WORKSHOP AND GARAGE NOTES.
Page 69
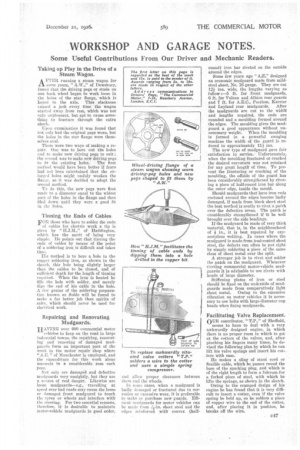
If you've noticed an error in this article please click here to report it so we can fix it.
Some Useful Contributions From Our Driver and Mechanic Readers.
Taking up Play in the Drive of a Steam Wagon.
AFTER running a steam wagon for some years, " A.W.," of Dewsbury, found that the driving pegs or studs on one Imek wheel began to work loose in the holes of the star flange, which is keyed to the axle. This slackness caused a jerk every time the wagon started away from rest, which was not only unpleasant, but apt to cause something to fracture through the extra alwek.
Upon examination it was found that not oulV had the original pegs worn, but the holes in the star flange were themselves oval.
There were two ways of making a repair. One was to bore out the boles and to make new driving pegs to suit ; the second was to make new driving pegs to tit the existing holes. The first method would have been better if fears had not been entertained that the enlarged holm might unduly weaken the flange, so it was decided to adopt the second method.
To do this, the new pegs were first made to a diameter equal to the widest part of the holes in the flange and then filed down Until they were a good fit in the holes.
Tinning the Ends of Cables. FOR those who have to solder the ends
of cables for electric work a tip is given by " H.J.M.," of Haddington, which has the merit of being very simple. He points out that tinning the ends of cables by means of the point of a soldering iron is difficult and takes time.
Eris method is to bore a hole in the copper soldering iron, as shown in the sketch, this hole being slightly larger than the cables to be tinned, and of sufficient depth for length of tinning required. When the iron is heated he fills the hole with solder, and merely dips the end of his cable in the hole. A few grains of the soldering preparation known as Soldo will be found to make a far better job than spirits of Falts, which should never be used for electrical work.
Repairing and Renovating Mudguards.
HAVING over 600 commercial motor vehicles to keep on the road in large industrial towns, the repairing, renovatiug and renewing of damaged mudguards form an important part of the worlc in the motor repair shop where " A.E." of Manchester is employed, and the expenditttro for this work alone amounts to a considerable sum each year.
Not only are damaged and defective mudguards very unsightly, but they are a source of real danger. Likewise are loose mudguards—e.g., travelling at speed over bad roads may cause the loose or damaged front mudguard to touch the tyres or wheels and interfere with the steering: For two essential reasons, therefore, it is desirable to maintain motor-vehicle mudguards in goad order, and allow proper clearance between thorn and the wheels.
In some eases, when a mudguard is badl,v damaged or fractured due to corrosion or excessive-wear, it is preferable to make or purchase new guards. Efficient in u denards for motor vehicles can be made from 116-in. sheet steel and the edges reinforced with convex .(half
round) iron bar riveted on the outside around the edges.
Some few years ago "AE." designed an economic mudguard made from mildsteel sheet, No. 16 gauge. They are cut 121 ins, wide, the lengths varying as follow ;-5 ft. for front mudguards, 6 ft. for Vulcan and Albion rear guards and 7 ft. for LEO., Peerless, Karrier and Leyland rear mudguards. After the mudguards are cut to the width and lengths required, the ends are rounded and a moulding formed around the edges. The moulding gives the mudguard a good appearance without unnecessary weight. When the moulding is formed in a powerful swaging machine the width of the guard is reduced to approximately 111 ins.
The new type of mudguard gave fair satisfaction in service.Unfortunately, when the moulding fractured or cracked the desired curvature was not retained for any great length of time. To prevent the fracturing or cracking of the moulding, the offside of the guard has been considerably strengthened by riveting a piece of half-round iron bar along the outer edge, inside the mould.
Should mudguards that have iron rods enclosed around the edges become badly damaged, if made from black sheet steel the best method is neatly to rivet a patch over the defective areas. The patch is considerably strengthened if it be well brought over the side headings.
If the mudguard be made of very thick material, that is, in the neighbourhood
of in., it is best repaired by oxyacetylene welding. In cases where the mudguard is made from lead-coated sheet steel, the defects can often be put right by simply soldering a piece of the same class of sheet metal over the split.
A stronger job is to rivet and solder the patch on the mudguard. Whenever riveting commercial motor-vehicle mudguards it is advisable to use rivets with heads of large diameter.
Stiffening plates of iron or steel should be fixed on the underside of mudguards made from comparatively light sheet metal. Owing to the excessive vibration on motor vehicles it is necessary to use bolts with large-diameter cup beads when fixing mudguards.
Facilitating Valve Replacement.
OUR contributor, " T.P.," of Sheffield,
seems to have to deal with a very awkwardly designed engine, in which there is no proper room in which to get at the cotters of the valves, and, after pinching his fingers many times, he devised the following plan by which he can lift his valve springs and insert his cotters with ease.
He makes a sling of stout cord or flexible cable, which he passes round the base of the sparking plug, and which is of the right length to form a fulcrum for a forked piece of steel, with which he lifts the springs, as shown in the sketeh.
Owing to the cramped design of his engine he has found that it is very difficult to insert a cotter, even if the valve spring be held up, so he solders a piece of copper wire to the end of the cotter, and, after piecing it in position, he breaks off the wire.