Don't trail behind
Page 60
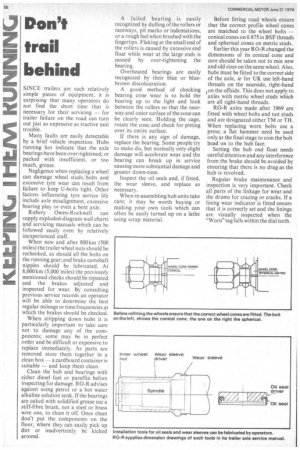
If you've noticed an error in this article please click here to report it so we can fix it.
SINCE trailers are such relatively simple pieces of equipment, it is surprising that many operators do not find the short time that is necessary for their servicing — for trailer failure on the road can turn out just as expensive as tractive unit trouble.
Many faults are easily detectable by a brief vehicle inspection. Hubs running hot indicate that the axle bearings have been over-tightened; or packed with insufficient, or too much, grease.
Negligence when replacing a wheel can damage wheel studs/ bolts and excessive tyre wear can result from failure to keep U-bolts tight. Other factors influencing tyre service life include axle misalignment, excessive bearing play or even a bent axle.
Rubery Owen-Rockwell can supply exploded-diagram wall charts and servicing manuals which can be followed easily even by relatively inexperienced staff.
When new and after 800 km (500 miles) the trailer wheel nuts should be rechecked, as should all the bolts on the running gear; and brake camshaft nipples should be lubricated. At 8,000 km (5,000 miles) the previously mentioned checks should be repeated and the brakes adjusted and inspected for wear. By consulting previous service records an operator will be able to determine the best regular mileage or time frequencies at which the brakes should be checked.
When stripping down hubs it is particularly important to take care not to damage any of the components; some may be in perfect order and be difficult or expensive to replace immediately. As parts are removed store them together in a clean box — a cardboard container is suitable — and keep them clean.
Clean the hub and bearings with either diesel fuel or paraffin before inspecting for damage. RO-R advises against using petrol or a hot water alkaline solution tank. If the bearings are caked with solidified grease use a stiff-fibre brush, not a steel or brass wire one, to clean it off. Once clean don't put the components on the floor, where they can easily pick up dirt or inadvertently be kicked around. A failed bearing is easily recognized by dulling of the rollers or raceways, pit marks or indentations, or a rough feel when brushed with the fingertips. Flaking at the small end of the rollers is caused by excessive end float while wear at the large ends is caused by over-tightening the bearing.
Overheated bearings are easily recognized by their blue or bluebrown discolouration.
A good method of checking bearing cone wear is to hold the bearing up to the light and look between the rollers so that the raceway and outer surface of the cone can be clearly seen. Holding the cage, rotate the cone and check for pitting over its entire surface.
If there is any sign of damage, replace the bearing. Some people try to make do, but normally only slight damage will accelerate wear and the bearing can break up in service causing more substantial damage and greater down-time.
Inspect the oil seals and, if fitted, the wear sleeve, and replace as necessary.
When re-assembling hub units take care; it may be worth buying or making your own tools which can often be easily turned up on a lathe using scrap material. Before fitting road wheels ensure that the correct profile wheel cones are matched to the wheel bolts — conical cones on 0.875 in BSF threads and spherical cones on metric studs.
Earlier this year RO-R changed the dimensions of its conical cone and care should be taken not to mix new and old sizes on the same wheel. Also, hubs must be fitted to the correct side of the axle, ie for UK use left-hand threads on the nearside, right-hand ion the offside. This does not apply to axles with metric wheel studs which are all right-hand threads.
RO-R axles made after 1969 are fitted with wheel bolts and not studs and are designated either TM or TH. When replacing worn bolts use a press; a flat hammer need be used only at the final stage to coin the bolt head on to the hub face.
Setting the hub end float needs careful attention and any interference from the brake should be avoided by ensuring that there is no drag as the hub is revolved.
Regular brake maintenance and inspection is very important. Check all parts of the linkage for wear and the drums for crazing or cracks. If a lining wear indicator is fitted ensure that it is correctly set and the linings are visually inspected when the "Worn" tag falls within the dial teeth.