Aluminium saves costs and increases payload
Page 36
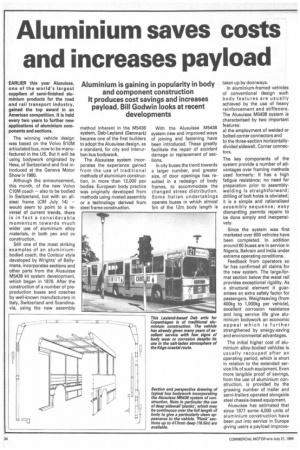
Page 37
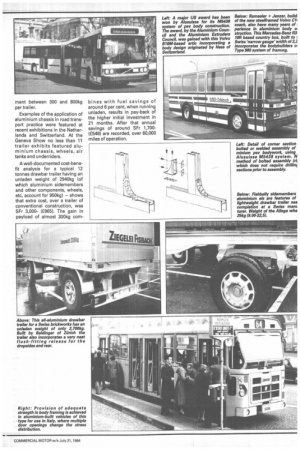
If you've noticed an error in this article please click here to report it so we can fix it.
Aluminium is gaining in popularity in body and component construction It produces cost savings and increases payload. Bill Godwin looks at recent developments
EARLIER this year Alusuisse, one of the world's largest suppliers of semi-finished aluminium products for the road and rail transport industry, gained the top award in an American competition. It is held every two years to further new applications of aluminium components and sections.
The winning vehicle design was based on the Volvo B1OM articulated bus, now to be manufactured in the US. But it will be using bodywork originated by Hess, of Switzerland and first introduced at the Geneva Motor Show in 1980.
Although the announcement, this month, of the new Volvo C1OM coach — also to be bodied in Switzerland, but with an allsteel frame (CM July 14) — would seem to point to a reversal of current trends, there is in fact a considerable momentum towards much wider use of aluminium alloy materials, in both psv and cv construction.
Still one of the most striking examples of an aluminiumbodied coach, the Contour style developed by Wrights' of Ballymena, incorporates sections and other parts from the Alusuisse M5438 kit system development, which began in 1976. After the construction of a number of preproduction buses and coaches by well-known manufacturers in Italy, Switzerland and Scandinavia, using the new assembly
method inherent in the M5438 system, Dab-Leyland (Denmark) became one of the first builders to adopt the Alusuisse design, as a standard, for city and interurban bus bodywork.
The Alusuisse system incorporates the experience gained from the use of traditional methods of aluminium construction, in more than 12,000 psv bodies. European body practice was originally developed from methods using riveted assembly or a technology derived from steel frame construction. With the Alusuisse M5438 system new and improved ways of joining and fastening have been introduced. These greatly facilitate the repair of accident damage or replacement of sections.
In city buses the trend towards a larger number, and greater size, of door openings has resulted in a redesign of body frames, to accommodate the changed stress distribution. Some Italian undertakings operate buses in which almost 5m of the 12m body length is taken up by doorways.
In aluminium-framed vehicles of conventional design such body features are usually achieved by the use of heavy reinforcement and stiffeners. The Alusuisse M5438 system is characterised by two important features: a) the employment of welded or bolted corner connectors and b) the three-section horizontallydivided sidewall. Corner connectors.
The key components of the system provide a number of advantages over framing methods used formerly: It has a high fatigue resistance; no need for preparation prior to assemblywelding is straightforward; drilling of bolt holes is obviated; it is a simple and rationalised assembly sequence; easy dismantling permits repairs to be done simply and inexpensively.
Since the system was first marketed over 600 vehicles have been completed. In addition around 60 buses are in service in Nigeria, Bahrain and India under extreme operating conditions.
Feedback from operators so far has confirmed all claims for the new system. The large-format section below the waist rail provides exceptional rigidity. As a structural element it guarantees an extra safety factor for passengers. Weightsaving (from 400kg to 1,000kg per vehicle), excellent corrosion resistance and long service fife give aluminium bodywork an economic appeal which is further strengthened by energy-saving and environmental advantages.
The initial higher cost of aluminium alloy-bodied vehicles is usually recouped after an operating period, which is short in relation to the extended service life of such equipment. Even more tangible proof of savings, from the use of aluminium construction, is provided by the growing number of trailer and semi-trailers operated alongside steel chassis-based equipment.
Alusuisse has estimated that since 1977 some 4,000 units of aluminium construction have been put into service in Europe giving users a payload improve ment between 300 and 800kg per trailer.
Examples of the application of aluminium chassis in road transport practice were featured at recent exhibitions in the Netherlands and Switzerland. At the Geneva Show no less than 11 trailer exhibits featured aluminium chassis, wheels, air tanks and underriders.
A well-documented cost-benefit analysis for a typical 12 tonnes drawbar trailer having an unladen weight of 2940kg (of which aluminium sidemembers and other components, wheels, etc, account for 950kg) — shows that extra cost, over a trailer of conventional construction, was SFr 3,000(f965). The gain in payload of almost 300kg corn
bines with fuel savings of around 6 per cent, when running unladen, results in pay-back of the higher initial investment in 21 months. After that annual savings of around SFr 1,700(C548) are recorded, over 60,000 miles of operation.