Tomorrow's fleets
Page 214
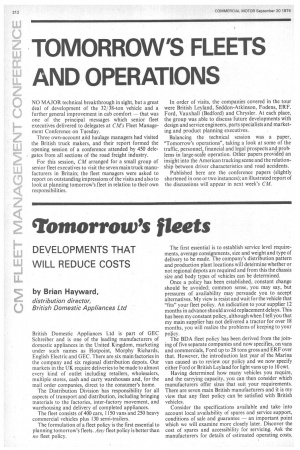
Page 215
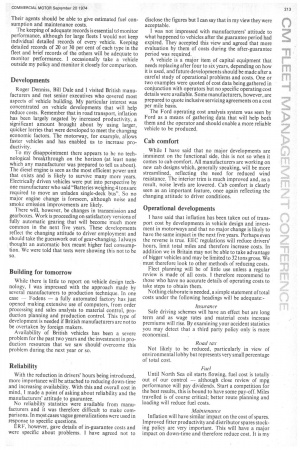
Page 216
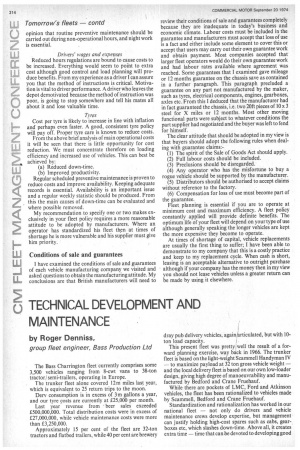
If you've noticed an error in this article please click here to report it so we can fix it.
DEVELOPMENTS THAT WILL REDUCE COSTS
by Brian Hayward,
distribution director, British Domestic Appliances Ltd
British Domestic Appliances Ltd is part of GEC Schreiber and is one of the leading manufacturers of domestic appliances in the United Kingdom, marketing under such names as Hotpoint, Morphy Richards, English Electric and GEC. There are six main factories in the company and six regional distribution depots. Our markets in the UK require deliveries to be made to almost every kind of outlet including retailers, wholesalers, multiple stores, cash and carry warehouses and, for the mail order companies, direct to the consumer's home.
The Distribution Division has responsibility for all aspects of transport and distribution, including bringing materials to the factories, inter-factory movement, and warehousing and delivery of completed appliances.
The fleet consists of 400 cars, 1150 vans and 250 heavy commercial vehicles plus 130 semi-trailers.
The formulation of a fleet policy is the first essential to planning tomorrow's fleets. Any fleet policy is better than no fleet policy. The first essential is to establish service level requirements, average consignments, size and weight and type of delivery to be made. The company's distribution pattern and production plant locations will determine whether or not regional depots are required and from this the chassis size and body types of vehicles can be determined.
Once a policy has been established, constant change should be avoided; common sense, you may say, but pressures of availability may persuade you to accept alternatives. My view is resist and wait for the vehicle that "fits" your fleet policy. An indication to your supplier 12 months in advance should avoid replacement delays. This has been my constant policy, although when I tell you that my main supplier has not delivered a tractor for over 18 months, you will realize the problems of keeping to your policy. The BDA fleet policy has been derived from the joining of five separate companies and now specifies, on vans and commercials, Ford up to 28 tons gross and ERF over that. However, the introduction last year of the Marina van caused us to review our policy and we now specify either Ford or British Leyland for light vans up to 10 cwt.
Having determined how many vehicles you require, and the carrying capacity, you can then consider which manufacturers offer sizes that suit your requirements. There are seven main British manufacturers and it is my view that any fleet policy can be satisfied with British vehicles.
Consider the specifications available and take into account local availability of spares and service support, conditions of sale and guarantee — an important point which we will examine more closely later. Discover the cost of spares and accessibility for servicing. Ask the manufacturers for details of estimated operating costs. Their agents should be able to give estimated fuel consumption and maintenance costs.
The keeping of adequate records is essential td monitor performance, although for large fleets I would not keep individual detailed records of every vehicle. Keeping detailed records of 20 or 30 per cent of each type in the fleet and brief records of the others will be adequate to monitor performance. I occasionally take a vehicle outside my policy and monitor it closely for comparison.
Developments
Roger Denniss, Bill Dale and I visited British manufacturers and met senior executives who covered most aspects of vehicle building. My particular interest was concentrated on vehicle developments that will help reduce costs. Remember that in road transport, inflation has been largely negated by increased productivity, a significant amount brought about by using larger, quicker lorries that were developed to meet the changing economic factors. The motorway, for example, allows faster vehicles and has enabled us to increase productivity.
To my disappointment there appears to be no technological breakthrough on the horizon (at least none which any manufacturer was prepared to tell us about). The diesel engine is seen as the most efficient power unit that exists and is likely to survive many more years. Electrically driven vehicles were put into perspective by one manufacturer who said "Batteries weighing 4 tons are required to move an unladen single-deck bus". So no major engine change is foreseen, although noise and smoke emission improvements are likely.
There will, however, be changes in transmission and gearboxes. Work is proceeding on satisfactory versions of fully automatic gearing that will become much more common in the next five years. These developments reflect the changing attitude to driver employment and should take the guesswork out of gear-changing. I always thought an automatic box meant higher fuel consumption. We were told that tests were showing this not to be so.
Building for tomorrow
While there is little to report on vehicle design technology, I was impressed with the approach made by several manufacturers to production technique. In one case — Fodens — a fully automated factory has just opened making extensive use of computers, from order processing and sales analysis to material control, production planning and production control. This type of development is needed if British manufacturers are not to be overtaken by foreign makers.
Availability of British vehicles has been a severe problem for the past two years and the investment in production resources that we saw should overcome this problem during the next year or so.
Reliability
With the reduction in drivers' hours being introduced, more importance will be attached to reducing down-time and increasing availability. With this and overall cost in mind, I made a point of asking about reliability and the manufacturers' attitude to guarantee. No reliability statistics were available from manufacturers and it was therefore difficult to make comparisons. In most.cases vague generalizations were used in response to specific questions.
ERF, however, gave details of in-guarantee costs and were specific about problems. I have agreed not to disclose the figures but I can say that in my view they were acceptable.
I was not impressed with manufacturers' attitude to what happened to vehicles after the guarantee period had expired. They accepted this view and agreed that more evaluation by them of costs during the after-guarantee period was required.
A vehicle is a major item of capital equipment that needs replacing after four to six years, depending on how it is used, and future developments should be made after a careful study of operational problems and costs. One or two examples were quoted of cost data being gathered in conjunction with operators but no specific operating cost details were available. Some manufacturers, however, are prepared to quote inclusive servicing agreements on a cost per mile basis.
The Ford operating cost analysis system was seen by Ford as a means of gathering data that will help both them and the operator and should enable a more reliable vehicle to be produced.
Cab comfort
While I have said that no major developments are imminent on the functional side, this is not so when it comes to cab comfort. All manufacturers are working on new cab designs which, generally speaking, will be more streamlined, reflecting the need for reduced wind resistance. The interior trim is much improved and, as a result, noise levels are lowered. Cab comfort is clearly seen as an important feature, once again reflecting the changing attitude to driver conditions.
Operational developments
I have said that inflation has been taken out of transport cost by developments in vehicle design and investment in motorways and that no major change is likely to have the same impact in the next five years. Perhaps even the reverse is true. EEC regulations will reduce drivers' hours, limit total miles and therefore increase costs. In addition we in Britain may not be able to take advantage of bigger vehicles and may be limited to 32 tons gross. We must therefore look to other methods of reducing costs.
Fleet planning will be of little use unless a regular review is made of all costs. I therefore recommend to those who have no accurate details of operating costs to take steps to obtain them.
Nothing elaborate is needed, a simple statement of total costs under the following headings will be adequate: insurance Safe driving schemes will have an effect but are long term and as wage rates and material costs increase premiums will rise. By examining your accident statistics you may detect that a third party policy only is more economical. . Road tax Not likely to be reduced, particularly in view of environmental lobby but represents very small percentage of total cost.
Fuel Until North Sea oil starts flowing, fuel cost is totally out of our control -although close review of mpg performance will pay dividends. Start a competition for the best results, this is bound to have some pay-off. Miles travelled is of course critical; better route planning and loading will reduce fuel costs.
Maintenance Inflation will have similar impact on the cost of spares. Improved fitter productivity and distributor spares stocking policy are very important. This will have a major impact on down-time and therefore reduce cost. It is my opinion that routine preventive maintenance should be carried out during non-operational hours, and night work is essential.
Drivers' wages and expenses
Reduced hours regulations are bound to cause costs to be increased. Everything would seem to point to extra cost although good control and load planning will produce benefits. From my experience as a driver! can assure you that the method of instructions is critical. Motivation is vital to driver performance. A driver who leaves the depot demotivated because the method of instruction was poor, is going to stop somewhere and tell his mates all about it and lose valuable time.
Tyres Cost per tyre is likely to increase in line with inflation and perhaps even faster. A good, consistent tyre policy will pay off. Proper tyre care is known to reduce costs.
From the above brief analysis of main operational costs it will be seen that there is little opportunity for cost reduction. We must concentrate therefore on loading efficiency and increased use of vehicles. This can best be achieved by: (a) Reduced down-time.
(b) Improved productivity.
Regular scheduled preventive maintenance is proven to reduce costs and improve availability. Keeping adequate records is essential. Availability is an important issue and a regular weekly statistic should be produced. From this the main causes of down-time can be evaluated and where possible removed.
My recommendation to specify one or two makes exclusively in your fleet policy requires a more reasonable attitude to be adopted by manufacturers. Where an operator has standardized his fleet then at times of shortage he is more vulnerable and his supplier must give him priority.
Conditions of sale and guarantees
I have examined the conditions of sale and guarantees of each vehicle manufacturing company we visited and asked questions to obtain the manufacturing attitude. My conclusions are that British manufacturers will need to review their conditions of sale and guarantees completely because they are inadequate in today's business and economic climate. Labour costs must be included in the guarantee and manufacturers must accept that loss of use is a fact and either include some element to cover this or accept that users may carry out their own guarantee work and obtain payment. Most companies accepted that larger fleet operators would do their own guarantee work and had labour rates available where agreement was reached. Some guarantees that I examined gave mileage or 12 months guarantee on the chassis save as contained in a further paragraph. This paragraph precluded a guarantee on any part not manufactured by the maker, such as tyres, electrical components, engines, gearboxes, axles etc. From this I deduced that the manufacturer had in fact guaranteed the chassis, i.e. two 20ft pieces of 10 x 3 steel for X miles or 12 months. Most other moving functional parts were subject to whatever conditions the part supplier had negotiated and the buyer was left to fend for himself.
The clear attitude that should be adopted in my view is that buyers should adopt the following rules when dealing with guarantee claims: (I) The spirit of the Sale of Goods Act should apply.
(2) Full labour costs should be included.
(3) Preclusions should be disregarded.
(4) Any operator who has the misfortune to buy a rogue vehicle should be supported by the manufacturer.
(5) Distributors should be authorised to accept claims without reference to the factory.
(6) Compensation for loss of use must become part of the guarantee.
Fleet planning is essential if you are to operate at minimum cost and maximum efficiency. A fleet policy constantly applied will provide definite benefits. The optimum life of your fleet will depend on your type of use although generally speaking the longer vehicles are kept the more expensive they become to operate.
At times of shortage of capital, vehicle replacements are usually the first thing to suffer; I have been able to demonstrate to my company that this is a costly practice and keep to my replacement cycle. When cash is short, leasing is an acceptable alternative to outright purchase although if your company has the money then in my view you should not lease vehicles unless a greater return can be made by using it elsewhere.