GT LEYLAND FOR 1970
Page 101
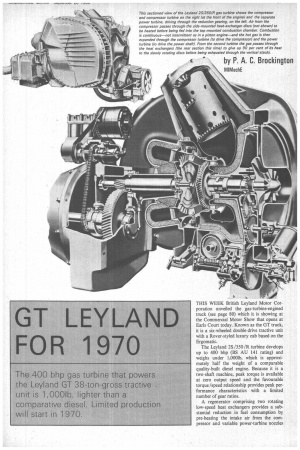
Page 102
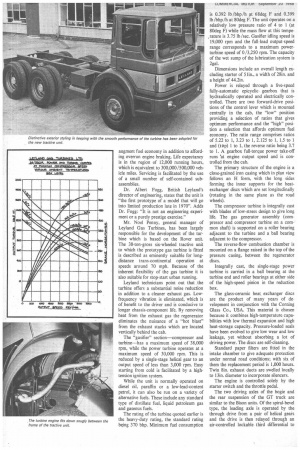
Page 103
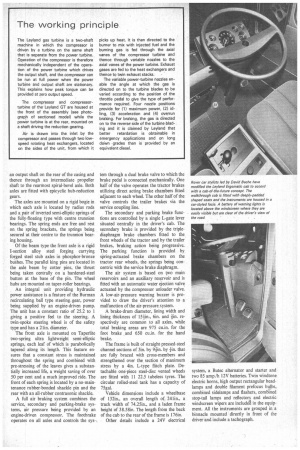
If you've noticed an error in this article please click here to report it so we can fix it.
The 400 bhp gas turbine that powers the Leyland GT 38-ton-gross tractive unit is 1,0001b. lighter than a comparative diesel. Limited production will start in 1970.
THIS WEEK British Leyland Motor Corporation unveiled the gas-turbine-erigined truck (see page 80) which it is showing at the Commercial Motor Show that opens at Earls Court today. Known as the GT truck, it is a six-wheeled double-drive tractive unit with a Rover-styled luxury cab based on the Ergomatic.
The Leyland 28 /350/R turbine develops up to 400 bhp (BS AU 141 rating) and weighs under 1,0001b, which is approximately half the weight of a comparable quality-built diesel engine. Because it is a two-shaft machine, peak torque is available at zero output speed and the favourable torque/speed relationship provides peak performance characteristics with a limited number of gear ratios.
A regenerator comprising two rotating low-speed heat exchangers provides a substantial reduction in fuel consumption by pre-heating the intake air from the compressor and variable power-turbine nozzles augment fuel economy in addition to affording overrun engine braking. Life expectancy is in the region of 12,000 running hours, which is equivalent to 300,000/500,000 vehicle miles. Servicing is facilitated by the use of a small number of self-contained subassemblies.
Dr. Albert Fogg, British Leyland's director of engineering, states that the unit is "the first prototype of a model that will go into limited production late in 1970". Adds Dr. Fogg: "It is not an engineering experiment or a purely prestige exercise."
Mr. Noel Penny, general manager of Leyland Gas Turbines, has been largely responsible for the development of the turbine which is based on the Rover unit. The 38-ton-gross six-wheeled tractive unit to which the prototype gas turbine is fitted is described as eminently suitable for longdistance trans-continental operation at speeds around 70 mph. Because of the inherent flexibility of the gas turbine it is also suitable for stop-start urban running.
Leyland technicians point out that the turbine offers a substantial noise reduction in addition to a cleaner exhaust gas. Lowfrequency vibration is eliminated, which is of benefit to the driver and is conducive to longer chassis-component life. By removing heat from the exhaust gas the regenerator eliminates the nuisance of a "hot blast" from the exhaust stacks which are located vertically behind the cab.
The "gasifier" section—compressor and turbine—has a maximum speed of 38,000 rpm, while the power turbine operates at a maximum speed of 30,000 rpm. This is reduced by a single-stage helical gear to an output speed of less than 3,000 rpm. Easy starting from cold is facilitated by a hightension ignition system.
While the unit is normally operated on diesel oil, paraffin or a low-lead-content petrol, it can also be run on a variety of alternative fuels. These include any standard type of distillate fuel, liquid petroleum gas and gaseous fuels.
The rating of the turbine quoted earlier is the heavy-duty rating, the standard rating being 370 bhp. Minimum fuel consumption is 0.392 lb /bhp /h at 68deg F and 0.399 lb /bhp /h at 80deg F. The unit operates on a relatively low pressure ratio of 4 to 1 (at 80deg F) while the mass flow at this temperature is 3.75 lb /sec. Gasifier idling speed is 19,000 rpm and the full-load output-speed range corresponds to a maximum powerturbine speed of 0/3,250 rpm. The capacity of the wet sump of the lubrication system is 2gal.
Dimensions include an overall length excluding starter of 51in., a width of 28in. and a height of 44.2in.
Power is relayed through a five-speed fully-automatic epicyclic gearbox that is hydraulically operated and electrically controlled. There are two forward-drive positions of the control lever which is mounted centrally in the cab, the "low" position providing a selection of ratios that gives optimum performance and the "high" position a selection that affords optimum fuel economy. The ratio range comprises ratios of 5.22 to 1, 3.23 to 1, 2.125 to 1, 1.5 to 1 and (top) 1 to 1, the reverse ratio being 3.7 to 1. A gearbox full-torque power take-off runs at engine output speed and is controlled from the cab,
The primary structure of the engine is a close-grained iron casing which in plan view follows an H form, with the long sides forming the inner supports for the heatexchanger discs which are set longitudinally (rotating in the same plane as the road wheels).
The compressor turbine is integrally cast with blades of low-stress design to give long life. The gas generator assembly (compressor and compressor turbine on a common shaft) is supported on a roller bearing adjacent to the turbine and a ball bearing adjacent to the compressor.
The reverse-flow combustion chamber is mounted on a flange raised in the top of the pressure casing, between the regenerator discs.
Integrally cast, the single-stage power turbine is carried in a ball bearing at the turbine end and roller bearings at either side of the high-speed pinion in the reduction box.
The glass-ceramic heat exchanger discs are the product of many years of development in conjunction with the Corning Glass Co., USA. This material is chosen because it combines high-temperature capabilities with low thermal expansion and high heat-storage capacity. Pressure-loaded seals have been evolved to give low wear and low leakage, yet without absorbing a lot of driving power. The discs are self-cleaning.
Standard paper filters are fitted in the intake chamber to give adequate protection under normal road conditions; with six of them the replacement period is 1,000 hours. Twin 8in. exhaust ducts are swelled locally to 13in. diameter to incorporate silencers.
The engine is controlled solely by the starter switch and the throttle pedal.
The two driving axles of the bogie and the rear suspension of the UT truck are similar to the Bison units. Of the spiral-bevel type, the leading axle is operated by the through drive from a pair of helical gears and the drive is then relayed through an air-controlled lockable third differential to an output shaft on the rear of the casing and thence through an intermediate propeller shaft to the rearmost spiral-bevel axle. Both axles are fitted with epicyclic hub-reduction gears.
The axles are mounted on a rigid bogie in which each axle is located by radius rods and a pair of inverted semi-elliptic springs of the fully-floating type with centre trunnion bearings. The spring ends are free and rest on the spring brackets, the springs being secured at their centre to the trunnion bearing housing.
Of the beam type the front axle is a rigid I-section alloy steel forging carrying forged steel stub axles in phosphor-bronze bushes. The parallel king pins are located in the axle beam by cotter pins, the thrust being taken centrally on a hardened-steel button at the base of the pin. The wheel hubs are mounted on taper-roller bearings.
An integral unit providing hydraulic power assistance is a feature of the Burman recirculating ball type steering gear, power being supplied by an engine-driven pump. The unit has a constant ratio of 25.2 to 1 giving a positive feel to the steering. A twin-spoke steering wheel is of the safety type and has a 21in. diameter.
The front axle is mounted on Taperlite two-spring ultra lightweight semi-elliptic springs, each leaf of which is parabolically tapered along its length. This feature ensures that a constant stress is maintained throughout the spring and combined with pre-stressing of the leaves gives a substantially increased life, a weight saving of over 50 per cent and a much improved ride. The front of each spring is located by a no-maintenance rubber-bonded shackle pin and the rear with an all-rubber contrasonic shackle.
A full air braking system combines the service, secondary and parking-brake systems, air pressure being provided by an engine-driven compressor. The footbrake operates on all axles and controls the sys tem through a dual brake valve to which the brake pedal is connected mechanically. One half of the valve operates the tractor brakes utilizing direct acting brake chambers fitted adjacent to each wheel. The other half of the valve controls the trailer brakes via the service coupling line.
The secondary and parking brake functions are controlled by a single L-gate lever situated centrally in the driver's cab. The secondary brake is provided by the triplediaphragm brake chambers fitted to the front wheels of the tractor and by the trailer brakes, braking action being progressive. The parking function is provided by spring-actuated brake chambers on the tractor rear wheels, the springs being concentric with the service brake diaphragm.
The air system is based on two main reservoirs and an auxiliary reservoir and is fitted with an automatic water ejection valve actuated by the compressor unloader valve. A low-air-pressure warning buzzer is provided to draw the driver's attention to a malfunction of the air-pressure system.
A brake-drum diameter, lining width and
lining thickness of 6in. and lin. respectively are common to all axles, while total braking areas are 975 cu.in. for the foot brake and 650 cu.in. for the hand brake.
The frame is built of straight pressed-steel channel sections of 3in. by 9+m. by +in. that are fully braced with cross-members and strengthened over the section of maximum stress by a 4in. L-type flitch plate. Detachable one-piece steel-disc vented wheels are fitted with 11 22.5 tubeless tyres. The circular rolled-steel tank has a capacity of 75gal.
Vehicle dimensions include a wheelbase of I32in., an overall length of 241in., a track width of 74.25in., and a laden frame height of 38.581n. The length from the back of the cab to the rear of the frame is 176in.
Other details include a 24V electrical
system, a Butec alternator and starter and two 85 amp /h 12V batteries. Twin windtone electric horns, high output rectangular headlamps and double filament prefocus bulbs, combined sidelamps and flashers, combined stop-tail lamps and reflectors and electric windscreen wipers are includes in the equipment. All the instruments are grouped in a binnacle mounted directly in front of the driver and include a tachograph.