THE BIGGER THEY ARE THE SMOOTHER THEY GO
Page 128
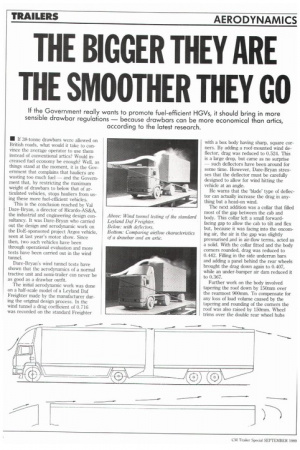
Page 132
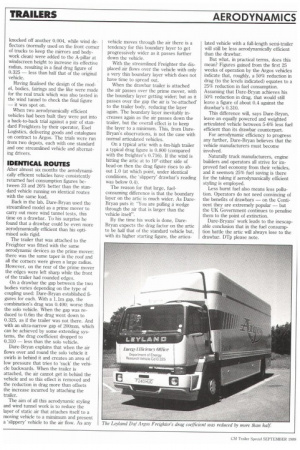
If you've noticed an error in this article please click here to report it so we can fix it.
If the Government really wants to promote fuel-efficient HGVs, it should bring in more sensible drawbar regulations — because drawbars can be more economical than artics, according to the latest research.
IN If 38-tonne drawbars were allowed on British roads, what would it take to convince the average operator to use them instead of conventional artics? Would increased fuel economy be enough? Well, as things stand at the moment, it is the Government that complains that hauliers are wasting too much fuel — and the Government that, by restricting the maximum weight of drawbars to below that of articulated vehicles, stops hauliers from using these more fuel-efficient vehicles.
This is the conclusion reached by Val Dare-Bryan, a director of Ricardo-AS&A, the industrial and engineering design consultancy. It was Dare-Bryan who carried out the design and aerodynamic work on the DoE-sponsored project Argos vehicle, seen at last year's motor show. Since then, two such vehicles have been through operational evaluation and more tests have been carried out in the wind tunnel.
Dare-Bryan's wind tunnel tests have shown that the aerodynamics of a normal tractive unit and semi-trailer can never be as good as a drawbar outfit.
The initial aerodynamic work was done on a half-scale model of a Leyland Daf Freighter made by the manufacturer during the original design process. In the wind tunnel a drag coefficient of 0.716 was recorded on the standard Freighter
with a box body having sharp, square corners. By adding a roof-mounted wind deflector, drag was reduced to 0.524. This is a large drop, but came as no surprise — such deflectors have been around for some time. However, Dare-Bryan stresses that the deflector must be carefully designed to allow for wind hitting the vehicle at an angle.
He warns that the 'blade' type of deflector can actually increase the drag in anything but a head-on wind.
The next addition was a collar that filled most of the gap between the cab and body. This collar left a small forwardfacing gap to allow the cab to tilt and flex but, because it was facing into the oncoming air, the air in the gap was slightly pressurised and in air-flow terms, acted as a solid. With the collar fitted and the body corners rounded, drag was reduced to 0.442. Filling in the side underrun bars and adding a panel behind the rear wheels brought the drag down again to 0.407, while an under-bumper air dam reduced it to 0.367.
Further work on the body involved tapering the roof down by 150mm over the rearmost 900mm. To compensate for any loss of load volume caused by the tapering and rounding of the corners the roof was also raised by 150mm. Wheel trims over the double rear wheel hubs knocked off another 0.004, while wind deflectors (normally used on the front corner of trucks to keep the mirrors and bodywork clean) were added to the A-pillar at windscreen height to increase its effective radius, resulting in a final drag figure of 0.325 — less than half that of the original vehicle.
Having finalised the design of the model, bodies, fairings and the like were made for the real truck which was also tested in the wind tunnel to check the final figure — it was spot on.
When two aerodynamically efficient vehicles had been built they were put into a back-to-back trial against a pair of standard Freighters by their operator, Exel Logistics, delivering goods and catalogues on contract to Argos. The trials were run from two depots, each with one standard and one streamlined vehicle and alternating drivers.
IDENTICAL ROUTES
After almost six months the aerodynamically efficient vehicles have consistently returned fuel consumption figures between 23 and 26% better than the standard vehicle running on identical routes with the same load.
Back in the lab, Dare-Bryan used the streamlined model as a prime mover to carry out more wind tunnel tests, this time on a drawbar. To his surprise he found that a drawbar could be even more aerodynamically efficient than his optimised solo rigid.
The trailer that was attached to the Freighter was fitted with the same aerodynamic devices as the prime mover; there was the same taper in the roof and all the corners were given a large radius. However, on the rear of the prime mover the edges were left sharp while the front of the trailer had rounded edges.
On a drawbar the gap between the two bodies varies depending on the type of coupling used: Dare-Bryan established figures for each. With a 1.1m gap, the combination's drag was 0.400; worse than the solo vehicle. When the gap was reduced to 0.6m the drag went down to 0.325, as if the trailer was not there. And with an ultra-narrow gap of 200mm, which can be achieved by some extending systems, the drag coefficient dropped to 0.310 — less than the solo vehicle.
Dare-Bryan explains that when the air flows over and round the solo Vehicle it swirls in behind it and creates an area of low pressure that tries to 'suck' the vehicle backwards. When the trailer is attached, the air cannot get in behind the vehicle and so this effect is removed and the reduction in drag more than offsets the increase incurred by attaching the trailer.
The aim of all this aerodynamic styling and wind tunnel work is to reduce the layer of static air that attaches itself to a moving vehicle to a mimimum and present a 'slippery' vehicle to the air flow. As any vehicle moves through the air there is a tendency for this boundary layer to get progressively wider as it passes further down the vehicle.
With the streamlined Freighter the displaced air flows over the vehicle with only a very thin boundary layer which does not have time to spread out.
When the drawbar trailer is attached the air passes over the prime mover, with the boundary layer getting wider; but as it passes over the gap the air is 're-attached' to the trailer body, reducing the layer again. The boundary layer inevitably increases again as the air passes down the trailer, but the overall effect is to keep the layer to a minimum. This, from DareBryan's observations, is not the case with normal articulated vehicles.
On a typical artic with a 4m-high trailer a typical drag figure is 0.800 (compared with the freighter's 0.716). If the wind is hitting the artic at to 10° either side of head-on then the drag figure rises to about 1.0 (at which point, under identical conditions, the 'slippery' drawbar's reading was below 0.4).
The reason for that large, fuelconsuming difference is that the boundary layer on the artic is much wider. As DareBryan puts it: "You are pulling a wedge through the air that is larger than the vehicle itself'.
By the time his work is done, DareBryan expects the drag factor on the artic to be half that of the standard vehicle but, with its higher starting figure, the articu
lated vehicle with a full-length semi-trailer will still be less aerodynamically efficient than the drawbar.
But what, in practical terms, does this mean? Figures gained from the first 25 weeks of operation by the Argos vehicles indicate that, roughly, a 50% reduction in drag (to the levels indicated) equates to a 25% reduction in fuel consumption. Assuming that Dare-Bryan achieves his 50% reduction in drag, that would still leave a figure of about 0.4 against the drawbar's 0.310.
This difference will, says Dare-Bryan, leave an equally powered and weighted articulated vehicle between 5-6% less fuel efficient than its drawbar counterpart.
For aerodynamic efficiency to progress any further, Dare-Bryan believes that the vehicle manufacturers must become involved.
Naturally truck manufacturers, engine builders and operators all strive for improved fuel economy from their vehicles, and it seems a 25% fuel saving is there for the taking if aerodynamically efficient styling is employed.
Less burnt fuel also means less pollution. Operators do not need convincing of the benefits of drawbars — on the Continent they are extremely popular — but the UK Government continues to penalise them to the point of extinction.
Dare-Bryans' work leads to the inescapable conclusion that in the fuel consumption battle the at-tic will always lose to the drawbar. DTp please note.