A TRAILER FOR THE FUTURE
Page 45
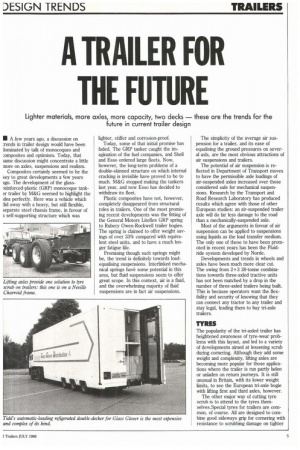
Page 46
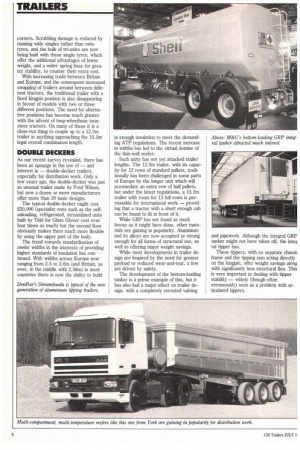
If you've noticed an error in this article please click here to report it so we can fix it.
• A few years ago, a discussion on trends in trailer design would have been dominated by talk of monocoques and zomposites and optimism. Today, that 3ame discussion might concentrate a little more on axles, suspensions and realism.
Composites certainly seemed to be the key to great developments a few years ago. The development of the glassreinforced-plastic (GRP) monocoque tanker trailer by M&G seemed to highlight the .dea perfectly. Here was a vehicle which did away with a heavy, but still flexible, separate steel chassis frame, in favour of a self-supporting structure which was lighter, stiffer and corrosion-proof.
Today, some of that initial promise has faded. The GRP tanker caught the imagination of the fuel companies, and Shell and Esso ordered large fleets. Now however, the long-term problems of a double-skinned structure on which internal cracking is invisible have proved to be to much. M&G stopped making the tankers last year, and now Esso has decided to withdraw its fleet.
Plastic composites have not, however, completely disappeared from structural roles in trailers. One of the most promising recent developments was the fitting of the General Motors Liteflex GRP spring to Rubery Owen-Rockwell trailer bogies. The spring is claimed to offer weight savings of over 33% compared with equivalent steel units, and to have a much longer fatigue life.
Promising though such springs might be, the trend is definitely towards loadequalising suspensions. Interlinked mechanical springs have some potential in this area, but fluid suspensions seem to offer great scope. In this context, air is a fluid, and the overwhelming majority of fluid suspensions are in fact air suspensions. The simplicity of the average air suspension for a trailer, and its ease of equalising the ground pressures on several axis, are the most obvious attractions of air suspensions and trailers.
The potential of air suspension is reflected in Department of Transport moves to have the permissible axle loadings of air-suspended axles increased over those considered safe for mechanical suspensions. Research by the Transport and Road Research Laboratory has produced results which agree with those of other European studies: an air-suspended trailer axle will do far less damage to the road than a mechanically-suspended axle.
Most of the arguments in favour of air suspension can be applied to suspensions using liquids as the load transfer medium. The only one of these to have been promoted in recent years has been the Fluidride system developed by Norde.
Developments and trends in wheels and axles have been much more clear cut. The swing from 2+3 38-tonne combinations towards three-axled tractive units has not been matched by a drop in the number of three-mded trailers being built. This is because operators want the flexibility and security of knowing that they can connect any tractor to any trailer and stay legal, leading them to buy tri-axle trailers.
TYRES
The popularity of the tri-axled trailer has heightened awareness of tyre-wear problems with this layout, and led to a variety of developments aimed at lessening scrub during cornering. Although they add some weight and complexity, lifting axles are becoming more popular for those applications where the trailer is run partly laden or unladen on return journeys. It is still unusual in Britain, with its lower weight limits, to see the European tri-axle bogie with lifting first and third axles, however.
The other major way of cutting tyre scrub is to attend to the tyres themselves. Special tyres for trailers are common, of course. All are designed to combine good sideways grip for cornering with resistance to scrubbing damage on tighter corners. Scrubbing damage is reduced by running wide singles rather than twin tyres, and the bulk of tri-axles are now being built with these single tyres, which offer the additional advantages of lower weight, and a wider spring base for greater stability, to counter their extra cost.
With increasing trade between Britain and Europe, and the consequent increased swapping of trailers around between different tractors, the traditional trailer with a fixed kingpin position is also disappearing in favour of models with two or three different positions. The need for alternative positions has become much greater with the advent of long-wheelbase twinsteer tractors. On many of these it is a close-run thing to couple up to a 12.2m trailer at anything approaching the 15.5m legal overall combination length.
DOUBLE DECKERS
As our recent survey revealed, there has been an upsurge in the use of — and interest in — double-decker trailers, especially for distribution work. Only a few years ago, the double-decker was just an unusual trailer made by Fred Wilson, but now a dozen or more manufacturers offer more than 20 basic designs.
The typical double-decker might cost £20,000 (specialist ones such as the selfunloading, refrigerated, streamlined units built by Tidd for Glass Glover cost over four times as much) but the second floor obviously makes them much more flexible by using the upper part of the body.
The trend towards standardisation of reefer widths in the interests of providing higher standards of insulation has continued. With widths across Europe now ranging from 2.5 to 2.6m (and Britain, as ever, in the middle with 2.58m) in most countries there is now the ability to build in enough insulation to meet the demanding ATP regulations. The recent increase in widths has led to the virtual demise of the thin-wall reefer.
Such unity has not yet attacked trailer lengths. The 12.2m trailer, with its capacity for 12 rows of standard pallets, traditionally has been challenged in some parts of Europe by the longer unit which will accomodate an extra row of half pallets, but under the latest regulations, a 13.2m trailer with room for 13 full rows is permissable for international work — providing that a tractor with a short enough cab can be found to fit in front of it.
While GRP has not found as much favour as it might have done, other materials are gaining in popularity. Aluminium and its alloys are now accepted as strong enough for all forms of structural use, as well as offering major weight savings.
While most developments in trailer design are inspired by the need for greater payload or reduced wear-and-tear, a few are driven by safety.
The development of the bottom-loading tanker is a prime example of this, but it has also had a major effect on trailer design, with a completely rerouted valving and pipework. Although the integral GRP tanker might not have taken off, the intei ral tipper has.
These tippers, with no separate chassi: frame and the tipping ram acting directly on the kingpin, offer weight savings along with significantly less structural Rex. This is very important in dealing with tipper stability — widely (though often erroneously) seen as a problem with articulated tippers.