Pistons Shaped to Suit Temperatures
Page 51
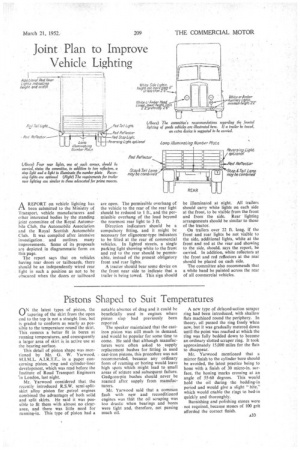
If you've noticed an error in this article please click here to report it so we can fix it.
Oo the latest types of piston, the tapering of the skirt from the open end to the top is not a straight line, but is graded to conform as nearly as possible to the temperature round the skirt. This ensures a better fit in bores at running temperatures, and consequently a larger area of skirt is in active use at the bearing surface.
This detail of piston shape was mentioned by Mr. G. W. Yarwood, A.I.R.T.E„ in a paper concerning piston, ring and cylinder-liner development, which was read before the Institute of Road Transport Engineers 'in London, last night.
Mr. Yarwood considered that the recently introduced R.S.W. semi-splitskirt alloy piston for .petrol engines combined the advantages of both solid and split skirts. He said it was possible to fit them with almost no clearance, and there was little need for running-in. This type of piston had a
notable absence of drag and it could be beneficially used in engines where piston slap had previously been reported.
The speaker maintained that the castiron piston was still much in demand, and would be popular for some time to come. He said that although manufacturers were often asked to supply replacement bushes for fitting in used cast-iron pistons, this procedure was not recommended, because any ordinary form of reaming or boring would leave high spots which might lead to small areas of seizure and subsequent failure. Gudgeon-pin bushes should never be reamed after supply from manufacturers.
Mr. Yarwood said that a common fault with new and reconditioned engines was that the oil scraping was too drastic when bearings and bores were tight and, therefore, not passing much oil.
A new type of delayed-action scraper ring had been introduced, with shallow flats machined round the periphery. In theory, oil passed the ring freely when new, but it was gradually metered down until the point was reached at which the ring was fully bedded down to become an ordinary slotted scraper ring. It took approximately 15,000 miles for the flats to disappear.
Mr. Yarwood mentioned that a mirror finish to the cylinder bore should be avoided, the latest practice being to hone with a finish of 30 micro-in, surface, the honing marks crossing at an angle of 55-60 degrees. This would hold the oil during the bedding-in period and would give a slight "bite," which would enable the rings to bed-in quickly and thoroughly.
Burnishing and polishing stones were not required,, because stones of 100 grit afforded the correct finish.