If your ducts are damaged and your fins eroded. . .
Page 40
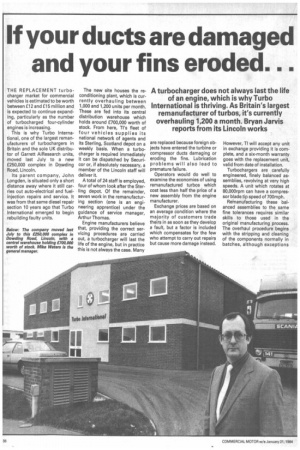
Page 41
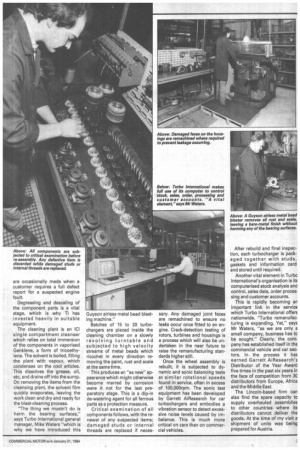
If you've noticed an error in this article please click here to report it so we can fix it.
A turbocharger does not always last the life of an engine, which is why Turbo International is thriving. As Britain's largest remanufacturer of turbos, it's currently overhauling 1,200 a month. Bryan Jarvis reports from its Lincoln works
THE REPLACEMENT turbocharger market for commercial vehicles is estimated to be worth between £12 and £15 million and is expected to continue expanding, particularly as the number of turbocharged four-cylinder engines is increasing.
This is why Turbo International, one of the largest remanufacturers of turbochargers in Britain and the sole UK distributor of Garrett AiResearch units, moved last July to a new £250,000 complex in Dowding Road, Lincoln.
Its parent company, John Longden, is situated only a short distance away where it still carries out auto-electrical and fuelinjection repairs and service. It was from that same diesel repair section 10 years ago that Turbo International emerged to begin rebuilding faulty units. The new site houses the reconditioning plant, which is currently overhauling between 1,000 and 1,200 units per month. These are fed into its central distribution warehouse which holds around £700,000 worth of stock. From here, TI's fleet of four vehicles supplies its national network of agents and its Sterling, Scotland depot on a weekly basis. When a turbocharger is required immediately it can be dispatched by Securicor or, if absolutely necessary, a member of the Lincoln staff will deliver it.
A total of 24 staff is employed, four of whom look after the Sterling depot. Of the remainder, seven work in the remanufacturing section (one is an engineering apprentice) under the guidance of service manager, Arthur Thomas.
Engine manufacturers believe that, providing the correct servicing procedures are carried out, a turbocharger will last the life of the engine, but in practice this is not always the case. Many are replaced because foreign objects have entered the turbine or compressor ducts damaging or eroding the fins. Lubrication problems will also lead to premature failure.
Operators would do well to examine the economies of using remanufactured turbos which cost less than half the price of a new assembly from the engine manufacturer.
Exchange prices are based on an average condition where the majority of customers trade theirs in as soon as they develop a fault, but a factor is included which compensates for the few who attempt to carry out repairs but cause more damage instead. However, TI will accept any unit in exchange providing it is complete, and a six-month warranty goes with the replacement unit, valid from date of installation.
Turbochargers are carefully engineered, finely balanced assemblies, revolving at very high speeds. A unit which rotates at 80,000rpm can have a compressor blade tip speed of 700mph.
Remanufacturing these balanced assemblies to the same fine tolerances requires similar skills to those used in the original manufacturing process. The overhaul procedure begins with the stripping and cleaning of the components normally in batches, although exceptions are occasionally made when a customer requires a full defect report for a suspected engine fault.
Degreasing and descaling of the component parts is a vital stage, which is why TI has invested heavily in suitable equipment.
The cleaning plant is an ClI single compartment cleanser which relies on total immersion of the components in vaporised Genklene, a form of tricoethylane. The solvent is boiled, filling the plant with vapour, which condenses on the cool articles. This dissolves the grease, oil, etc, and drains off into the sump. On removing the items from the cleansing plant, the solvent film quickly evaporates, leaving the work clean and dry and ready for the blast-cleaning process.
"The thing we mustn't do is harm the bearing surfaces," says Turbo International general manager, Mike Waters "which is why we have introduced this Guyson airless metal bead blasting machine."
Batches of 15 to 20 turbochargers are placed inside the cleaning chamber on a slowly revolving turntable and subjected to high velocity streams of metal beads which ricochet in every direction removing the paint, rust and scale at the same time.
This produces an "as new" appearance which might otherwise become marred by corrosion were it not for the last preparatory stage. This is a dip-in de-watering agent for all ferrous parts as a protection measure.
Critical examination of all components follows, with the renewal of any suspected items; damaged studs or internal threads are replaced if neces
sary. Any damaged joint faces are remachined to ensure no leaks occur once fitted to an engine. Crack-detection testing of rotors, turbines and housings is a process which will also be undertaken in the near future to raise the remanufactu ring standards higher still.
Once the wheel assembly is rebuilt, it is subjected to dynamic and sonic balancing tests at similar rotational speeds found in service, often in excess of 100,000rpm. The sonic test equipment has been developed by Garrett AiResearch for car turbochargers and embodies a vibration sensor to detect excessive noise levels caused by imbalance. This is much more critical on cars than on commercial vehicles. After rebuild and final inspection, each turbocharger is packaged together with studs, gaskets and information card and stored until required.
Another vital element in Turbo International's organisation is its computerised stock analysis and control, sales data, order processing and customer accounts.
This is rapidly becoming an important link in the service which Turbo International offers nationwide. "Turbo remanufacturing is expanding. Yet," says Mr Waters, "as we are only a small company, business has to be sought." Clearly, the company has established itself in the commercial vehicle and car sectors. In. the process it has earned Garrett AiResearch's Distributor of the Year Award five times in the past six years in the face of competition from 30 distributors from Europe, Africa and the Middle East.
The Lincoln-based firm can also find the spare capacity to supply overhauled assemblies to other countries where its distributors cannot deliver the goods. At the time of my visit a shipment of units was being prepared for Austria.