(..) TECHNICAL DEVELOPMENT AND MAINTENANCE
Page 216
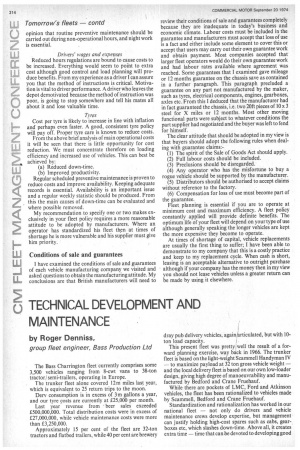
Page 217
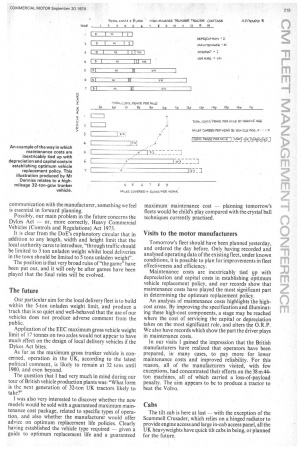
Page 218
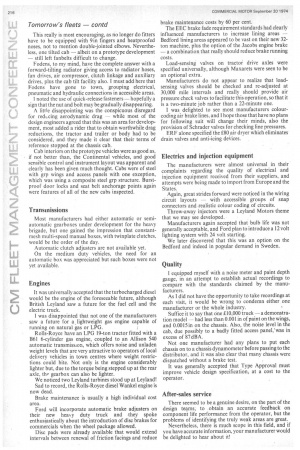
Page 219
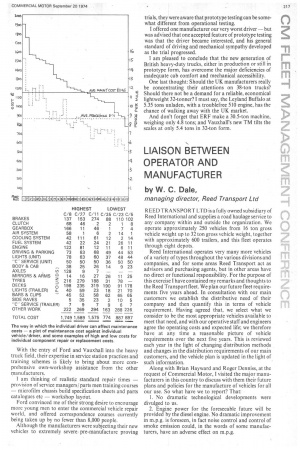
If you've noticed an error in this article please click here to report it so we can fix it.
by Roger Denniss,
group fleet engineer, Bass Production Ltd
The Bass Charrington fleet currently comprises some 3,500 vehicles ranging from 8-cwt vans to 38-ton tractor/semi-trailers, operating in Europe.
The trunker fleet alone covered 12 m miles last year, which is equivalent to 25 return trips to the moon.
Dery consumption is in excess of 3m gallons a year, and our tyre costs are currently at £25,000 per month.
Last year revenue from beer sales exceeded £500,000,000. Total distribution costs were in excess of £27,000,000, while vehicle maintenance costs were more than £3,250,000.
Approximately 15 per cent of the fleet are 32-ton tractors and flatbed trailers, while 40 per cent are brewery dray pub delivery vehicles, again*rticulated, but with 10 ton load capacity. • This present fleet was pretty well the result of a forward planning exercise, way back in 1966. The trunker fleet is based on the light-weight Scammell Handyman IV — to maximize payload at 32 ton gross vehicle weight — and the local delivery fleet is based on our own low-loader design, giving high degree of manoeuvrability and manufactured by Bedford and Crane Fruehauf.
While there are pockets of LMC, Ford and Atkinson vehicles, the fleet has been rationalized to vehicles made by Scammell, Bedford and Crane Fruehauf.
Standardization and rationalization has worked in our national fleet — not only do drivers and vehicle maintenance crews develop expertise, but management can justify holding high-cost spares such as cabs, gearboxes etc, which slashes down-time. Above all, it creates extra time — time that can be devoted to developing good communication with the manufacturer, something we feel is essential in forward planning.
Possibly, our main problem in the future concerns the Dykes Act — or, more correctly, Heavy Commercial Vehicles (Controls and Regulations) Act 1973.
It is clear from the DoE's explanatory circular that in addition to any length, width and height limit that the local authority cares to introduce, "through traffic should be limited to 3 ton unladen weight whilst local deliveries in the town should be limited to 5 tons unladen weight".
The position is that very broad rules of "the game" have been put out, and it will only be after games have been played that the final rules will be evolved.
The future
Our particular aim for the local delivery fleet is to build within the 5-ton unladen weight limit, and produce a 'truck that is so quiet and well-behaved that the use of our vehicles does not produce adverse comment from the public.
Application of the EEC maximum gross vehicle weight limit of 17 tonnes on two axles would not appear to have much effect on the design of local delivery vehicles if the Dykes Act bites.
As far as the maximum gross trunker vehicle is concerned, operation in the UK, according to the latest political comment, is likely to remain at 32 tons until 1980, and even beyond.
The question that I had very much in mind during our tour of British vehicle production plants was: "What form is the next generation of 32-ton UK tractors likely to take?"
I was also very interested to discover whether the new models would be sold with a guaranteed maximum maintenance cost package, related to specific types of operation, and also whether the manufacturer would offer advice on optimum replacement life policies. Clearly having established the vehicle type required — given a guide to optimum replacement life and a guaranteed maximum maintenance cost — planning tomorrow's fleets would be child's play compared with the crystal ball techniques currently practised.
Visits to the motor manufacturers
Tomorrow's fleet should have been planned yesterday, and ordered the day before. Only having recorded and analysed operating data of the existing fleet, under known conditions, it is possible to plan for improvements in fleet effectiveness and efficiency.
Maintenance costs are inextricably tied t.tp with depreciation and capital costs in establishing optimum vehicle replacement policy, and our records show that maintenance costs have played the most significant part in determining the optimum replacement policy.
An analysis of maintenance costs highlights the highcost areas. By improving the specification and illuminating these high-cost components, a stage may be reached where the cost of servicing the capital or depreciation takes on the most significant role, and alters the O.R.P. We also have records which show the part the driver plays in maintenance costs.
In our visits I gained the impression that the British manufacturers have realized that operators have been prepared, inmany cases, to pay more for lower maintenance costs and improved reliability. For this reason, all of the manufacturers visited, with few exceptions, had concentrated their efforts on the 38 m 44ton machines, all of which carried a loss-of-payload penalty. The aim appears to be to produce a tractor to beat the Volvo.
Cabs
The tilt cab is here at last — with the exception of the Scam mell Crusader, which relies on a hinged radiator to provide engine access and large in-cab access panel, all the UK heavyweights have quick tilt cabs in being, or planned for the future. This really is most encouraging, as no longer do fitters have to be equipped with 9 in fingers and heatproofed noses, not to mention double-jointed elbows. Nevertheless, one tilted cab — albeit on a prototype development — still left fanbelts difficult to change.
Fodens, to my mind, have the complete answer with a forward-tilting radiator giving access to radiator hoses, fan drives, air compressor, clutch linkage and auxiliary drives, plus the cab tilt facility also. I must add here that Fodens have gone to town, grouping electrical, pneumatic and hydraulic connections in accessible areas.
I noted the use of quick-release fasteners — hopefully a sign that the nut and bolt may be gradually disappearing.
A little disappointing was the conspicuous disregard for reducing aerodynamic drag — while most of the design engineers agreed that this was an area for development, most added a rider that to obtain worthwhile drag reductions, the tractor and trailer or body had to be considered, and they made it clear that their terms of reference stopped at the chassis cab.
Cab interiors on the prototype vehicles were as good as, if not better than, the Continental vehicles, and good sensible control and instrument layout was apparent and clearly has been given much thought. Cabs were of steel with grp wings and access panels with one exception, which was using a composite steel grp structure. Burstproof door locks and seat belt anchorage points again were features of all of the new cabs inspected.
TranstnissionS Most manufacturers had either automatic or semiautomatic gearboxes under development for the heavy brigade, but one gained the impression that constantmesh multi-speed manual boxes, with twinplate clutches, would be the order of the day.
Automatic clutch adjusters are not available yet.
On the medium duty vehicles, the need for an automatic box was appreciated but such boxes were not yet available.
Engines
It was universally accepted that the turbocharged diesel would be the engine of the foreseeable future, although British Leyland saw a future for the fuel cell and the electric truck.
I was disappointed that not one of the manufacturers saw a future for a_ lightweight gas engine capable of running on natural gas or LPG.
Rolls-Royce have an LPG 19-ton tractor fitted with a B61 6-cylinder gas engine, coupled to an Allison 540 automatic transmission, which offers noise and unladen weight levels that are very attractive to operators of local delivery vehicles in town centres where weight restrictions could bite. Not only is the engine considerably lighter but, due to the torque being stepped up at the rear axle, the gearbox can also be lighter.
We noticed two Leyland turbines stood up at Leyland! Sad to record, the Rolls-Royce diesel Wankel engine is now dead.
Brake maintenance is usually a high individual cost area.
Ford will incorporate automatic brake adjusters on their new heavy duty truck and they spoke enthusiastically about the introduction of disc brakes for commercials when the wheel package allowed.
Disc pads were already available that would extend intervals between renewal of friction facings and reduce brake maintenance costs by 60 per cent.
The EEC brake fade requirement standards had clearly influenced manufacturers to increase lining areas Bedford lining areas appeared to be vast on their new 32ton machine, plus the option of the Jacobs engine brake — a combination that really should reduce brake running costs.
Load-sensing valves on tractor drive axles were specified universally, although Maxarets were seen to be an optional extra.
Manufacturers do not appear to realize that loadsensing valves should be checked and re-adjusted at 30,000 mile intervals and really should provide air pressure check valves to facilitate this operation, so that it is a two-minute job rather than a 22-minute one.
I was delighted to see most manufacturers colourcoding air brake lines, and 1 hope those that have no plans for following suit will change their minds, also the provision of Schrader valves for checking line pressures.
E R F alone specified the E80,air dryer which eliminates drain valves and anti-icing devices.
Electrics and injection equipment
The manufacturers were almost universal in their complaints regarding the quality of electrical and injection equipment received from their suppliers, and attempts were being made to import from Europe and the States.
Again, great strides forward were noticed in the wiring circuit layouts — with accessible groups of snap connectors and -realistic colour coding of circuits.
Throw-away injectors were a Leyland Motors theme that we may see developed.
Manufacturers again accepted that bulb life was not generally acceptable, and Ford plan to introduce a 12 volt lighting system with 24 volt starting.
We later discovered that this was an option on the Bedford and indeed in popular demand in Sweden.
Quality
I equipped myself with a noise meter and paint depth gauge, in an attempt to establish actual recordings to compare with the standards claimed by the manufacturers.
As I did not have the opportunity to take recordings at each visit, it would be wrong to condemn either one manufacturer or the whole industry.
Suffice it to say that one £10,000 truck — a demonstra tion model had less than 0.001 in of paint on the wings, and 0.0015 in on the chassis. Also, the noise level in the cab, due possibly to a badly fitted access panel, was in excess of 87 d BA.
Not one manufacturer had any plans to put each chassis on to a chassis dynamometer before passing to the distributor, and it was also clear that many chassis were dispatched without a brake test.
It was generally accepted that Type Approval must improve vehicle design specification, at a cost to the operator.
After-sales service
There seemed to be a genuine desire, on the part of the design teams, to obtain an accurate feedback on component life performance from the operator, but the problems of identifying the truly weak areas are great.
Nevertheless, there is much scope in this field, and if you have accurate information, your manufacturer would be delighted to hear about it!
The way in which the individual driver can affect maintenance costs — a plot of maintenance cost against individual vehicle/driver, and some examples of high and low costs for individual component repair or replacement costs.
With the entry of Ford and Vauxhall into the heavy truck field, their expertise in service station practices and training schemes is likely to bring about more comprehensive own-workshop assistance from the other manufacturers.
1 am thinking of realistic standard repair times — provision of service managers/ parts men training courses — microfilm chassis build specification sheets and parts catalogues etc — workshop laydut.
Ford convinced me of their strong desire to encourage more young men to enter the commercial vehicle repair world, and offered correspondence courses currently being taken up by no fewer than 8,000 people.
Although the manufacturers were subjecting their new vehicles to extremely severe pre-manufacture proving trials, they were aware that prototype testing can be somewhat different from operational testing.
I offered one manufacturer our very worst driver — but was advised that one accepted feature of prototype testing was that the driver became interested, and his general standard of driving and mechanical sympathy developed as the trial progressed.
I am pleased to conclude that the new generation of British heavy-duty trucks, either in production or still in prototype form, has overcome the major deficiencies of inadequate cab comfort and mechanical accessibility.
One last thought: Should the UK manufacturers really be concentrating their attentions on 38-ton trucks? Should there not be a demand for a reliable, economical lightweight 32-tonner? I must say, the Leyland Buffalo at 5.35 tons unladen, with a troublefree 510 engine, has the chance of walking away with the UK market.
And don't forget that ERE make a 30.5-ton machine, weighing only 4.8 tons; and Vauxhall's new TM tilts the scales at only 5.4 tons in 32-ton form.