TIME FOR A CHANG
Page 49
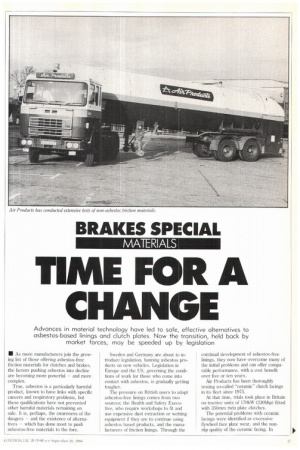
Page 50
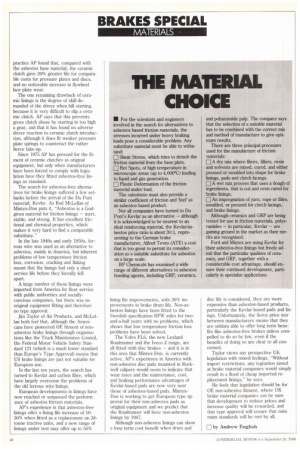
If you've noticed an error in this article please click here to report it so we can fix it.
Advances in material technology have led to safe, effective alternatives to asbestos-based linings and clutch plates. Now the transition, held back by market forces, may be speeded up by legislation
• As more manufacturers join the growing list of those offering asbestos-free friction materials for clutches and brakes, the factors pushing asbestos into decline are becoming more powerful — and more complex.
True, asbestos is a particularly harmful product, known to have links with specific cancers and respiratory problems, but these qualifications have not prevented other harmful materials remaining on sale. It is, perhaps, the awareness of the dangers — and the existence of alternatives — which has done most to push asbestos-free materials to the fore. Sweden and Germany are about to introduce legislation, banning asbestos products on new vehicles. Legislation in Europe and the US, governing the conditions of work for those who come into contact with asbestos, is gradually getting tougher.
The pressure on British users to adopt asbestos-free linings comes from two sources; the Health and Safety Executive, who require workshops to fit and use expensive dust extraction or wetting equipment if they are to continue using asbestos based products, and the manufacturers of friction linings. Through the continual development of asbestos-free linings, they now have overcome many of the initial problems and can offer comparable performance, with a cost benefit over five or ten years.
Air Products has been thoroughly testing so-called "ceramic" clutch facings in its fleet since 1975.
At that time, trials took place in Britain on tractive units of 1701tiN (230bhp) fitted with 350inm twin plate clutches.
The potential problems with ceramic facings were identified as excessive flywheel face plate wear, and the nonslip quality of the ceramic facing. In practice AP found that, compared with the asbestos base material, the ceramic clutch gave 20% greater life for comparable costs for pressure plates and discs, and no noticeable increase in flywheel face plate wear.
The one remaining drawback of ceramic linings is the degree of skill demanded of the driver when hill starting, because it is very difficult to slip a ceramic clutch. AP says that this prevents gross clutch abuse by starting in too high a gear, and that it has found no adverse driver reaction to ceramic clutch introduction, although it does fit weaker pressure plate springs to counteract the rather fierce take-up.
Since 1975 AP has pressed for the fitment of ceramic clutches as original equipment, but only when manufacturers have been forced to comply with legislation have they fitted asbestos-free linings as standard.
The search for asbestos-free alternatives for brake linings suffered a few setbacks before the arrival of the Du Pont material, Kevlar. As Rod McLellan of Mintex-Don puts it, "Asbestos is a Godgiven material for friction linings — inert, stable, and strong. It has excellent frictional and chemical properties, which makes it very hard to find a comparable substitute."
In the late 1940s and early 1950s, ferrous wire was used as an alternative to asbestos, mainly in America, but inherent problems of low temperature friction loss, corrosion, cracking and flaking meant that the linings had only a short service life before they literally fell apart.
A large number of these linings were imported from America for fleet service with public authorities and sociallyconcious companies, but there was no original equipment fitting and therefore no type approval.
Jim Taylor of Air Products, and McLellan both feel that, although the Americans have pioneered OE fitment of nonasbestos brake linings through organisations like the Truck Maintenance Council, the Federal Motor Vehicle Safety Standard 121 (which is a much lower standard than Europe's Type Approval) means that US brake linings are just not suitable for European use.
In the last ten years, the search has turned to Kevlar and carbon fibre, which have largely overcome the problems of the old ferrous wire linings.
European developments in linings have now reached or surpassed the performance of asbestos friction materials.
AP's experience is that asbestos-free linings offer a lining life increase of 1030% when fitted as a replacement on 38tonne tractive units, and a new range of linings under test may offer up to 50% lining life improvements, with 20% improvements in brake drum life. Non-asbestos linings have been fitted to the Swedish specification BPW axles for twoand-a-half years with no problems, which shows that low temperature friction loss problems have been solved.
The Volvo FL6, the new Leyland Roadrunner and the Iveco Z range, are all fitted with disc brakes — and it is in this area that Mintex-Don, is currently active. AP's experience in America with non-asbestos disc pads mounted in Rockwell calipers would seem to indicate that wear rates and the maintenance, cost, and braking performance advantages of Kevlar-based pads are now very near those of asbestos-based pads. MintexDon is working to get European type approval for their non-asbestos pads as original equipment and we predict that the Roadrunner will have non-asbestos linings by 1987.
Although non-asbestos linings can show a long term cost benefit when drum and
disc life is considered, they are more expensive than asbestos-based products, particularly the Kevlar-based pads and linings. Unfortunately, the fierce price war between manufacturers means that they are seldom able to offer long term benefits like asbestos-free brakes unless compelled to do so by law, even if the benefits of doing so are clear to all concerned.
Taylor views any prospective UK legislation with mixed feelings. "Without import restrictions, any legisation aimed at brake material companies would simply result in a flood of cheap imported replacement linings," he says.
He feels that legislation should be for OE non-asbestos fitment, where UK brake material companies can be sure that development to reduce prices and increase quality will be rewarded, and that type approval will ensure that minimum standards will be met by all.
by Andrew English