Great future for an o ame
Page 14
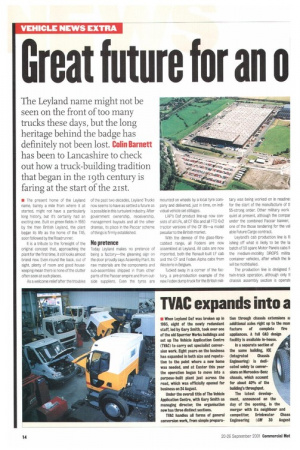
Page 15
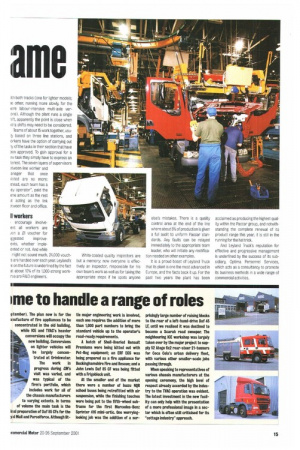
If you've noticed an error in this article please click here to report it so we can fix it.
The Leyland name might not be seen on the front of too many trucks these days, but the long heritage behind the badge has definitely not been lost. Colin Barnett has been to Lancashire to check out how a truck-building tradition that began in the T9th century is faring at the start of the 21st.
• The present home of the Leyland name, barely a mile from where it all started, might not have a particularly long history, but it's certainly had an exciting one. Built on green fields in 1980 by the then British Leyland, the plant began its life as the home of the 145, soon followed by the Roadrunner.
It is a tribute to the foresight of the original concept that, approaching the plant for the first time, it still looks almost brand new. Even round the back, out of sight, plenty of room and good housekeeping mean there is none of the clutter often seen at such places.
As a welcome relief after the troubles of the past two decades, Leyland Trucks now seems to have as settled a future as is possible in this turbulent industry, After government ownership, receivership, management buyouts and all the other dramas, its place in the Paccar scheme of things is firmly established.
No pretence
Today Leyland makes no pretence of being a factory—the gleaming sign on the door proudly says Assembly Plant. Its raw materials are the components and sub-assemblies shipped in from other parts of the Paccar empire and from outside suppliers. Even the tyres are mounted on wheels by a local tyre company and delivered, just in time, on individual vehicle set stillages.
LAP's Oaf product line-up now consists of all LFs, all CF 65s and all FTD 6x2 tractor verslons of the CF 85—a model peculiar to the British market.
With the demise of the glass-fibrecabbed range, all Fodens are now assembled at Leyland. All cabs are now Imported, both the Renault-built LF cab and the CF and Foden Alpha cabs from Westerlo in Belgium.
Tucked away in a corner of the factory, a pre-production example of the new Foden dump truck for the British mili
tary was being worked on in readinel for the start of the manufacture of ti 55-strong order. Other military work quiet at present, although the compar under the combined Paccar banner, one of the those tendering for the val able Future Cargo contract, Leyland's cab production line is ft ishing off what is likely to be the la batch of 50 spare Motor Panels cabs fl the medium-mobility DROPS milita container vehicles, after which the lir will be mothballed.
The production line is designed fi twin-track operation, although only tl chassis assembly section is operati
ith both tracks (one for lighter models; le other, running more slowly, for the lore labour-Intensive multi-axle veroils). Although the plant runs a single lift, apparently the point is close when (t-a shifts may need to be considered. Teams of about 15 work together, usuly based on three line stations, and orkers have the option of carrying out iy of the tasks in their section that have ten approved. To gain approval for a tw task they simply have to express an terest. The seven layers of supervisors ttween line worker and anager that once cisted are no more: stead, each team has a ey operator", paid the tine amount as the rest it acting as the link Aween floor and office.
II workers
encourage involveent all workers are ien a El voucher for
Iggested improveents, whether impleented or not. And while
might not sound much, 24,000 vouch are handed over each year. Leyland's 'eon the future is underlined by the fact at about 10% of its 1,000-strong workroe are R&D engineers. White-coated quality inspectors are but a memory; now everyone is effectively an inspector, responsible for his own team's work as well as for taking the appropriate steps if he spots anyone else's mistakes. There is a quality control area at the end of the line where about 5% of production is giver a full audit to uniform Paccar standards. Any faults can be relayed immediately to the appropriate team leader, who will initiate any rectification needed on other examples.
It is a proud boast of Leyland Truck that its plant is one the most advanced in Europe, and the facts back it up. For the past two years the plant has been acclaimed as producing the highest quality Within the Paccar group, and notwithstanding the complete renewal of its product range this year, it is still in the running for the hat trick.
And Leyland Truck's reputation for effective and progressive management is underlined by the success of its subsidiary, Optima Personnel Services, which acts as a consultancy to promote its business methods in a wide range of commercial activities.