THE MATERIAL CHOICE
Page 50
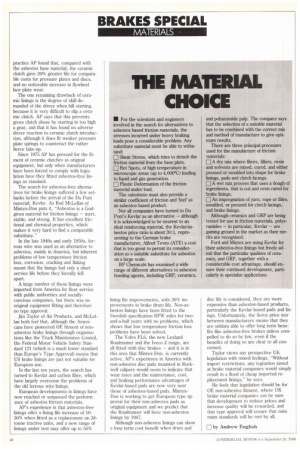
If you've noticed an error in this article please click here to report it so we can fix it.
• For the scientists and engineers involved in the search for alternatives to asbestos based friction materials, the stresses incurred under heavy braking loads pose a considerable problem. Any substitute material must be able to withstand: Shear Stress, which tries to detach the friction material from the base plate.
Hot Spots, of high temperature in microscopic areas (up to 4,000°C) leading to liquid and gas generation.
Plastic Deformation of the friction material under load.
The substitute must also provide a similar coefficient of friction and 'feel' as an asbestos based product.
Not all companies have turned to Du Pont's Kevlar as an alternative — although it is acknowledged to be nearest to an ideal reinforcing material, the Kevlar/asbestos price ratio is about 30:1, representing to the German brake manufacturer, Alfred Teves (ATE) a cost that is too great to permit its consideration as a suitable substitute for asbestos on a large scale.
BP Chemicals has examined a wide range of different alternatives to asbestos bonding agents, including GRP, ceramics, and polyararoide pulp. The company says that the selection of a suitable material has to be combined with the correct mix and method of manufacture to give optimum results.
There are three principal processes used for the manufacture of friction materials:
fl A dry mix where fibres, fillers, resin and solvents are mixed, cured, and either pressed or moulded into shape for brake linings, pads and clutch facings.
[]A wet mix process that uses a dough of ingredients, that is out and oven cured for brake linings.
An impregnation of yarn, rope or fibre, moulded, or pressed for clutch facings, and brake linings.
Although ceramics and GRP are being tested for use in friction materials, polyaramides — in particular, Kevlar — are gaining ground in the market as their merits are recognised.
Ford and Mintex are using Kevlar for 'their asbestos-free linings but freely admit that the particular qualities of ceramics, and GRP, together with a considerable cost advantage, should ensure their continued development, particularly in specialist applications.