PAPWORTH ON THE MOV
Page 158
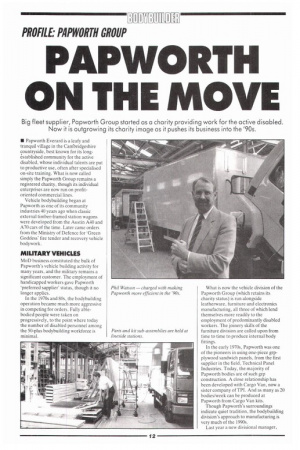
Page 160
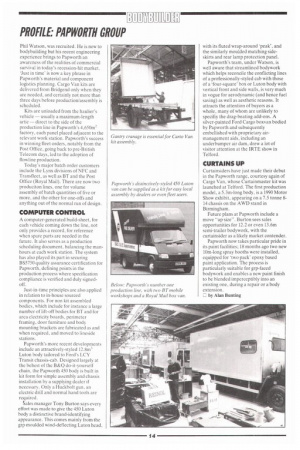
If you've noticed an error in this article please click here to report it so we can fix it.
Big fleet supplier, Papworth Group started as a charity providing work for the active disabled. Now it is outgrowing its charity image as it pushes its business into the `90s.
• Papworth Everard is a leafy and tranquil village in the Cambridgeshire countryside, best known for its longestablished community for the active disabled, whose individual talents are put to productive use, often after specialised on-site training. What is now called simply the Papworth Group remains a registered charity, though its individual enterprises are now run on profitoriented commercial lines.
Vehicle bodybuilding began at Papworth as one of its community industries 40 years ago when classic external timber-framed station wagons were developed from the Austin A40 and A70 cars of the time. Later came orders from the Ministry of Defence for 'Green Goddess' fire tender and recovery vehicle bodywork.
MILITARY VEHICLES
MoD business constituted the bulk of Papworth's vehicle building activity for many years, and the military remains a significant customer, The employment of handicapped workers gave Papworth 'preferred supplier' status, though it no longer applies.
In the 1970s and 80s, the bodybuilding operation became much more aggressive in competing for orders. Fully ablebodied people were taken on progressively, to the point where today the number of disabled personnel among the 50-plus bodybuilding workforce is What is now the vehicle division of the Papworth Group (which retains its charity status) is run alongside leatherware, furniture and electronics manufacturing, all three of which lend themselves more readily to the employment of predominantly disabled workers. The joinery skills of the furniture division are called upon from time to time to produce internal body fittings.
In the early 1970s, Papworth was one of the pioneers in using one-piece grpplywood sandwich panels, from the first supplier in the field, Technical Panel Industries. Today, the majority of Papworth bodies are of such grp construction. A close relationship has been developed with Cargo Van, now a sister company of TI'!. And as many as 20 bodies/week can he produced at Papworth from Cargo Van kits.
Though Papworth's surroundings indicate quiet tradition, the bodybuilding division's approach to manufacturing is very much of the 1990s.
Last year a new divisional manager, Phil Watson, was recruited. He is new to bodybuilding but his recent engineering experience brings to Papworth an awareness of the realities of commercial survival in today's recession-hit market. `Just in time' is now a key phrase in Papworth's material and component logistics planning. Cargo Van kits are delivered from Bridgend only when they are needed, and certainly not more than three days before production/assembly is scheduled.
Kits are unloaded from the haulier's vehicle — usually a maximum-length artic — direct to the side of the production line in Papworth's 4,650m2 factory, each panel placed adjacent to the relevant work station. Papworth's success in winning fleet orders, notably from the Post Office, going back to pre-British Telecom days, led to the adoption of flowline production.
Today's major batch order customers include the Lynx divisions of NFC and Transfleet, as well as BT and the Post Office (Royal Mail). There are now two prod uciton lines, one for volume assembly of batch quantities of five or more, and the other for one-offs and anything out of the normal run of design.
COMPUTER CONTROL
A computer-generated build-sheet, for each vehicle coming down the line, not only provides a record, for reference when spare parts are needed in the future. It also serves as a production scheduling document, balancing the manhours at each work station. The system has also played its part in securing BS5750 quality assurance certification for Papworth, defining points in the production process where specification compliance is verified and duly signedoff.
Just-in-time principles are also applied in relation to in-house sourced components. For non kit assembled bodies, which include for instance a large number of lift-off bodies for BT and for area electricity boards, perimeter framing, door furniture and body mounting brackets are fabricated as and when required, and moved to lineside stations.
Papworth's more recent developments include an attractively-styled 12.8m3 Luton body tailored to Ford's LCY Transit chassis-cab. Designed largely at the behest of the B&Q do-it-yourself chain, the Papworth 450 body is built in kit form for simple assembly and chassis installation by a supplying dealer if necessary. Only a Huckbolt gun. an electric drill and normal hand tools are required.
Sales manager Tony Burton says every effort was made to give the 450 Luton body a distinctive brand-identifying appearance. This comes mainly from the grp moulded wind-deflecting Luton head, with its fluted wrap-around peak', and the similarly moulded matching sideskirts and rear lamp protection panel.
Papworth's team, under Watson, is well aware that streamlined bodywork which helps reconcile the conflicting lines of a professionally-styled cab with those of a 'four-square' box or Luton body with vertical front and side walls, is very much in vogue for aerodynamic (and hence fuel saving) as well as aesthetic reasons. It attracts the attention of buyers as a whole, many of whom are unlikely to specifiy the drag-beating add-ons. A silver-painted Ford Cargo boxvan bodied by Papworth and subsequently embellished with proprietary airmanagement aids, including an underbumper air dam, drew a lot of visitor attention at the IRTE show in Telford.
CURTAINS UP
Curtainsiders have just made their debut in the Papworth range, courtesy again of Cargo Van, whose Curtainmaster kit was launched at Telford. The first production model, a 5.3m-long body, is a 1990 Motor Show exhibit, appearing on a 7.5 tonne 814 chassis on the AWD stand in Birmingham.
Future plans at Papworth include a move "up size". Burton sees sales opportunities for 12.2 or even 13.6m semi-trailer bodywork, with the curtainsider as a likely market contender.
Papworth now takes particular pride in its paint facilities; 18 months ago two new 10m-long spray booths were installed, equipped for two pack' epoxy based paint application. The process is particularly suitable for grp-faced bodywork and enables a new paint finish to be blended imperceptibly into an existing one, during a repair or a body extension.
C by Alan Bunting