RETREADING THE PATH TO SAFER TYRES
Page 102
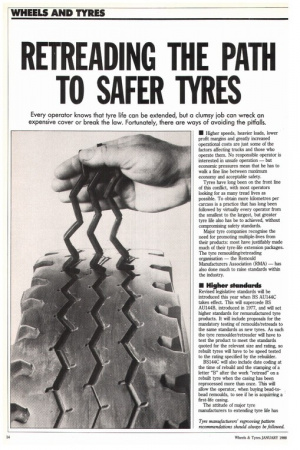
Page 103
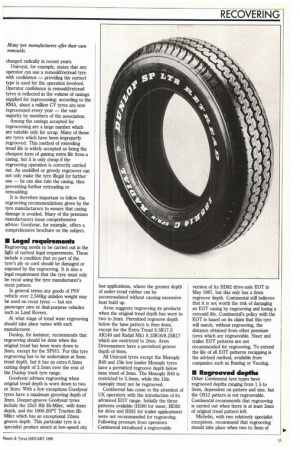
Page 104

If you've noticed an error in this article please click here to report it so we can fix it.
Every operator knows that tyre life can be extended, but a clumsy job can wreck an expensive cover or break the law. Fortunately, there are ways of avoiding the pitfalls.
• Higher speeds, heavier loads, lower profit margins and greatly increased operational costs are just some of the factors affecting trucks and those who operate them. No responsible operator is interested in unsafe operation — but economic pressures mean that he has to walk a fine line between maximum economy and acceptable safety.
Tyres have long been on the front line of this conflict, with most operators looking for as many tread lives as possible. To obtain more kilometres per carcass is a practice that has long been followed by virtually every operator from the smallest to the largest, but greater tyre life also has be to achieved, without compromising safety standards.
Major tyre companies recognise the need for promoting multiple-lives from their products: most have justifiably made much of their tyre-life extension packages. The tyre remoulding/retreading organisation — the Remould Manufacturers Association (RMA) — has also done much to raise standards within the industry.
• Higher standards
Revised legislative standards will be introduced this year when BS AU144C takes effect. This will supercede BS AU144B, introduced in 1977, and will set higher standards for remanufactured tyre products. It will include proposals for the mandatory testing of remoulds/retreads to the same standards as new tyres. As such the tyre remoulder/retreader will have to test the product to meet the standards quoted for the relevant size and rating, so rebuilt tyres will have to be speed tested to the rating specified by the rebuilder.
BS144C will also include date coding at the time of rebuild and the stamping of a letter "B" after the work "retread" on a rebuilt tyre when the casing has been reprocessed more than once. This will allow the operator, when buying bead-tobead remoulds, to see if he is acquirring a first-life casing.
The attitude of major tyre manufacturers to extending tyre life has changed radically in recent years.
Uniroyal, for example, states that any operator can use a remould/retread tyre with confidence — providing the correct type is used for the operation involved. Operator confidence in remould/retread tyres is reflected in the volume of casings supplied for reprocessing:: according to the RMA, about a million CV tyres are now reprocessed every year — the vast majority by members of the association.
Among the casings accepted for reprocessing are a large number which are suitable only for scrap. Many of these are tyres which have been improperly regrooved. This method of extending tread life is widely accepted as being the cheapest form of gaining extra life from a casing, but it is only cheap if the regrooving operation is correctly carried out. An unskilled or greedy regroover can not only make the tyre illegal for further use — he can also ruin the casing, thus preventing further retreading or remoulding.
It is therefore important to follow the regrooving recommendations given by the tyre manufacturers to ensure that casing damage is avoided. Many of the premium manufacturers issue comprehensive advice: Goodyear, for example, offers a comprehensive brochure on the subject.
• Legal requirements
Regrooving needs to be carried out in the light of current legal requirements. These include a condition that no part of the tyre's ply or cord should be damaged or exposed by the regrooving. It is also a legal requirement that the tyre must only be recut using the tyre manufacturer's recut pattern.
In general terms any goods of PSV vehicle over 2,540kg unladen weight may be used on recut tyres — but not passenger cars or dual-purpose vehicles such as Land Rovers.
At what stage of tread wear regrooving should take place varies with each manufacturer.
Dunlop, for instance, recommends that regrooving should be done when the original tread has been worn down to 3mm, except for the SP911. For this tyre regrooving has to be undertaken at 5nun tread depth, but it has an extra 0.5nun cutting depth of 3.5mm over the rest of the Dunlop truck tyre range.
Goodyear advises regrooving when original tread depth is worn down to two or 3mm. With a few exceptions Goodyear tyres have a maximum grooving depth of 3mm. Deeper-groove Goodyear tyres include the 23x5 Rib Hi-Miler, with 4mm depth, and the 1000-20PT Traction HiMiler which has an exceptional 12nun groove depth. This particular tyre is a specialist product aimed at low-speed city bus applications, where the greater depth of under-tread rubber can be accommodated without causing excessive heat build up.
Avon suggests regrooving its products when the original tread depth has worn to two to 3mm. Permitted regroove depth below the base pattern is then 4mm, except for the Extra Tread 8.5R17.5 AR140 and Radial Mkl 8.25R16/8.25R17 which are restricted to 2mm. Avon Drivemasters have a permitted groove depth of 6mm.
All Uniroyal tyres except the Monoply R40 and 15in low loader Monoply tyres have a permitted regroove depth below base tread of 3mm. The Monoply R40 is restricted to 2.5mm, while the 15in monoply must not be regrooved.
Continental has come to the attention of UK operators with the introduction of its advanced EOT range. Initially the three patterns available (HS80 for steer, HD82 for drive and HS81 for trailer applications) were not recommended for regrooving. Following pressure from operators Continental introduced a regroovable version of its HD82 drive-axle EOT in May 1987, but this only has a 2nun regroove depth. Continental still believes that it is not worth the risk of damaging an EOT casing by regrooving and losing a remould life. Continental's policy with the EOT is based on its claim that this tyre will match, without regrooving, the distance obtained from other premium tyres which are regroovable. Steer and trailer EOT patterns are not recommended for regrooving. To extend the life of all EOT patterns recapping is the advised method, available from companies such as Bandag or Vaculug.
• Regreeved depths
Other Continental tyre types have regrooved depths ranging from 1.5 to 5mm, dependent on pattern and size, but the 0S12 pattern is not regroovable. Continental recommends that regrooving is carried out when there is at least 3mm of original tread pattern left.
Michelin, with two relatively specialist exceptions, recommend that regrooving should take place when two to 3mm of original tread depth remains. Michelin XL and XR on/off road tyres are recommended for repatterning before the tread is completely worn away in the central area. Apart from these exceptions Michelin tyres have, dependent on size and model, a regroove depth of between three and 4mm.
A number of tyre manufacturers have tyres in their ranges which require repatterning rather than regrooving. Generally this is restricted to on/off highway tyres with prominent block tread.
Repatterning involves cutting a new pattern into the tread area, without penetrating into the rubber below the tread. The deep ribbed, widely spaced treads of an on/off road tyre require support to prevent excessive tread movement, which in turn leads to rapid wear. This support is generally provided by tie bars or two or more levels in the tread pattern. With this arrangement the tread pattern alters as wear takes place.
With an on/off road tyre such as the Firestone SAT 2000, repatterning only involves grooving-out the tread tie bars. No regrooving into the base rubber is permitted by the manufacturer. With the Firestone ST2000 the original pattern is followed to remove tread tie bars and two level grooves down to the depth of the tyre's shoulder pocket area. Again, no cutting beyond the original, deepest part, of the tread depth is allowed.
Firestone's regrooving recommendations suggest regrooving when two to 3mm of original tread remains.
Pirelli does not recommend any particular remaining tread depth for regrooving. Maximum groove depth below the base of the original pattern runs from anrn for 650R16, 700R16, 700R20 and 9R22.5 sizes. Except for the 3.5mm permitted for the 16R22.5, 15R22.5 and 1200R20 sizes, and the 4rnm of the 315 and 75R24.5, the Pirelli range has a groovable depth of Inm.
• Cutting depths
A further regrooving consideration which has to be allowed for with HM80/80A and L,S91 patterns is the difference in cutting depths for inner and outer tread grooves. With these tyre types care has to be taken as the outer grooves have lmm less grooving depth than the inner grooves.
Manufacturers' regrooving depth recommendations must be treated seriously as there is only around 2mrn base rubber left after grooving, above the breaker belt — and that 2mm is all that is between you and an illegal tyre if you get greedy in cutting. Another factor to consider when regrooving — and all manufacturers stress this — is to accurately measure tread depth at a number of points. The lowest point should be used for setting the cutter depth. This will avoid the risk of taking an untypical high patch on the tread, setting the depth of the regrooving tool accordingly and cutting into the breaker belts.
Assuming that regrooving has been carried out correctly, a further life extension of this type can be achieved at the end of the remoulded or retreaded life. Most manufacturers reduce the grooving depth by lmm for this second operation.
After regrooving the tyre to extend the life of the original tread, if all is well with the casing, remoulding or retreading can be carried out. Many tyre manufacturers now offer their own casing reprocessing packages, following the lead set by Michelin many years ago. Three types of process are available, though according to Uniroyal only two have a significant part of the reprocessed tyre market. These are pre-cured tread recapping and beadto-bead remoulding. The amount of the market taken by the third option, shoulder-to-shoulder, is now insignificant, says Uniroyal.
Traditionally the most popular tyre reprocessing method is bead-to-bead, which now has around 65% of the market. Tyres remoulded in this way look new as the walls are also covered in new rubber, but head-to-bead remoulding is now under pressure from cold-capping processes.
Until recently remoulders could handle the majority of jobs with relatively few moulds, which allowed the companies involved in this type of reprocessing to keep up with tread pattern changes without excessive investment. Recently, however, the dominance of 1000 and 1100 sizes in the UK truck market has diminished as low-profile, wide-single and other sizes have gained favour. Remoulders were faced with a massive investment programme if they were to be able to offer bead-to-bead reprocessing on all these new sizes.
Instead, new capping with pre-cured tread has been introduced. Many established remoulders now offer cold-cap retreading and remoulding on "traditional" sizes. These remould sizes have been complemented by remoulding for the bigvolume "new" sizes such as 15R22.5, where there is sufficient demand to justify investment in new moulds.
Reprocessing the tyre's carcass depends on suitable base material, so responsible tyre reprocessors carefully inspect casings prior to remoulding or retreading. This aspect of tyre reprocessing will be formalised with the introduction of BS AU144C.
• Reprocessed tyres
Goodyear, Michelin, Dunlop and Pirelli are among the many tyre manufacturers to offer reprocessed tyres under their own brand names.
Dunlop has its Truck Tyre Package which Oyes up to five lives: new, regrooved, reprocessed, regrooved and remoulded. Two of these — new and reprocessed — are covered by separate Dunlop guarantees.
Pirelli has recently launched a retread/ remould operation for its premium Zero Degree tyres. Two types of process are used by Pirelli, dependent on tyre type and size: pre-cured recapping, and beadto-bead hot-cure remoulding.
Goodyear, as well as offering a similar "own-brand" reprocessing package, also opts for extended first life as a means of cutting total costs — it claims that its G167 premium drive-axle tyre has up to 22% more depth than standard. This feature has proved to be very popular with operators and now other tyre companies are following suit.
Tyre reprocessors keep very close watch on the casing makes. While all premium-make carcasses are welcomed for reprocessing — assuming their condition is acceptable — some makes are reckoned to be better than other nominally similar quality tyres.
To minimise tyre running costs it is advisable to buy "premium" makes, regroove within manufacturers' recommendations and then remould or retread using a good-quality reprocessor. 0 by Phil Reed