HITCHING LIFTS
Page 170
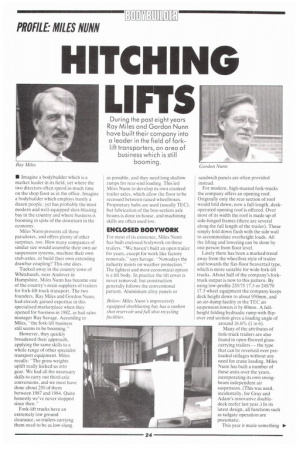
Page 172
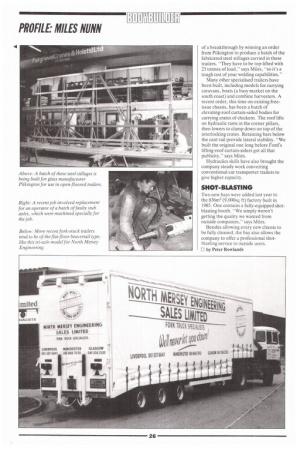
If you've noticed an error in this article please click here to report it so we can fix it.
During the past eight years Ray Miles and Gordon Nunn have built their company into a leader in the field of forklift transporters, an area of business which is still booming.
• Imagine a bodybuilder which is a market leader in its field, yet where the two directors often spend as much time on the shop floor as in the office. Imagine a bodybuilder which employs barely a dozen people, yet has probably the most modern and well-equipped shot-blasting bay in the country and where business is booming in spite of the downturn in the economy.
Miles Nunn presents all these paradoxes, and offers plenty of other surprises. too. How many companies of similar size would assemble their own air suspension systems, machine their own stub-axles, or build their own extending drawbar coupling? This one does.
Tucked away in the country town of Whitchurch, near Andover in Hampshire, Miles Nunn has become one of the country's main suppliers of trailers for fork-lift truck transport. The two founders, Ray Miles and Gordon Nunn. had already gained expertise in this specialised marketplace when they opened for business in 1982, as had sales manager Ray Savage. According to Miles, -the fork-lift business still seems to be booming."
However, they quickly broadened their approach, applying the same skills to a whole range of other specialist transport equipment. Miles recalls: "The gross weights uplift really kicked us into gear. We had all the necessary skills to carry out third-axle conversions, and we must have done about 250 of them between 1987 and 1984. Quite honestly we've never stopped since then."
Fork-lift trucks have an extremely low ground clearance, so trailers carrying them need to be as low-slung
as possible, and they need long shallow ramps for rear-end loading. This led Miles Nunn to develop its own cranked trailer axles, which allow the floor to be recessed between raised wheelboxes. Proprietary hubs are used (usually TEC), but fabrication of the box-section axle beams is done in-house, and machining skills are often used too.
ENCLOSED BODYWORK
For most of its existence, Miles Nunn has built enclosed bodywork on these trailers. "We haven't built an open trailer for years, except for work like factory removals," says Savage. "Nowadays the industry insists on weather protection.The lightest and most economical option is a tilt body. In practice the tilt cover is never removed, but construction generally follows the conventional pattern. Aluminium alloy panels or
sandwich panels are often provided instead.
For modern, high-masted fork-trucks the company offers an opening roof. Originally only the rear section of roof would fold down; now a full-length, deckoperated opening roof is offered. Over most of its width the roof is made up of side-hinged frames (there are several along the full length of the trailer). These simply fold down flush with the side wall to accommodate overheight loads. All the lifting and lowering can be done by one person from floor level.
Lately there has been a marked trend away from the wheelbox style of trailer and towards the flat-floor beavertail type. which is more suitable for wide fork-lift trucks. About half of the company's forktruck output is now to this pattern. By using low-profile 235/75 17.5 or 245/70 17.5 wheel equipment the company keeps deck height down to about 950mm, and an air-dump facility in the TEC air suspension lowers it by 80mm. A fullheight folding hydraulic ramp with flipover end section gives a loading angle of around 16.6% (1 in 6).
Many of the attributes of fork-truck trailers are also found in open-floored glasscarrying trailers — the type that can be reversed over preloaded stillages without any need for crane loading. Miles Nunn has built a number of these units over the years, incorporating its own swingbeam independent air
suspension. (This was used, incidentally, for Gray and Adam's innovative doubledeck reefer last year.) In its latest design, all functions such as tailgate operation are pneumatic.
This year it made something • of a breakthrough by winning an order from Pilkington to produce a batch of the fabricated steel stillages carried in these trailers. "They have to be top-lifted with 23 tonnes of load," says Miles, "so it's a tough test of your welding capabilities."
Many other specialised trailers have been built, including models for carrying caravans, boats (a busy market on the south coast) and combine harvesters. A recent order, this time on existing freeissue chassis, has been a batch of elevating-roof curtain-sided bodies for carrying crates of chickens. The roof lifts on hydraulic rams in the corner pillars, then lowers to clamp down on top of the interlocking crates. Retaining bars below the cant rail provide lateral stability. "We built the original one long before Ford's lifting-roof curtain-siders got all that publicity," says Miles.
Hydraulics skills have also brought the company steady work converting conventional car transporter trailers to give higher capacity.
SHOT-BLASTING
Two new bays were added last year to the 836m2 (9,000sq ft) factory built in 1985. One contains a fully-equipped shotblasting booth. "We simply weren't getting the quality we wanted from outside companies," says Miles.
Besides allowing every new chassis to be fully cleaned, the bay also allows the company to offer a professional shotblasting service to outside users. 0 by Peter Rowlands