MAINTENANCE FC PROFIT
Page 42
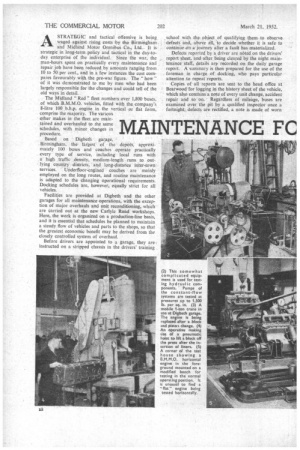
Page 43
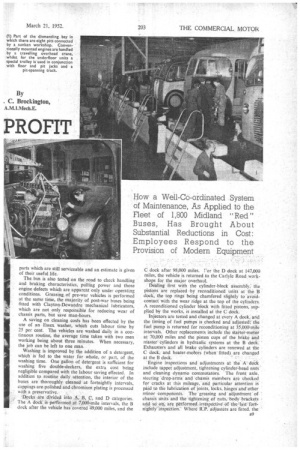
Page 44
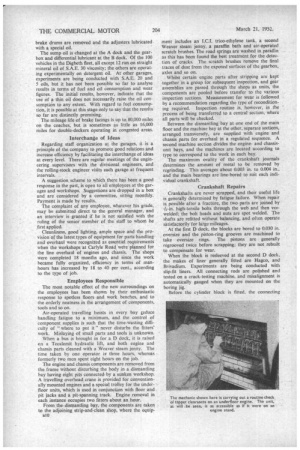
Page 45
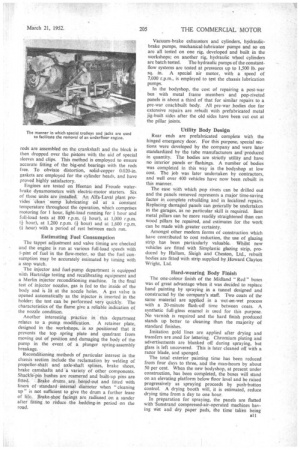
Page 46
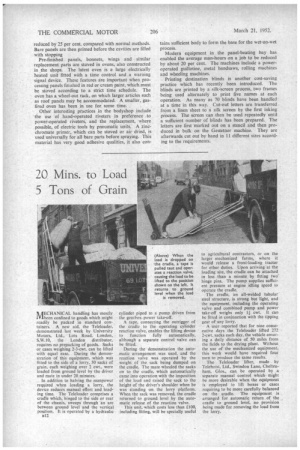
If you've noticed an error in this article please click here to report it so we can fix it.
How a Well-Co-ordinated System Of Maintenance, As Applied to the Fleet of 1,800 Midland• "Red" Buses, Has Brought About Substantial Reductions in Cost: Employees Respond to the Provision of Modern Equipment A, STRATEGIC and tactical offensive is being waged against rising costs by the Birmingham and Midland Motor Omnibus Co.., Ltd.It is strategic in long-term policy and tactical in the day-today enterprise of the individual. Since the war, the man-hours spent on practically every maintenance and repair job have been reduced by amounts ranging from 10 to 50 per cent., and in a few instances the cost compares favourably with the pre-war figure, The " how " of it was demonstrated to me by men who had been largely responsible for the changes and could tell of the old ways in detail.
The Midland " Red" fleet numbers over 1,800 buses, of which B.M.M.O. vehicles, fitted with the-company's 8-litre 100 b.h.p. engine in the vertical orflat form, comprise the majority. The various other makes in the fleet are maintained and overhauled to the same schedules, with minor changes in procedure.
Based on Digbeth garage, Birmingham, the largest of the depots approximately 100 buses and coaches operate practically every type of service, including local runs with a high traffic density, medium-length runs to outlying country districts, and long-distance inter-town services. Underfloor-engined coaches are mainly employed on the long routes, and routine maintenance is adapted to the changing operational requirements. Docking schedules are, however, equally strict for all vehicles.
Facilities are provided at Digbeth and the other garages for all maintenance operations, with the exception of major overhauls and unit reconditioning, which are carried out at the •new Carlyle Road workshops. Here, the work is organized on a production-line basis, and it is essential that schedules be planned to maintain a steady flow of vehicles and parts to the shops, so that the greatest economic benefit may be derived from the closely controlled system of overhaul.
Before drivers are appointed to a garage, they are instructed on a stripped chassis in the drivers' training
school with the object of qualifying them to observe defects and, above all, to decide whether it is safe to continue on a journey after a fault has materialized.
Defects reported by a driver are noted on the drivers' report sheet, and after being cleared by the night maintenance staff, details are recorded on the daily garage report. A summary is then prepared for the use of the foreman. in charge of docking, who pays particular attention to repeat reports.
Copies of all reports are sent to the head office at Bearwood for logging hi the history sheet of the vehicle, which also contains a note of every unit change, accident repair and so on. Regardless of mileage, buses are examined over the pit by a qualified inspector once .a fortnight; defects are rectified, a note is made of worn parts which are still serviceable and an estimate is given of their useful life.
The bus is also tested on the road to check handling and braking characteristics, pulling power and those engine defects which are apparent only under operating conditions. Greasing. of pre-war vehicles is performed at the same time, the majority of post-war buses being fitted with Clayton-Dewandre mechanical lubricators, which are not only responsible for reducing wear of chassis parts, but save man-hours.
A saving on cleaning costs has been effected by the use of an Essex washer, which cuts labour time by• 25 per cent. The vehicles are washed daily in a continuous routine, the average time taken with two men working being about three minutes. When necessary, the job can be left to one man.
Washing is improved by the addition of a detergent, which is fed to the water for whole, or part, of the washing time. One gallon of detergent is sufficient for washing five double-deckers, the extra cost being negligible compared with the labour saving effected. In addition to routine daily attention, the interior of the buses are thoroughly cleaned at fortnightly intervals, cappings are polished and chromium plating is processed with a preservative.
Docks are divided into A, B, C, and D categories. The A dock is performed at 7,000 mile intervals, the B dock after the vehicle has covered 49,000 miles, and the C dock after 98,000 miles. For the D dock at 147,000 miles, the vehicle is returned to the Carlyle Road workshops for the major overhaul.
Dealing first with the cylinder block assembly ; the pistons are replaced -by reconditioned units at the cloak, the top rings being chamfered slightly to 'avoidcontact with the wear ridge at the top of the cylinders. A reconditioned cylinder block with fitted pistons, supplied 1* the works, is installed at the C dock.
Injectors are tested and changed at every A dock, and the timing of fuel 'pumpsis checked and adjusted; the fuel pump is returned for reconditioning at 35,000'-mile intervals. Other replacements include the starter motor at 70,000 miles and the piston cups of the brake and Master Cylinders in hydraulic systems at the •B doek: ' Exhausters and all brake cylinders are renewed at the C -dock; and heater-motors (when' fitted) are changed at the dock. 'Engine inspections and adjustments at the A' dad( include tappet adjustment, tightening cylinder-head nuts' , and cleaning •dynattio commutators. The front axle, steering 'drop-am-is and chassis members are checked for cracks at this mileage, and, Particular attention is paid to the lubrication of joints, locks, hinges' and' other rriinor Compotients.1 The greasing and adjuStirierit' ofchassis units arid the tightening Of nuts,hodyThratkets and so On; are performed :irrespective' of thelast'fortnightly inspection: Where RP. adjusters are fitted, the'
brake drums are removed and the adjusters lubricated. with a special oil.
The sump oil is changed at the A dock and the gearbox and differential lubricant at the B dock. Of the 100 vehicles in the Digbeth fleet, all except 12 run on straight mineral oil of S.A.E. 30 viscosity; the others are operating experimentally on detergent oil. At other garages, experiments are being conducted with S.A.E. 20 and 5 oils, but it has not been possible so far to analyse results in terms of fuel and oil consumption and wear figures. The initial results, however, indicate that the use of a thin oil does not necessarily raise the oil consumption to any extent. With regard to fuel consumption, it is possible at this stage only to say that the results so far are distinctly promising.
The mileage life of brake facings is up to 80,000 miles on the coaches, but is sometimes as little as 16,000 miles for double-deckers operating in congested areas.
Interchange of Ideas
Regarding staff organization at the garages, it is a principle of the company to promote good relations and increase efficiency by facilitating the interchange of ideas at every level. There are regular meetings of the engineering supervisors with the divisional engineers, and the-rolling-stock engineer visits each garage at frequent intervals.
A suggestion scheme to which there has been a good response in the past, is open to all employees at the garages and workshops. Suggestions are dropped in a. box and are considered by a committee, sitting monthly. Payment is made by results.
The complaint of any employee, whatever his grade, may be submitted direct to the general manager, and an interview is granted if he is not satisfied with the ruling of the senior member, of the staff to whom he _first applied.
Cleanliness, good lighting, ample space and the provision of the latest types of equipment for parts handling arid overhaul were recognized as essential requirements when the workshops at Carlyle Road Were planned for the line overhaul of engines and chassis. The shops were completed 18 months ago, and since the work became fully organized, efficiency in terms of manhours has increased by 18 to 40 per cent., according to the type of job.
Employees Responsible The most notable effect of the new surroundings on the employees has been shown by their enthusiastic response to spotless floors and work benches, and to the orderly neatness in the arrangement of components, tools and so on.
Air-operated travelling hoists in every bay teduce handling fatigue to a minimum, and the control of component supplies is such that the time-wasting difficulty of "where to put it" never disturbs the fitters' work. Mislaying of small parts and tools is unknown.
When a bus is brought in for a D dock, it is raised on a Tecalemit hydraulic lift, and both engine and chassis parts cleaned with a Weaver steam jenny. The time taken by one operator is three hours, whereas formerly two men spent eight hours on the job.
The engine and chassis components are removed from the frame without disturbing the body in a dismantling bay having eight pits connected by a sunken workshop. A travelling overhead crane is provided for conventionally mounted engines, and a special trolley for the Underfloor units, which is used in conjunction with floor and pit jacks and a pit-spanning track. Engine removal in each instance occupies two fitters about an hour. • From the dismantling bay, the components are taken to the adjoining strip-and-clean shop, where the equip 1310
ment includes an T.C.F. trico-ethylene tank, a second Weaver steam jenny, a paraffin bath and air-operated scratch brushes. The road springs are washed in paraffin as this has been found the best treatment for the detection of cracks. The scratch brushes remove the final traces of dust from the exposed surfaces of the gearbox, axles and so on.
Whilst certain engine parts after stripping are kept together in a group for subsequent inspection, and gear assemblies are passed through the shops as units, the components are pooled before transfer to the various inspection sections. Measurement for wear is followed by a recommendation regarding the type of reconditioning required. Inspection routine is, however, in the process of being transferred to a central section, where all parts will be checked.
Between the dismantling bay at one end of the main floor and the machine bay at the other, separate sections, arranged transversely, are supplied with engine and chassis parts for overhaul in a regulated sequence. A second machine section divides the engineand chassisunit bays, and the machines are located according to type to correspond to the work in each bay.
The maximum ovality of the crankshaft journals determines the amount of metal to be removed by regrinding. This averages about 0.003 in. to 0.004 in., and the main bearings are line-bored to suit each individual crankshaft.
Crankshaft Repairs
• Crankshafts are never scrapped, and their useful life is generally determined by fatigue failure. When repair
possible after a fracture, the two parts are joined by *-in. high-tensile bolts through the web and then veewelded; the bolt heads and nuts are spot welded. The shafts are refitted without balancing, and often operate satisfactorily for large mileages.
At the first D dock, the blocks are bored to 0.030 in. oversize and the piston-ring grooves are machined to take oversize rings. The pistons are generally regrooved twice before scrapping; they are not rebuilt to compensate for wear.
When the block is resleeved at the second D dock, the makes of finer generally fitted are Hagco, and Brivadium. Experiments are being conducted with slip-fit liners. All connecting rods are polished and tested on a crack-testing machine, and misalignment is automatically gauged when they are mounted on the boring jig.
Before the cylinder block is fitted, the connecting
rods are assembled on the crankshaft and the block is• then dropped over the pistons with the aid of special sleeves and clips. This method is employed to ensure accurate fitting of the big-end bearings with the rods free. To obviate distortion, solid-copper 0.020-in, gaskets are employed for the cylinder heads, and have proved highly satisfactory.
Engines are tested on Heenan and Froude waterbrake dynamometers with electric-motor starters. Six of these units are installed An Alfa Laval plant provides Clean sump `lubricating oil at a constant temperature throughout the operation, which comprises motoring for 1 hour, light-load running for 1 hour and full-load tests at 800 r.p.m. (1. hour), at 1,000 r.p.m. (i hour), at 1,200 r.p.m. (f hour) and at 1,600 r.p.m. (71 hour) with a period of rest between each run.
Estimating Fuel Consumption
The tappet adjustment and valve timing are checked and the engine is run at various full-load speeds with .17-pint of fuel in the flow-meter, so that the fuel consumption may be accurately estimated by timing with a stop watch.
The injector and fuel-pump department is equipped With Hartridge testing and recalibrating equipment and a Merlin injector reconditioning machine. In the final test of injector nozzles, gas is fed to the inside of the body and is lit at the nozzle holes. A gas valve is opened automatically as the injector is inserted in the holder; the test can be performed very quickly. The characteristics of the flame give a reliable indication of the nozzle condition.
Another interesting practice in this department relates to a pump modification. A retainer plate, designed in the workshops, is so positioned that it prevents the top spring plate and quadrant from moving out of position and damaging the body of the pump in the event of a plunger spring-assembly breakage. 'Reconditioning methods of particular interest in the chassis section include the reclamation by welding of propeller-shalt and axle-shaft splines, brake shoes, brake camshafts arid 'a variety of other components. Shackle:pin bushes are reamered and built-up pins are fitted. . Brake drums are bored out and fitted with liners of standard internal diameter when "cleaning up" is not sufficient to give the drum a further lease of life. Brake -shoe facing§ are radiused..on a sander after' fitting to reduce the bedding-in period on the road. Vacuum-brake exhausters and cylinders, hydraulicbrake pumps, mechanical-lubricator pumps and so on are all tested on one rig, developed and built in the workshops; on another rig, hydraulic wheel cylinders are batch tested. The hydraulic pumps of the constantflow systems are tested at pressttres up to l,500 lb. per sq. in. A special air motor, with a speed of 7,000 r.p.m., is employed to test the chassis lubrication pumps.
In the bodyshop, the cost of repairing a post-war bus with metal frame members and pop-riveted panels is about a third of that for similar repairs to a pre-war coachbuilt body. All pre-war bodies due for extensive repairs are rebuilt with prefabricated metal jig-built sides after the old sides have been cut out at the pillar joints.
Utility Body Design
Rear ends are prefabricated complete with the hinged emergency door. For this purpose, special sections were developed by the company and were later standardized by the tube manufacturers and produced in quantity. The bodies are strictly utility and have no interior panels or flashings. A number of bodies was completed in this way in the bodyshop at low cost. The job was later undertaken by contractors, and well over 400 vehicles have now been rebuilt in this manner.
The ease with which pop rivets can be drilled out and the panels removed represents a major time-saving factor in complete rebuilding and in localized repairs. Replacing damaged panels can generally be undertaken in the garages, as no particular skill is required. Bent metal pillars can be more readily straightened than can wood pillars be repaired, and estimates for the work can be made with greater certainty.
Amongst other modern forms of construction which have contributed to cost reduction, the use of glazing strip has been particularly valuable. Whilst new vehicles are fitted with Simplastic glazing strip, produced by Hallam, Sleigh and Cheston, Ltd., rebuilt bodies are fitted with strip supplied by Howard Clayton Wright, Ltd.
Hard-wearing Body Finish
The one-colour finish of the Midland "Red" buses was of great advantage when it was decided to replace hand painting by spraying in a tunnel designed and constructed by the company's staff. Two coats of the same material are applied in a wet-On-wet process with a 20-minute flash-off time between coats. A synthetic full-gloss enamel is used for this purpose. No varnish is required and the hard finish produced stands up better to cleaning than the majority of standard finishes.
Imitation gold lines are applied after drying and transfers are -used for lettering. Chromium plating and advertisements are blanked off during spraying, but glass is left uncovered. This is later cleaned off with a razor blade, and sponged.
The total exterior painting time has been reduced from four days to three, and the man-hours by about 50 per cent. When the new bodyshop, at present under construction, has been completed, the buses will stand on an elevating platform below floor level and be raised progressively as spraying proceeds by push-button control. A drying booth will, it is estimated, reduce drying time from a day to one hour.
In preparation for spraying, the panels are flatted with .Sunstrandcompressed-air-operated machines having wet and dry paper Pads, the time taken being
reduced by 25 per cent. compared with normal methods. Bare panels are then primed before the cavities are filled with stopping Pre-finished panels, bonnets, wings and similar replacement parts are stoved in ovens, also constructed in the shops. The latest oven is a large electrically heated unit fitted with a time control and a warning signal device. These features are important when processing panels finished in red or cream paint, which must be stoved according to a strict time schedule. The oven has a wheel-out rack, on which larger articles such as roof panels may be accommodated. A smaller, gasfired oven has been in use for some time.
Other interesting practices in the bodyshop include the use of hand-operated riveters in preference to power-operated riveters, and the replacement, where possible, of electric tools by pneumatic units. A zincchromate primer, which can be stoved or air dried, is used universally for all bare parts before spraying. This material has very good adhesive qualities, it also con
tains sufficient body to form the base for the wet-on-wet process.
Modern equipment in the panel-beating bay has enabled the average man-hours on a job to be reduced by about 20 per cent. The machines include a poweroperated guillotine, metal bandsaws, rolling machines and wheeling machines.
Printing destination blinds is another cost-saving practice which has recently been introduced. The blinds are printed by a silk-screen process, two frames being used alternately to print five names at each operation. As many as 70 blinds have been handled at a time in this way. Cut-out letters are transferred from a linen sheet to a silk screen by the first inking process. The screen can then be used repeatedly until a sufficient number of blinds has been prepared. The letters are first marked out on a stencil and then produced in bulk on the Gestetner machine. They are afterwards cut out by hand in 11 different sizes according to the requirements.
By . C. Brockington,
A .M.I.Mrech.E.