DOCK LEVELLERS
Page 50
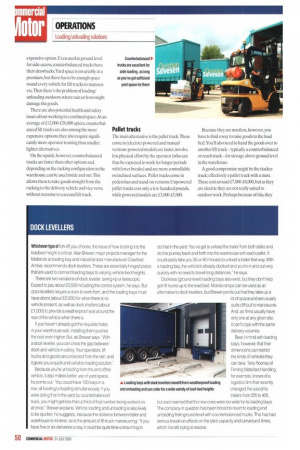
If you've noticed an error in this article please click here to report it so we can fix it.
Whichever type at fork-lift you choose, the issue of how to bring it to the loadbed height is critical. Alan Brewer, major projects manager for the Midlands at loading bay and industrial door manufacturer Crawford Amber, recommends dock levellers. These are essentially hinged plates that are used to connect loading bays to varying vehicle bed heights.
There are two variations of dock leveller: swing-lip or telescopic. Expect to pay about £3,500 including the control system, he says. But dock levellers require a dock to work from, and the loading bays must have doors (about £2,000) for when there is no vehicle present, as well as dock shelters (about 21,000) to provide a weatherproof seal around the fear of the vehicle when there is.
If you haven't already got the requisite holes in your warehouse wall, installing them pushes the cost even higher. But, as Brewer says: With a dock leveller, you can cross the gap between dock and vehicle in safety. Your operators, lift trucks and goods are protected from the rain; and it gives you a quick and variable loading solution."
Because you're unloading from the end of the vehicle, it also makes better use of yard space,
he points out. "You could have 100 Pays in a A Loading bays with du row, all loading/unloading simultaneously. If you and unloading and can c
were doing that in the yard by counterbalanced
truck, you might get less than a third of that number being worked on at once," Brewer explains. Vehicle loading and unloading is also likely to be quicker, he suggests, because the distance between trailer and warehouse is minimal, as is the amount of lift-truck manoeuvring: "If you have five or six deliveries a day, it could be quite time-consuming to do that in the yard. You've got to unload the trailer from both sides and do the journey back and forth into the warehouse with each pallet. It could easily take you 35 or 40 minutes to unload a trailer that way. With a loading bay the vehicle's already docked and you're in and out very quickly with no need to travel long distances," he says.
Dockless (ground-level) loading bays also exist, but they don't help get lift trucks up to the load bed. Mobile ramps can be used as an alternative to dock levellers, but Brewer points out that they take up a lot of space and are usually quite difficult to manoeuvre. And, as firms usually have only one at any given site, it can't cope with the same delivery volumes.
Bear in mind with loading bays, however, that their dimensions can restrict the kinds of vehicles they can take. Tony Rooney of Finning Materials Handling, for example, knows of a
ck levellers benefit from weatherproof loading logistics firm that recently ater for a wide variety of load-bed heights changed the size of its
trailers from 20ft to 40ft, but soon learned that the new ones were too wide for its loading bays. The company in question has been forced to revert to loading and unloading from ground level with counterbalanced trucks. This has had serious knock-on effects on the site's capacity and turnaround times, which it is still trying to resolve.