A fitting job There are plenty of flat spots in
Page 28
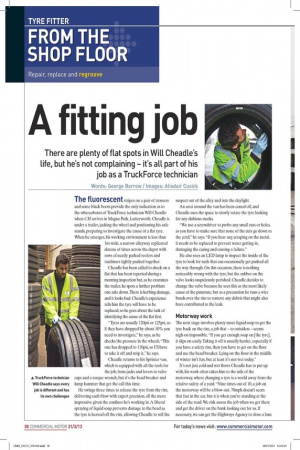
Page 30
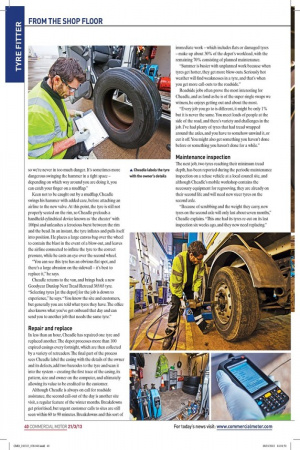
Page 31
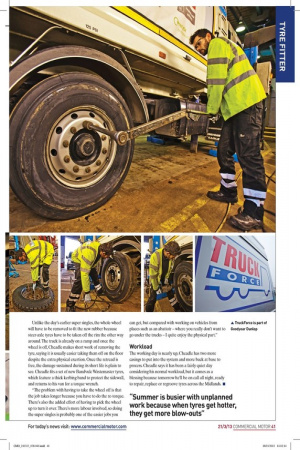
If you've noticed an error in this article please click here to report it so we can fix it.
Will Cheadle's life, but he's not complaining ifs all part of his job as a TruckForce technician Words: George Barrow! Images: Alisdair Cusick The fluorescent stripes on a pair of trousers and some black boots provide the only indication as to the whereabouts of TruckForce technician Will Cheadle when CM arrives in Magna Park, Lutterworth. Cheadle is under a trailer, jacking the wheel and positioning his axle stands, preparing to investigate the cause of a flat tyre. When he emerges, his working environment is less than lm wide, a narrow alleyway replicated dozens of times across the depot with rows of neatly parked reefers and tautliners tightly packed together.
Cheadle has been called to check on a flat that has been reported during a morning inspection but, as he examines the trailer, he spots a further problem one axle down. There is kerbing damage, and it looks bad. Cheadle's experience tells him the tyre will have to be replaced, so he goes about the task of identifying the cause of the flat first.
"Tyres are usually 120psi or 125psi, so if they have dropped by about 10% you need to investigate," he says, as he checks the pressure in the wheels. "This one has dropped to 110psi, so I'll have to take it off and strip it," he says.
Cheadle returns to his Sprinter van, which is equipped with all the tools for the job, from jacks and levers to valve caps and a torque wrench, but it's the bead breaker and lump hammer that get the call this time.
He swings three times to release the tyre from the rim, delivering each blow with expert precision, all the more impressive given the confines he's working in. A liberal spraying of liquid soap prevents damage to the bead as the tyre is heaved off the rim, allowing Cheadle to roll the suspect out of the alley and into the daylight.
An area around the van has been coned off and Cheadle uses the space to slowly rotate the tyre looking for any dubious marks.
"We use a screwdriver to probe any small cuts or holes, as you have to make sure that none of the cuts go down to the cord," he says. "If you hear any scraping on the metal, it needs to be replaced to prevent water getting in, damaging the casing and causing a failure."
He also uses an LED lamp to inspect the inside of the tyre to look for nails that can occasionally get pushed all the way through. On this occasion, there is nothing noticeably wrong with the tyre, but the rubber on the valve looks suspiciously perished. Cheadle decides to change the valve because he sees this as the most likely cause of the puncture, but as a precaution he runs a wire brush over the rim to remove any debris that might also have contributed to the leak.
Motorway work The next stage involves plenty more liquid soap to get the tyre back on the rim, a job that — to outsiders — seems nigh-on impossible. "If you get enough soap on [the tyre], it slips on easily. Taking it off is usually harder, especially if you have a safety rim, then you have to get on the floor and use the bead breaker. Lying on the floor in the middle of winter isn't fun, but at least it's not wet today."
It's not just cold and wet floors Cheadle has to put up with, his work often takes him to the side of the motorway, where changing a tyre is a world away from the relative safety of a yard. "Nine times out of 10, a job on the motorway will be a blow-out. 70mph doesn't seem that fast in the car, but it is when you're standing at the side of the road. We risk assess the job when we get there and get the driver on the bank looking out for us. If necessary, we can get the Highways Agency to close a lane so we're never in too much danger. It's sometimes more dangerous swinging the hammer in a tight space — depending on which way around you are doing it, you can catch your finger on a mudflap."
Keen not to be caught out by a mudflap, Cheadle swings his hammer with added care, before attaching an airline to the new valve. At this point, the tyre is still not properly seated on the rim, so Cheadle preloads a handheld cylindrical device known as 'the cheater' with 100psi and unleashes a ferocious burst between the rim and the bead. In an instant, the tyre inflates and pulls itself into position. He places a large canvas bag over the wheel to contain the blast in the event of a blow-out, and leaves the airline connected to inflate the tyre to the correct pressure, while he casts an eye over the second wheel.
"You can see this tyre has an obvious flat spot, and there's a large abrasion on the sidewall — it's best to replace it," he says.
Cheadle returns to the van, and brings back a new Goodyear Dunlop Next Tread Retread 385/65 tyre. "Selecting tyres [at the depot] for the job is down to experience," he says. "You know the site and customers, but generally you are told what tyres they have. The office also knows what you've got onboard that day and can send you to another job that needs the same tyre."
Repair and replace In less than an hour, Cheadle has repaired one tyre and replaced another. The depot processes more than 100 expired casings every fortnight, which are then collected by a variety of retreaders. The final part of the process sees Cheadle label the casing with the details of the owner and its defects, add two barcodes to the tyre and scan it into the system — creating the first trace of the casing, its pattern, size and owner on the computer, and ultimately allowing its value to be credited to the customer.
Although Cheadle is always on call for roadside assistance, the second call-out of the day is another site visit, a regular feature of the winter months. Breakdowns get prioritised, but urgent customer calls to sites are still seen within 60 to 90 minutes. Breakdowns and this sort of immediate work — which includes flats or damaged tyres — make up about 30% of the depot's workload, with the remaining 70% consisting of planned maintenance.
"Summer is busier with unplanned work because when tyres get hotter, they get more blow-outs. Seriously hot weather will find weaknesses in a tyre, and that's when you get more call-outs to the roadside."
Roadside jobs often prove the most interesting for Cheadle, and as fond as he is of the super single swaps we witness, he enjoys getting out and about the most.
"Every job you go to is different, it might be only 1% but it is never the same. You meet loads of people at the side of the road, and there's variety and challenges in the job. I've had plenty of tyres that had tread wrapped around the axles, and you have to somehow unwind it, or cut it off. You might also get something you haven't done before or something you haven't done for a while."
Maintenance inspection The next job, two tyres reaching their minimum tread depth, has been reported during the periodic maintenance inspection on a refuse vehicle at a local council site, and although Cheadle's mobile workshop contains the necessary equipment for regrooving, they are already on their second life and will need new steer tyres on the second axle.
"Because of scrubbing and the weight they carry, new tyres on the second axle will only last about seven months," Cheadle explains. "This one had its tyres re-cut on its last inspection six weeks ago, and they now need replacing."
Unlike the day's earlier super singles, the whole wheel will have to be removed to fit the new rubber because steer-axle tyres have to be taken off the rim the other way around. The truck is already on a ramp and once the wheel is off Cheadle makes short work of removing the tyre, saying it is usually easier taking them off on the floor despite the extra physical exertion. Once the retread is free, the damage sustained during its short life is plain to see. Cheadle fits a set of new Bandvulc Wastemaster tyres, which feature a thick kerbing band to protect the sidewall, and returns to his van for a torque wrench.
"The problem with having to take the wheel off is that the job takes longer because you have to do the re-torque. There's also the added effort of having to pick the wheel up to turn it over. There's more labour involved, so doing the super singles is probably one of the easier jobs you can get, but compared with working on vehicles from TruckForce is part of places such as an abattoir — where you really don't want to Goodyear Dunlop go under the trucks — I quite enjoy the physical part."
Workload The working day is nearly up, Cheadle has two more casings to put into the system and more back at base to process. Cheadle says it has been a fairly quiet day considering his normal workload, but it comes as a blessing because tomorrow he'll be on call all night, ready to repair, replace or regroove tyres across the Midlands. •