The voice of the operator
Page 36
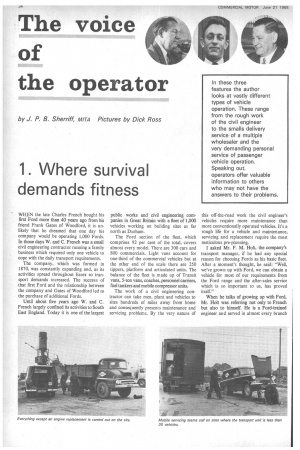
Page 37
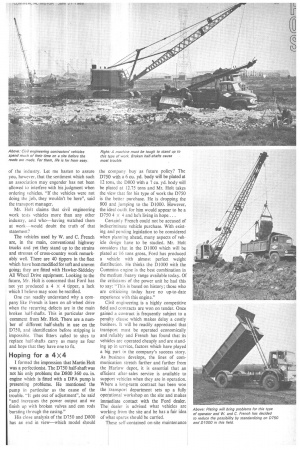
Page 38
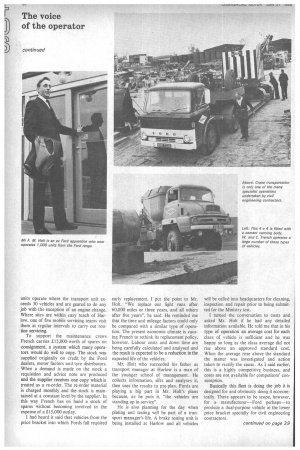
Page 41
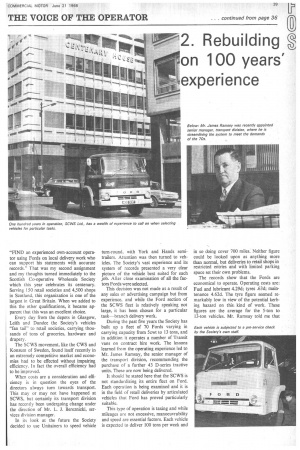
Page 42
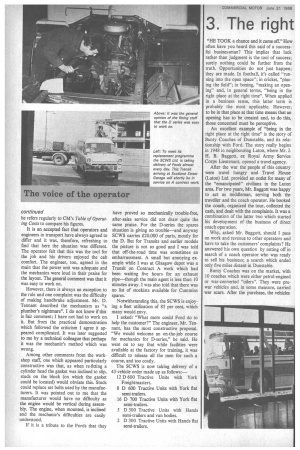
If you've noticed an error in this article please click here to report it so we can fix it.
by J. P. B. Sherriff, MITA Pictures by Dick Ross
1. Where survival demands fitness
WHEN the late Charles French bought his first Ford more than 40 years ago from his friend Frank Gates of Woodford, it is unlikely that he dreamed that one day his company would be operating 1,000 Fords. In those days W. and C. French was a small civil engineering contractor running a family business which required only one vehicle to cope with the daily transport requirements.
The company, which was formed in 1870, was constantly expanding and, as its activities spread throughout Essex so transport demands increased. The success of that first Ford and the relationship between the company and Gates of Woodford led to the purchase of additional Fords.
Until about five years ago W. and C. French largely confined its activities to South East England. Today it is one of the largest public works and civil engineering companies in Great Britain with a fleet of 1,000 vehicles working on building sites as far north as Durham.
The Ford section of the fleet, which comprises 92 per cent of the total, covers almost every model. There are 300 cars and 800 commercials. Light vans account for one-third of the commercial vehicles but at the other end of the scale there are 250 tippers, platform and articulated units. The balance of the fleet is made up of Transit vans, 5-ton vans, coaches, personnel carriers, fuel tankers and mobile compressor units.
The work of a civil engineering contractor can take men, plant and vehicles to sites hundreds of miles away from home and consequently presents maintenance and servicing problems. By the very nature of this off-the-road work the civil engineer's vehicles require more maintenance than more conventionally operated vehicles. It's a rough life for a vehicle and maintenance, servicing and replacement require the most meticulous pre-planning.
I asked Mr. F. M. Holt, the company's transport manager, if he had any special reason for choosing Fords as his basic fleet. After a moment's thought, he said: "Well, we've grown up with Ford, we can obtain a vehicle for most of our requirements from the Ford range and the after-sales service which is so important to us, has proved itself."
When he talks of growing up with Ford, Mr. Holt was referring not only to French but also to himself. He is a Ford-trained engineer and served in almost every branch
of the industry. Let me hasten to assure you, however, that the sentiment which such an association may engender has not been allowed to interfere with his judgment when ordering vehicles. "If the vehicles were not doing the job, they wouldn't be here", said the transport manager.
Mr. Holt claims that civil engineering work tests vehicles more than any other industry, and who—having watched them
at work would doubt the truth of that statement?
The vehicles used by W. and C. French are, in the main, conventional highway trucks and yet they stand up to the strains and stresses of cross-country work remarkably well. There are 40 tippers in the fleet which have been modified for soft and uneven going; they are fitted with Hawker-Siddeley All Wheel Drive equipment. Looking to the future, Mr. Holt is concerned that Ford has not yet produced a 4 x 4 tipper, a lack which I believe may soon be rectified.
One can readily understand why a company like French is keen on all-wheel drive when the recurring defects are in the main broken half-shafts. This in particular drew comment from Mr. Holt. There are a number of different half-shafts in use on the D750, and identification before stripping is impossible. Thus fitters called to sites to replace half-shafts carry as many as four and hope that they have one to fit.
Hoping for a 4x4
I formed the impression that Martin Holt was a perfectionist. The D750 half-shaft was not his only problem; the D800 360 cu. in. engine which is fitted with a DPA pump is presenting problems. He mentioned • the pump in particular as the cause of the trouble. "It gets out of adjustment", he said "and increases the power output and we finish up with broken valves and con rods bursting through the casing."
His close analysis of the D750 and D800 has an end in view—which model should the company buy as future policy? The D750 with a 6 Cu. yd. body will be plated at 12 tons, the D800 with a 7 Cu. yd. body will be plated at 12.75 tons and Mr. Holt takes the view that for his type of work the D750 is the better purchase. He is dropping the 800 and jumping to the • D1000. However, the ideal outfit for him would appear to be a D750 4 x 4 and he's living in hope ...
Certainly French could not be accused of indiscriminate vehicle purchase. With existing and pending legislation to be considered when planning ahead, many aspects of vehicle design have to be studied. Mr. Holt considers that in the D1000 which will be plated at 16 tons gross, Ford has produced a vehicle with almost perfect weight distribution. He thinks the D1000 with the Cummins engine is the best combination in the medium /heavy range available today. Of the criticisms of the power unit he had this to say: "This is based on history; those who are criticizing today have no up-to-date experience with this engine."
Civil engineering is a highly competitive field and contracts are won on tender. Once gained a contract is frequently subject to a penalty clause which makes delay a costly business. It will be readily appreciated that transport must be operated economically ! and reliably and French has found that its vehicles are operated cheaply and are standing up in service, factors which have played a big part in the company's success story. As business develops, the lines of communication stretch farther and farther from j the Harlow depot, it is essential that an efficient after-sales service is available to support vehicles when they are in operation. Where a long-term contract has been won the transport department sets up a fully operational workshop on the site and makes! immediate contact with the Ford dealer. ' The dealer is advised what vehicles are working from the site and he has a fair idea of what spares should be carried.
These self-contained on-site maintenance units operate where the transport unit exceeds 30 vehicles and are geared to do any job with the exception of an engine change. Where sites are within easy reach of Harlow, one of five mobile servicing teams visit them at regular intervals to carry out routine servicing.
To support the maintenance crews French carries £15,000-worth of spares on consignment, a system which many operators would do well to copy. The stock was supplied originally on credit by the Ford dealers, motor factors and tyre distributors. When a demand is made on the stock a requisition and advice note are produced and the supplier receives one copy which is treated as a re-order. The re-order material is charged monthly and the stock is maintained at a constant level by the supplier. In this way French has on hand a stock of spares without becoming involved in the expense of a £15,000 outlay.
I had heard it said that vehicles from the price bracket into which Fords fall required early replacement. I put the point to Mr. Holt. "We replace our light vans after 60,000 miles or three years, and all others after five years", he said. He reminded me that the time and mileage factors could only be compared with a similar type of operation. The present economic climate is causing French to rethink its replacement policy, however. Labour costs and down time are being carefully calculated and analysed and the result is expected to be a reduction in the expected life of the vehicles.
Mr. Holt who succeeded his father as transport manager at Harlow is a man of the younger school of management. He collects information, sifts and analyses it, then uses the results to pre-plan. Fords are playing a big part in Mr. Holt's plans because, as he puts it, "the vehicles are standing up in service".
He is also planning for the day when plating and testing will be part of a transport manager's life. A brake testing unit is being installed at Harlow and all vehicles will be called into headquarters for cleaning, inspection and repair prior to being submitted for the Ministry test.
I turned the conversation to costs and asked Mr. Holt if he had any detailed information available. He told me that in his type of operation an average cost for each Class of vehicle is .sufficient and he was happy so long as the class average did not rise above an approved standard cost. When the average rose above the standard the matter was investigated and action taken to rectify the cause. As I said earlier, this is a highly competitive business, and costs are not available for competitors' consumption.
Basically this fleet is doing the job it is designed for and obviously doing it economically. There appears to be scope, however, for a manufacturer—Ford perhaps—to produce a dual-purpose vehicle in the lower price bracket specially for civil engineering contractors.
"FIND an experienced own-account operator using Fords on local delivery work who can support his statements with accurate records." That was my second assignment and my thoughts turned immediately to the Scottish Co-operative Wholesale Society which this year celebrates its centenary. Serving 150 retail societies and 4,500 shops in Scotland, this organization is one of the largest in Great Britain. When we added to this the other qualifications, it became apparent that this was an excellent choice.
Every day from the depots in Glasgow, Leith and Dundee the Society's vehicles "fan tailto retail societies, carrying thousands of tons of groceries, hardware and drapery.
The SCWS movement, like the CWS and Konsum of Sweden, found itself recently in an extremely competitive market and economies had to be effected without impairing efficiency. In fact the overall efficiency had to be improved.
When costs are a consideration and efficiency is in question the eyes of the directors always turn towards transport. This may or may not have happened at SCWS, but certainly its transport division has recently been undergoing change under the direction of Mr. L. J. Bereznicki, services division manager.
In its look at the future the Society decided to use Unitainers to speed vehicle turn-round, with York and Hands semitrailers. Attention was then turned to vehicles. The Society's vast experience and its system of records presented a very clear picture of the vehicle best suited for each job. After close examination of all the factors Fords were selected.
This decision was not made as a result of any sales or advertising campaign but from experience, and while the Ford section of the SCWS fleet is relatively speaking not large, it has been chosen for a particular task branch delivery work.
During the past five years the Society has built up a fleet of 70 Fords varying in carrying capacity from 5cwt to 13 tons, and in addition it operates a number of Transit vans on contract hire work. The lessons learned from the operating experience led to Mr. James Ramsay, the senior manager of the transport division, recommending the purchase of a further 43 D-series tractive units. These are now being delivered.
It should be stated here that the SCWS is not standardizing its entire fleet on Ford. Each operation is being examined and it is in the field of retail deliveries by articulated vehicles that Ford has proved particularly suitable.
This type of operation is taxing and while mileages are not excessive, manoeuvrability and speed are essential factors. Each vehicle is expected to deliver 100 tons per week and in so doing cover 700 miles. Neither figure could be looked upon as anything more than normal, but deliveries to retail shops in restricted entries and with limited parking space set their own problems.
The records show that the Fords are economical to operate. Operating costs are: Fuel and lubricant 4.29d; tyres .63d; maintenance 4.62d. The tyre figure seemed remarkably low in view of the potential kerbing hazard on this. kind of work. These figures are the average for the 5-ton to 13-ton vehicles, Mr. Ramsay told me that
he refers regularly to CM's Table of Operating Costs to compare his figures.
It is an accepted fact that operators and engineers in transport have always agreed to differ and it was, therefore, refreshing to find that here the situation was different. The operator felt that this was the tool for the job and his drivers enjoyed the cab comfort. The engineer, too, agreed in the main that the power unit was adequate and the mechanics were loud in their praise for the layout. The general comment was that it was easy to work on.
However, there is always an exception to the rule and one complaint was the difficulty of making handbrake adjustment. Mr. D. Tennant described the mechanism as "a plumber's nightmare". I do not know if this is fair comment; I have not had to work on, it. But from the practical demonstration which followed the criticism I agree it appeared complicated. It was later suggested to me by a technical colleague that perhaps it was the mechanic's method which was wrong.
Among other comments from the workshop staff, one which appeared particularly constructive was that, as when re-fitting a cylinder head the gasket was inclined to slip, studs on the block (on which the gasket could be located) would obviate this. Studs could replace set bolts used by the manufacturers. It was pointed out to me that the manufacturer would have no difficulty as the engine would be vertical during assembly. The engine, when mounted, is inclined and the mechanic's difficulties are easily understood.
If it is a tribute to the Fords that they have proved so mechanically trouble-free, after-sales service did not draw quite the same praise. For the D-series the spares situation is giving no trouble—and anyway SCWS carries 120,000 of parts, mostly for the D. But for Transits and earlier models the picture is not so good and I was told that off-the-road time was sometimes an embarrassment. A small but annoying example while I was at Glasgow depot was a Transit on Contract A work which had been waiting five hours for an exhaust pipe—though the main agent is less than 10 minutes away. I was also told that there was no list of stockists available for Cummins spares.
Notwithstanding this, the SCWS is enjoying a fleet utilization of 85 per cent, which many would envy.
I asked: "What more could Ford do to help the customer?" The engineer, Mr. Tennant, has the most constructive proposal. "We would welcome an on-the-job course for mechanics for D-series," he said. He went on to say that while facilities were available at the factory for training, it was difficult to release all the men for such a course, and too costly.
The SCWS is now taking delivery of a 41-vehicle order made up as follows: 12 D 600 Tractive Units with York Freightmasters.
8 D 600 Tractive Units with York flat semi-trailers.
16 D 700 Tractive Units with York flat semi-trailers.
5 D 300 Tractive Units with Hands semi-trailers and van bodies.
2 D 300 Tractive Units with Hands flat semi-trailers.