ENCOURAGING USE OF PNEUMATIC TYRES.
Page 20
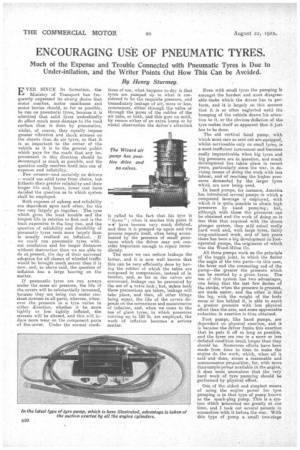
Page 21
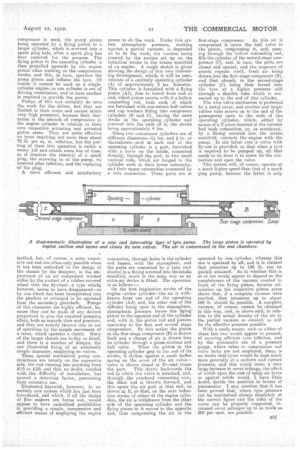
If you've noticed an error in this article please click here to report it so we can fix it.
Much of the Expense and Trouble Connected with Pneumatic Tyres is Due to Under-inflation, and the Writer Points Out How This Can be Avoided.
By Henry Sturmey.
EVER SINCE its formation, the 1;4 Ministry of Transport has frequently expressed its strong desire that motor coaches, motor omnibuses and motor lorries should, so far as possible, be run on pneumatic tyres, because it is admitted that solid tyres undoubtedly do effect much more damage to the road surface than is done by pneumatics, whilst, of course, they equally impose greater vibration and shock stresses on the chassis than do air tyres, so that it is as important to the owner of the vehicle as it is to the general public which pays for the roads that any improvement in this direction should be encouraged as much as possible, and the question really resolves itself into one of expense and reliability.
Few owners—and certainly no drivers ----would use solid tyres from choice, but hitherto their greater reliability and their longer life and, hence, lower cost have decided the question as to which system shall be employed.
Both expense of upkeep and reliability are dependent upon each other, for the two very largely go together. The tyre which gives the least trouble and the longest life in relation to first cost is the least expensive in the long run, and the question of reliability and durability of pneumatic tyres rests more largely than is usually realized on inflation. • If we could run pneumatic tyres without reinflation and for longer distances without destruction than we are able to do at present, the day of their universal adoption for all classes of wheeled traffic would be brought much nearer than it is now, and, as above said, the question of inflation has a large bearing on the matter.
If pneumatictyres are run always under the same air pressure, the life of the covers will be substantially increased, because they are being run under constant stresses in all parts, whereas, whenever the pressure in a tyre varies in either direction, whether it be more tightly or less tightly inflated, the stresses will be altered, and this will induce more wear on the component parts of the.cover. Under the normal condi tions of use, what happens to-day is that tyres are pumped up to what is considered to be the requisite pressure, and immediately leakage of air, more or less, commences, either through the valve or through the pores of the rubber of the air tube, or both, and this goes on until, by reason either of an extra bump or by visual observation the driver's attention is called to the fact that his tyre is " down" ; when it reaches this point it wa have become very much deflated, and then it is pumped up again and the process repeats itself, often being accentuated by the presence of small punctures which the driver may not consider important enough to repair immediately.
The more we can reduce leakage the better, and it is now well known that this can be very efficiently done by having the rubber of which the tubes are composed in compression, instead of in tension and, so far as the valves are concerned, leakage can be prevented by the use of a valve lock ; but, unless both these precautions are taken, leakage will take place, and then, all other things being equal, the life of the covers depends on the correctness and maintenance of inflation, anti, when we come to the use of giant tyres, in which pressures running up to 120 lb. are employed, the work of inflation becomes a serious matter. Even with small tyres the pumping is amongst the hardest and most disagreeable •tasks which the driver has to perform, and it is largely on this account that it is so often neglected until the bumping of the vehicle draws his attention to it, or the obvious deflation of the tyre makes itself so apparent that it just has to be done.
The old vertical hand pump, with which most cars as sent out are equipped, whilst serviceable only on small tyres, is a most inefficient instrument and becomes really impracticable when big tyres and big pressures are in question, and muchdevelopment has taken place in recent years, particularly since the war, in devising means of doing the work with less labour, and of reaching the higher pressures demanded -by the larger tyres which are now being used.
In hand pumps, for instance, America has introduced several pumps in which a compound leverage is employed, with which it is quite possible to attain high pressures by hand pumping ; but, although with these the pressures can be obtained and the work of dairy= so is less than that required with the direct plunger system, they still entail really hard work and, with large tyres, fairly long-continued work, and of late years there has been a big development in footoperated pumps, the originator of which was the Wood-Milne Co.
All these pumps work an the principle of the toggle joint, in which the flatter the angle of the two parts—in this case, the lever and the connecting rod of the pump—the greater the pressure which can be exerted by a given force. The use of this system has two advantages, one being that the last few inches of the stroke, when the pressure is greatest, are made easier, and the other is that the leg, with the weight of the body more or less behind it, is able to exert a greater pressure with -less physical effort than the arm, and some appreciable reduction in exertion is thris obtained.
Foot pumps, like hand pumps, are dependent on physical exertion, and it is because the driver funks this exertion that he puts it off so long as possible, and the tyres are run in a more or less deflated condition much longer than they should be. Numerous efforts have been made from time to time to make the engine do the work, which, when all is said and done, seems a reasonable and commonsense proposition, for, with more tharnample power available in the engine, it does seem anomalous that the very hard work of tyre pumping should be performed by physical effort.
One of the oldest and simplest means. of using the engine power for tyre pumping is in that type of pump known as the spark-plug pump. This is a system Which jetereeted me greatly at one time, and I took out several patents in connection with it before the war. With this type of pump a small two-stage
compressor is used, the pump piston being operated by a flying piston in a larger cylinder, which is screwed into a spark plug hole, after a spark plug has been removed for the purpose. The flying piston in the operating cylinder is then propelled upwards by the engine piston when working on the compression stroke, and this, in turn, operates the pump piston and 'inflates the tyre. Of course it cannot be used on a singlecylinder engine, as one cylinder is out of driving commission, and at least another is required to provide the power. Pumps of this sort certainly do save the work for the driver, but they are limited in their scope and cannot attain very high pressures, because their limitation is the amount of compression in the engine cylinder in relation to their own respective actuating and actuated piston areas. They are quite effective on tyres requiring not more than about 70 1h. per sq. in, inflation, but, the putting of them into operation is rather a messy job and entails some loss of time, as it requires the removal of a spark plug,. the screwing in of the pump, its removal after inflation, and the replacing of the plug.
A more efficient and (satisfactory
• method, but, of course, a more expensive one and one often only possible when it has been embodied in the design of the chassis by the designer, is the employment of an air compressor worked either by the cantact a a rubber-covered wheel with the flywheel—a type which; however, seems to have disappeared—or. by one Which has been incorporated into the gearbox or arranged to be operated from the secondary gearshaft. Pumps of this character are highly efficient, because they can be made of any desired proportion to give the required pumping effect, both as regards time and pressure, and they are usually thrown into or out of operation by the simple movement of a lever, which operates a clutch. Many of the larger chassis are to-day so fitted, and there iS a number of designs, the one, illustrated being of an extremely simple character, employing no valves. Those special mechanical pump constructions are usually on the expensive aide, the cost relining into anything from £15 to £20, and this, no doubt, coupled with the difficulty of installation, has proved a deterrent factor, preventing their extensive use.
Ilhistrated herewith, however, is an entirely new system which has just been introduced, and which, if all the claims' of [the makers are borne out, would appear to have undoubted possibilities in providing a simple, inexpensive and efficient means of employing the engine
power to do the work. Under this system atmospheric pressure, working against a partial vacuum, is depended on to do the work, the vacdum being created by the suction set up on the induction stroke in the intake manifold Of en engine. A rough sketch is given showing the design of this very interestifig development, which, it will be seen, -consists of a centrally operating Cylinder (A) of approximately 3 ins, diameter. This cylinder is furnished with a flying piston (Al), free to travel from end to end, which piston carries with it a hollow connecting rod, both ends of which are furnished with non-return hall valves and cup washers fitting into compressor 'cylinders (B and C), having the same stroke as the operating cylinder and screwed into the ends of it, the stroke being approximately 4 ins.
These two compressor cylinders are of different diamefers-14 ins, and i• in, or thereabouts—and (tit each end of the operating cylinder is a port, furnished with a cover on the connected directly, through the port, to two small vertical .rods, which are hinged to the cylinder ends at their lower extremity, and their upper extremities connected by a wire connection. These ports are in connection, through holes in the cylinder end bosses, with the atmosphere, and the ports are connected by a tube (not shown) to a fitting screwed into theintake manifold, much in the same -way as an extra-air device is fitted. The operation is as follows:— . •
On the first inspiration stroke of the engine—either cylinder—the air is withdrawn from one end of the operating cylinder (AA) and, the other end of the cylinder being open to the atmosphere, atmospheric pressure forces the flying piston to the opposite end of the cylinder and, with it, the piston rod and pistons• operating in the first and second stage compressors. By this action the piston in the first-stage compressor (B) is drawn back and a charge of air is drawn into its cylinder through a gauze strainer and ball valve. When the piston in the operating cylinder gets to the end of its stroke, it strikes against a small buffer spring on the cover of the air valve— valve is shown closed at D—and closes the port. This draws backwards the rod tp which the valve ia attached, and, throngh the overhead connecting wire, the other rod is thrown forward, and this opens the air poi-t at that end, as shown a E, o that, on the next induction stroke of either of the engine cylin-• clers, the air is withdrawn from the other side of the operating cylinder and the flying piston in it moves to the opposite end, thus compressing the air in the
first-stage compressor. As this air is compressed it opens the ball valve in the piston, Compressing it, and, passing through the hollow connecting rod, fills the cylinder of the second-stage compressor (C), and, in turn, the ports are closed and Opened, and the sequence of events repeats itself, fresh air being drawn into the first-stage compressor (B), and that already in the second-stage cylinder (Ct being then forced into the tyre at a higher pressure still through a flexible tube which is connected up to the end of this cylinder.
The wire valve mechanism is protected by a metal cover, and another and larger rubber tube screws on to the end of the. passageway open to the ends of the operating cylinder, which, either by means of a T-plece inserted in the vacuum fuel tank connection, or, as mentioned, by a. fitting screwed into the intake manifold, connects the engine with the pump. In the latter case a .valve with fly-nut is provided, so that when a tyre is required to be pumped up, all that needs to be done is to screw on -the connection and open the valve.
This system will, of course, operate at a much higher speed than that of a spark. plug pump, because the latter is only
operated by one cylinder, whereas this one is operated by all, and it is claimed that pressures lip to 120 lb. can be quickly attained. As to whether this is Co or not would appear to depend on thecompleteness of the vacuum created in front of the flying piston, because calculation on the respective piston areas shows that, if a complete vacuum were reached, then pressures up to about 160 lb. should be possible. A complete vacuum, of course, cannot be obtained in this way, and, as above said; in relation to the actual densityof the air in the partial vacuum so created, so will be the effective pressure possible.
With a ready means such as either of these last two would appear to present, of securing efficient tyre inflation, and by the systematic use of a pressure gauge, where tubes in compression and valve locks are not employed, there is no doubt that tyres would be kept much more generally at a uniform and correct pressure, and this would mean a very large increase in cover Mileage, the effect of which upon the cost of using air tyres as against solids would, I have little doubt, decide the question in favour of pneumatics. I may mention that it has been proved that, where tyre pressure can be maintained always absolutely at the correct figure and the sides of the cover can be properly supported, increased cover mileages up to as much as 200 per cent. are possible.