METAL PRESSINGS FOR THE BODY AND CHASSIS.
Page 11
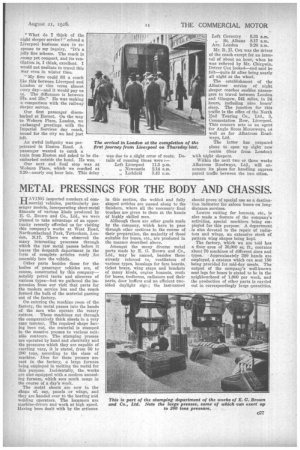
If you've noticed an error in this article please click here to report it so we can fix it.
T_TAVING inspected numbers of com
mercial vehicles, particularly passenger models, incorporating sheet-metal fitments of various kinds produced by E. G. Brown and Co., Ltd., we were pleased to take advantage of an opportunity recently afforded us for visiting this company's works at West Road, Northumberland Park, Tottenham, London, N.17. There we observed the many interesting processes through which the raw metal passes before it leaves the despatch department in the form of complete articles ready for assembly into the vehicle.
Other parts besides those for the bodies of passenger vehicles are, of course, constructed by this company— notably petrol tanks and silencers of various types—but we gathered the impression from our visit that parts for the modern service bus and the coach formed the bulk of the material passing out of the factory.
On entering the machine room of the factory, the metal passes into tho hands of the men who operate the rotary cutters. These machines cut through the comparatively thick sheets in a very easy manner. The required shape having been cut, the material is stamped In the massive presses to various suitable contours. The stamping presses are operated by hand and electricity and the pressures which they are capable of exerting vary, it is stated, from 50 to 200 tons, according to the class of machine. Dies for these presses are cast in the factory, a large furnace being employed in melting the metal for this purpose. Incidentally, the works are also equipped with a modern annealing furnace, which sees much usage in the course of a day's work.
The metal sheets are now in the shape of, say, panels or wings, and they are handed over to the beating and welding operators. The hammers are machine-driven and work at high speed. Having been dealt with by the artisans in this section, the welded and fully shaped articles are passed along to the finishers, where all the necessary final touches are given to them at the hands of highly skilled men.
Although there are other goods made by the company, which have to pass through ether sections in the course of their preparation, the majority of those suitable for buses, etc., are produced in the manner described above.
Amongst the many diverse metal parts made by E. G. Brown and Co., Ltd., may be named, besides those already referred to, ventilators of various types, housings for fare boards, ticket boxes, wing stays and brackets of many kinds, engine bonnets, roofs for buses, toolboxes, radiators and their parts, door buffers and'an efficient twosided daylight sign ; the last-named should prove of special use as a destination indicator for saloon buses on longdistance services.
Louvre cutting for bonnets, etc., is also made a feature of the company's activities, special machines being employed for this purpose. A department As also devoted to the repair of radiators and wings, an extensive stock of pattern wing shapes being kept.
The factory, which we are told has a floor area of 30,000 sq. ft., contains about 70 machines of different sizes and types. Approximately 200 hands are employed, a canteen which can seat 150 being provided for mid-day meals. The output of the company's well-known seat legs for buses is stated to be in the neighbourhood of 1,000 per week, and the production of other parts is carried out in correspondingly large quantities.