All-aluminium Engines Possible
Page 45
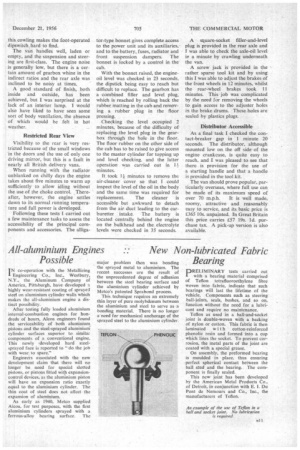
If you've noticed an error in this article please click here to report it so we can fix it.
IN co-operation with the Metallizing i Engineering Co., Inc., Westbury, N.Y., the Aluminum Company of America, Pittsburgh, have developed a highly wear-resistant coating of sprayed steel on aluminium cylinder walls which makes the all-aluminium engine a distinct possibility.
After testing fully loaded aluminium internal-combustion engines for hundreds of hours, Alcoa engineers found the serviceability of both aluminium pistons and the steel-sprayed aluminium cylinder surfaces superior to similar components of a conventional engine. This newly developed hard steelsprayed face is reported to do the job with wear to spare," Engineers associated with the new development claim that there will no longer be need for special slotted pistons, or pistons fitted with expansioncontrol devices, as the aluminium piston will have an expansion ratio exactly equal to the aluminium cylinder. The thin coat of steel does not affect the expansion of aluminium.
As early as 1940. Metco supplied Alcoa, for test purposes, with the first aluminium cylinders sprayed with a ferrous-alloy bearing surface. The major problem then was bonding the sprayed metal to aluminium. The recent successes are the result of the unprecedented degree of adhesion between the steel hearing surface and the aluminium cylinder achieved by Metco's patented Sprabond process.
This technique requires an extremely thin layer of pure molybdenum between the aluminium and steel to serve as a bonding material. There is no longer a'need for mechanical anchorage of the sprayed steel to the aluminium cinder: