IN THE MOD FOR A CHANG
Page 72
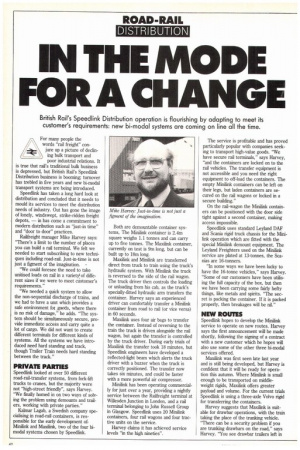
Page 73
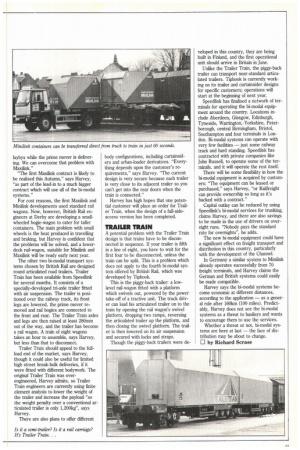
If you've noticed an error in this article please click here to report it so we can fix it.
British Rail's Speedlink Distribution operation is flourishing by adapting to meet its customer's requirements: new bi-modal systems are coming on line all the time.
For many people the words "rail freight" con jure up a picture of declin ing bulk transport and poor industrial relations. It is true that rail's traditional bulk business is depressed, but British Rail's Speedlink Distribution business is booming; turnover has trebled in five years and new bi-modal transport systems are being introduced.
Speedlink has taken a long hard look at distribution and concluded that it needs to mould its services to meet the distribution needs of industry. Out has gone the image of lonely, windswept, strike-ridden freight depots, — in has come a commitment to modern distribution such as "just-in time" and "door to door" practices.
Railfreight manager Mike Harvey says: "There's a limit to the number of places you can build a rail terminal. We felt we needed to start subscribing to new techniques including road-rail. Just-in-time is not just a figment of the imagination. •
"We could foresee the need to take unitised loads on rail in a variety1 of different sizes if we were to meet customer's requirements."
"We needed a quick system to allow the non-sequential discharge of trains, and we had to have a unit which provides a safe environment fot goods, where there is no risk of damage," he adds. "The system should be simultaneously secure, provide immediate access and carry quite a lot of cargo. We did not want to create different terminals for different kinds of systems. All the systems we have introduced need hard standing and track, though Trailer Train needs hard standing between the track."
PRIVATE PARTIES
Speedlink looked at over 50 different road-rail-transfer systems, from fork-lift trucks to cranes, but the majority were not "high-street friendly", says Harvey. "We finally homed in on two ways of solving the problem using demounts and trailers, working with private parties."
Kalmar Lagab, a Swedish company specialising in road-rail containers, is responsible for the early development of. Minilink and Maxilink, two of the four bimodal systems chosen by Speedlink. Both are demountable container systems, The Minilink container is 2.4m square weighs 1.1 tonnes and can carry up to five tonnes. The Maxilink container, currently on test is 9m long, but can be built up to 18m long.
Maxilink and Minilink are transferred direct from truck to train using the truck's hydraulic system. With Minilink the truck is reversed to the side of the rail wagon. The truck driver then controls the loading or unloading from his cab, as the truck's specially-fitted hydraulic arm transfers the container. Harvey says an experienced driver can comfortably transfer a Minilink container from road to rail (or vice versa) in 60 seconds.
Maxilink uses four air bags to transfer the container. Instead of reversing to the train the truck is driven alongside the rail wagon, but again the transfer is controlled by the truck driver. During early trials of Maxilink the transfer took 18 minutes, but Speedlink engineers have developed a reflected-light beam which alerts the truck driver with a buzzer when the truck is correctly positioned. The transfer now takes six minutes, and could be faster with a more powerful air compressor.
Minilink has been operating commercially for just over a year, providing a nightly service between the Railfreight terminal at Willesden Junction in London, and a rail terminal belonging to John Russell Group in Glasgow. Speedlink uses 20 Minilink containers, four rail wagons and four tractive units on the service.
Harvey claims it has achieved service levels "in the high nineties". The service is profitable and has proved particularly popular with companies seeking to transport high-value goods. "We have secure rail terminals," says Harvey, "and the containers are locked on to the rail vehicles. The transfer equipment is not accessible and you need the right equipment to off-load the containers. The empty Minilink containers can be left on their legs, but laden containers are secured on the rail wagons or locked in a secure building."
On the rail-wagon the Minilink containers can be positioned with the door side tight against a second container, making access impossible.
Speedlink uses standard Leyland DAF and Scalia rigid truck chassis for the Minilink operation which are fitted with the special Minilink demount equipment. The Leyland Freighters used on the Minilink service are plated at 13-tonnes, the Scanias are 16-tonners.
"In some ways we have been lucky to have the 16-tonne vehicles," says Harvey. "Some of our customers have been utilising the full capacity of the box, but then we have been carrying some fairly hefty things, like metals and spirits. "The secret is packing the container. If it is packed properly, then breakages will be nil."
NEW ROUTES
Speedlink hopes to develop the Minilink service to operate on new routes. Harvey says the first announcement will be made shortly, following the signing of a contract with a new customer which he hopes will also use some of the other three bi-modal services offered.
Maxilink was first seen late last year and is still being developed, but Harvey is confident that it will be ready for operation this autumn. Where Milani( is small enough to be transported on middleweight rigids, Maxilink offers greater payload and volume. For the current trials Speedlink is using a three-axle Volvo rigid for transferring the containers.
Harvey suggests that Maxilink is suitable for drawbar operations, with the train taking the place of the trunking vehicle. "There can be a security problem if you are truriking drawbars on the road," says Harvey. "You see drawbar trailers left in laybys while the prime mover is delivering. We can overcome that problem with Maxilink."
"The first Maxilink contract is likely to be realised this Autumn," says Harvey, "as part of the lead-in to a much bigger contract which will use all of the bi-modal systems."
For cost reasons, the first Maxilink and Minilink developments used standard rail wagons. Now, however, British Rail engineers at Derby are developing a smallwheeled bogie-wagon to cater for taller containers. The main problem with small wheels is the heat produced in travelling and braking, but Harvey is confident that the problems will be solved, and a lowerdeck rail-wagon, suitable for Minilink and Maxilink will be ready early next year.
The other two bi-modal transport systems chosen by British Rail are designed round articulated road trailers. Trailer Train has been available from Speedlink for several months. It consists of a specially-developed tri-axle trailer fitted with air suspension. The trailer is positioned over the railway track, its front legs are lowered, the prime mover removed and rail bogies are connected to the front and rear. The Trailer Train axles and legs are then raised at least 280nun out of the way, and the trailer has become a rail wagon. A train of eight wagons takes an hour to assemble, says Harvey, but less than that to disconnect.
Trailer Train should appeal to the fullload end of the market, says Harvey, though it could also be useful for limited high street break-bulk deliveries, if it were fitted with different bodywork. The original Trailer Train was overengineered, Harvey admits, so Trailer Train engineers are currently using finite element analysis to lower the weight of the trailer and increase the payload "so the weight penalty over a conventional articulated trailer is only 1,200kg", says Harvey.
There are also plans to offer different body configurations, including curtainsiders and urban-loader derivatives. "Everything depends upon the customer's requirements," says Harvey. "The current design is very secure because each trailer is very close to its adjacent trailer so you can't get into the rear doors when the train is connected."
Harvey has high hopes that one potential customer will place an order for Trailer Train, when the design of a full-sideaccess version has been completed.
TRAILER TRAIN
A potential problem with the Trailer Train design is that trains have to be disconnected in sequence. If your trailer is fifth in a line of eight, you have to wait for the first four to be disconnected, unless the train can be split. This is a problem which does not apply to the fourth bi-modal system offered by British Rail, which was developed by Tiphook.
This is the piggy-back trailer: a lowlevel rail-wagon fitted with a platform which swivels out, powered by the power take-off of a tractive unit. The truck driver can load his articulated trailer on to the train by opening the rail wagon's swivel platform, dropping two ramps, reversing the articulated trailer up the platform, and then closing the swivel platform. The trailer is then lowered on its air suspension and secured with locks and straps.
Though the piggy-back trailers were de veloped in this country, they are being built in Finland, and the first operational unit should arrive in Britain in June.
Unlike the Trailer Train, the piggy-back trailer can transport near-standard articulated trailers. Tiphook is currently working on its trailer and curtainsider designs for specific customers; operations will start at the beginning of next year.
Speedlink has finalised a network of terminals for operating the bi-modal equipment around the country. Locations include Aberdeen, Glasgow, Edinburgh, Tyneside, Warrington, .Yorkshire, Peterborough, central Birmingham, Bristol, Southampton and four terminals in London. Bi-modal systems can operate with very few facilities — just some railway track and hard standing. Speedlink has contracted with private companies like John Russell, to operate some of the terminals, and it will operate the rest itself.
There will be some flexibility in how the bi-modal equipment is acquired by customers: "The equipment can be leased or purchased," says Harvey, "or Railfreight can provide ownership so long as it's backed with a contract."
Capital outlay can be reduced by using Speecllink's bi-modal services for trunking, claims Harvey, and there are also savings to be made in the use of drivers on overnight runs. "Nobody pays the standard rate for overnights", he adds.
The new bi-modal equipment could have a significant effect on freight transport and distribution in this country, particularly with the development of the Chtuinel.
In Germany a similar system to Minilink already operates successfully from 70 freight terminals, and Harvey claims the German and British systems could easily be made compatible.
Harvey says the bi-modal systems become economic at different distances, according to the application — as a general rule after 160Icm (100 miles). Predictably, Harvey does not see the bi-modal systems as a threat to hauliers and wants to encourage them to use the services.
Whether a threat or not, bi-modal systems are here at last — the face of distribution may be about to change. D by Richard Scrase