NEW PROBLEMS NEW SOLUTIONS
Page 120
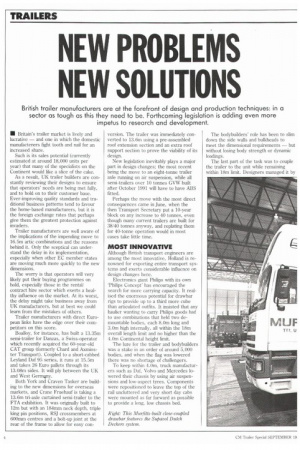
Page 121
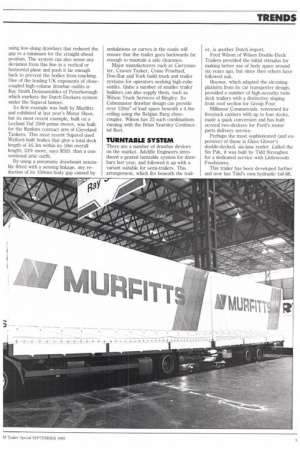
Page 122
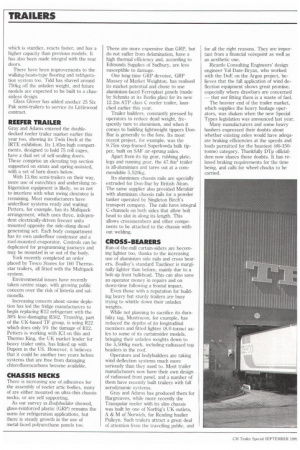
Page 123
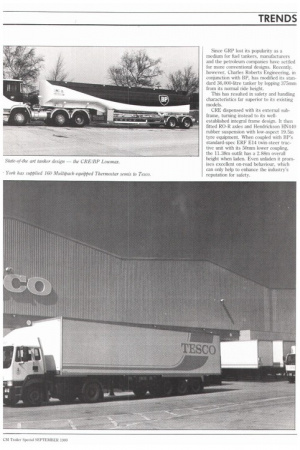
If you've noticed an error in this article please click here to report it so we can fix it.
British trailer manufacturers are at the forefront of design and production techniques: in a sector as tough as this they need to be. Forthcoming legislation is adding even more impetus to research and development.
• Britain's trailer market is lively and lucrative — and one in which the domestic manufacterers fight tooth and nail for an increased share.
Such is its sales potential (currently estimated at around 18,000 units per year) that many of the specialists on the Continent would like a slice of the cake.
As a result, UK trailer builders are constantly reviewing their designs to ensure that operators' needs are being met fully, and to hold on to their customer base. Ever-improving quality standards and traditional business patterns tend to favour the home-based manufacturers, but it is the foreign exchange rates that perhaps give them the greatest protection against invaders.
Trailer manufacturers are well aware of the implications of the impending move to 16.5m artic combinations and the reasons behind it. Only the sceptical can understand the delay in its implementation, especially when other EC member states are moving much more quickly to the new dimensions.
The worry is that operators will very likely put their buying programmes on hold, especially those in the rental' contract hire sector which exerts a healthy influence on the market. At its worst, the delay might take business away from UK manufacturers, but at best we could learn from the mistakes of others.
Trailer manufacturers with direct European links have the edge over their competitors on this score.
BoaNoy. for instance, has built a 13.35m semi-trailer for Danzas, a Swiss-operator which recently acquired the 60-year-old CAT group (formerly Chard and Axminster Transport). Coupled to a short-cabbed Leyland Daf 95 series, it runs at 15.5m and takes 26 Euro pallets through its 13.08m sides, It will ply between the UK and West Germuny.
Both York and Craven Tasker are building to the new dimensions for overseas markets, and Crane Fruehauf is taking a 13.6m tri-axle curtained semi-trailer to the PTA exhibition. It was originally built to 12m but with an 184min neck depth, triple king pin positions, RSJ crossmembers at 600rrun centres and a bolt-up joint at the rear of the frame to allow for easy con version. The trailer was immediately converted to 13.6m using a pre-assembled roof extension section and an extra roof support section to prove the viability of its design.
New legislation inevitably plays a major part in design changes; the most recent being the move to an eight-tonne trailer axle running on air suspension, while all semi-trailers over 10 tonnes GVW built after October 1991 will have to have ABS fitted.
Perhaps the move with the most direct consequences came in June, when the then Transport Secretary put a 10-year block on any increase to 40 tonnes, even though many current trailers are built for 38/40 tonnes anyway, and replating them for 40-tonne operation would in most cases take little time.
MOST INNOVATIVE
Although British transport engineers are among the most innovative. Holland is renowned for exporting entire transport systems and exerts considerable influence on design changes here.
Electronics giant Philips with its own Philips Concept' has encouraged the search for more carrying capacity. It realised the enormous potential for drawbar rigs to provide up to a third more cube than articulated outfits. It insisted that any haulier wanting to carry Philips goods had to use combinations that held two demountable bodies, each 8.0m long and 3.0m high internally, all within the 18m overall length limit and no higher than the 4.0m Continental height limit.
The lure for the trailer and bodybuilders was a stake in an order of around 5,000 bodies, and when the flag was lowered there was no shortage of challengers.
To keep within 4.0rn, truck manufacturers such as Daf, Volvo and Mercedes lowered their chassis by using air suspensions and low-aspect tyres. Components were repositioned to leave the top of the rail uncluttered and very short day cabs were mounted as far forward as possible to provide a long, low chassis bed. The bodybuilders' role has been to slim down the side walls and bulkheads to meet the dimensional requirements — but without losing body strength or dynamic loadings.
The last part of the task was to couple the trailer to the unit while remaining within 18m limit, Designers managed it by using low-slung drawbars that reduced the gap to a minimum for the straight-ahead position. The system can also sense any deviation from this line in a vertical or horizontal plane and push it far enough back to prevent the bodies from touching. One of the leading UK exponents of closecoupled high-volume drawbar outfits is Ray Smith Demountables of Peterborough which markets the Dutch Deckers system under the Supavol banner.
Its first example was built by Murfitts and exhibited at last year's Motor Show, but its most recent example, built on a Leyland Daf 2500 prime mover, was built for the Rankins contract arm of Cleveland Tankers. This most recent Supavol used WeIford-built bodies that give a total deck length of 16.3m within its 18m overall length; 33% more, says RSD, than a conventional artic outfit.
By using a pneumatic drawbeam assembly fitted with a sensing linkage, any reduction of its 150mm body gap caused by undulations or curves in the roads will ensure that the trailer goes backwards far enough to maintain a safe clearance.
Major manufacturers such as Carrymaster, Craven Tasker, Crane Fruehauf, Don-Bur and York build truck and trailer systems for operators seeking high-cube outfits. Quite a number of smaller trailer builders can also supply them, such as Wilson Truck Services of Bingley. Its Cubemaster drawbar design can provide over 120m3 of load space beneath a 4.0m ceiling using the Belgian Burg closecoupler. Wilson has 23 such combinations running with the Brian Yearsley Continental fleet.
TURNTABLE SYSTEM
There are a number of drawbar devices on the market. Adcliffe Engineers introduced a geared turntable system for drawbars last year, and followed it up with a variant suitable for semi-trailers. This arrangement. which fits beneath the trail er, is another Dutch import.
Fred Wilson of Wilson Double-Deck Trailers provided the initial stimulus for making better use of body space around six years ago, but since then others have followed suit.
Hoynor, which adapted the elevating platform from its car transporter design, provided a number of high-security twindeck trailers with a distinctive sloping front roof section for Group Four.
MilImoor Commercials, renowned for livestock carriers with up to four decks, made a quick conversion and has built several two-deckers for Ford's motor parts delivery service.
Perhaps the most sophisticated (and expensive) of these is Glass Glover's double-decked, six-lane reefer. Called the Six Pak, it was built by Tidd Strongbox for a dedicated service with Littlewoods Foodstores.
This trailer has been developed further and now has Tidd's own hydraulic tail-lift, which is sturdier, reacts faster, and has a higher capacity than previous models. It has also been made integral with the rear doors.
There have been improvements to the walking-beam-type flooring and refrigeration system too. Tidd has shaved around 750kg off the unladen weight, and future models are expected to be built to a chassisless design.
Glass Glover has added another 25 Six Pak semi-trailers to service its Littlewood contract.
REEFER TRAILER
Gray and Adams entered the doubledecked reefer trailer market earlier this year too, showing its Twin Deck at the IRTE exhibition. Its 1.83m-high compartments, designed to hold 75 roll cages, have a dual set of self-sealing doors. These comprise an elevating top section supported on struts and spring-assisted, with a set of barn doors below.
With 13.6m semi-trailers on their way, more use of eutechtics and undersItmg refrigeration equipment is likely, so as not to interfere with what swing clearance is remaining. Most manufacturers have underfloor systems ready and waiting: Petters, for example, has its Multipack arrangement, which uses three, independent electrically-driven freezer units mounted opposite the side-slung diesel generating set. Each body compartment has its own underfloor condensor and a roof-mounted evaporator. Controls can be duplicated for programming journeys and may be mounted in or out of the body.
York recently completed an order placed by Tesco Stores for 160 Thermostar trailers, all fitted with the Multipack system.
Environmental issues have recently taken centre stage, with growing public concern over the risk of listeria and salmonella.
Increasing concern about ozone depletion has led the fridge manufacturers to begin replacing R12 refrigerant with the 30% less-damaging R502. Transfrig, part of the UK-based IF group, is using R22 which does only 5% the damage of R12. Petters is working with ICI on this and Thermo King, the UK market leader for heavy trailer units, has linked up with Dupont in the US. However, it believes that it could be another two years before systems that are free from damaging chlorofluorocarbons become available.
CHASSIS NECKS
There is increasing use of adhesives for the assembly of reefer artic bodies, many of are either mounted on ultra-thin chassis necks, or are self supporting.
As our survey in Bodybuilder showed, glass-reinforced plastic (GRP) remains the norm for refrigeration applications, but there is steady growth in the use of metal-faced polyurethane panels too.
These are more expensive than GRP, but do not suffer from delkunination, have a high thermal efficiency and, according to Edmunds Supplies of Sudbury, are less susceptible to damage.
One long-time GRP devotee, GRP Massey of Market Weighton, has realised its market potential and chose to use aluminium-faced Ferroplast panels (made by Schmitz at its Berlin plan) for its new 12.2m ATP class C reefer trailer, launched earlier this year.
Trailer builders, constantly pressed by operators to reduce dead weight, frequently turn to aluminium, and when it comes to building lightweight tippers DonBur is generally to the fore. Its most recent project, for example, was the 9.75m step-framed Superlowda bulk tipper, built on SAF air-sprung axles.
Apart from its tip gear, rubbing plate, legs and running gear, the 47.8m3 trailer is all-aluminium and tares out at a commendable 5,520kg.
Its aluminium chassis rails are specially extruded for Don-Bur by British Alcan. The same supplier also provided Metalair with aluminium chassis rails for a powder tanker operated by Singleton Birch's transport company. The rails have integral C-channels on both sides that allow bolt head to slot in along its length. This allows crossmembers and other components to be attached to the chassis without welding.
CROSS-BEARERS
Run-of-the-mill curtain-siders are becoming lighter too, thanks to the increasing use of aluminium side rails and cross bearers. Boalloy's standard Tautliner is marginally lighter than before, mainly due to a bolt-up front bulkhead. This can also save an operator money in repairs and on down-time following a frontal impact.
Even those with a reputation for building heavy but sturdy trailers are busy trying to whittle down their unladen weights.
While not planning to sacrifice its durability tag, Montracon, for example, has reduced the depths of its longitudinal members and fitted lighter (8.0-tonne) axles to some of its curtainsider models, bringing their unladen weights down to the 5,500kg mark, including radiussed top headers in the roof.
Operators and bodybuilders are taking wind deflection systems much more seriously than they used to. Most trailer manufacturers now have their own design of radiussed front panel, and a number of them have recently built trailers with full aerodynamic systems.
Gray and Adams has produced them for Hargreaves, while more recently the Transpolar reefer with its slim chassis was built by one of Norfrig's UK outlets, A & M of Norwich, for Reading haulier Pulleyn. Such trailers attract a great deal of attention from the travelling public, and for all the right reasons. They are important from a financial veiwpoint as well as an aesthetic one.
Ricardo Consulting Engineers' design engineer Val Dare-Bryan, who worked with the DoE on the Argos project, believes that the full application of wind deflection equipment shows great promise, especially where drawbars are concerned — that not fitting them is a waste of fuel.
The heavier end of the trailer market, which supplies the heavy haulage operators, was shaken when the new Special Types legislation was announced last year.
Many manufacturers and some heavy hauliers expressed their doubts about whether existing axles would have adequate braking efficiencies at the speeds and loads permitted for the heaviest (80450tonne) category. Thankfully DTp officialdom now shares those doubts. It has relaxed braking requirements for the time being, and calls for wheel chocks to be carried. Since GRP lost its popularity as a medium for fuel tankers, manufacturers and the petroleum companies have settled for more conventional designs. Recently. however, Charles Roberts Engineering, in conjunction with BP, has modified its standard 36,000-litre tanker by lopping 375mm from its normal ride height.
This has resulted in safety and handling characteristics far superior to its existing models.
CRE dispensed with its external subframe, turning instead to its wellestablished integral frame design. It then fitted RO-R axles and Hendrickson HN440 rubber suspension with low-aspect 19.5in tyre equipment. When coupled with BP's standard-spec ERF E14 twin-steer tractive unit with its 50mm lower coupling, the 11.38m outfit has a 2.88m overall height when laden. Even unladen it promises excellent on-road behaviour, which can only help to enhance the industry's reputation for safety.