is to quote the nearest metric size, with decimal equivalent in inches, as follows: For a in. diameter bolt which is 0.3125in. the drill would be 7.9mm, or 0.311in. giving a 0.0015in. drive fit allowance.
For a tin. bolt which is 0.375in., the drill would be 9.5mm or 0.374in. A %in. bolt, i.e. 0.4375in., would need a drill at 11.0mm or 0.4331in., giving a 0.0044in. allowance.
A 4-in. bolt is 0.5 in. and would need a 12.5mm or 0.4921in. drill, giving an allowance of 0.0079in.
These sizes are a brief guide to providing a kit of "fit" drills for the normal chassis bolt, but where the holes are worn oversize there is a standard approach at bin. intervals, with the metric size between, i.e., a gin. diameter bolt or pin which is 0.3281in., would need a drill at 8.3mm or 0.3268in.
Above +in. diameter, the interference sizes are available in the straight shank long series, or in taper shank. Remember to quote decimal and metric size when ordering.
Not everyone takes kindly to drive-fit bolts, as they fear thread damage in entering the bolt in the undersize hole. The answer to this is a little extra care in lining up mated parts—used a taper mandrel but do not drive it home hard to damage the holes, then wherever possible clamp the work and offer the bolt squarely. The threads will be "skimmed" slightly, but this is not serious damage and has little detrimental effect on the nut. However the end product is a firstclass engineering job that will pass all tests.