THE CONTAINER AGE demands great changes
Page 63
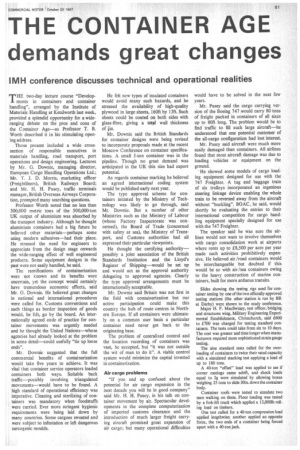
If you've noticed an error in this article please click here to report it so we can fix it.
IMH conference discusses technical and operational realities
!THE two-day lecture course "Develop-1ments in containers and container handling", arranged by the Institute of Materials Handling at Kenilworth last week, provided a splendid opportunity for a wideranging debate on the pros and cons of the Container Age—as Professor T. B. Worth described it in his stimulating opening address.
Those present included a wide crosssection of responsible executives in materials handling, road transport, port operations and design engineering. Lectures by Mr. G. Downie, managing director, European Cargo Handling Operations Ltd.; Mr. T. J. D. Morris, marketing officer (Freightliners), British Railways Board; and Mr. H. H. Pusey, traffic terminals manager, British Overseas Airways Corporation, prompted many searching questions.
Professor Worth noted that no less than 300,000 metric tons of the 500,000-ton UK output of aluminium was absorbed by the transport industry. Although he thought aluminium containers had a big future he believed other materials—perhaps some using modern adhesives—had their place. He stressed the need for engineers to appreciate from the design stage onwards the wide-ranging effect of well engineered products. Some equipment designs in the past were not easily handled, he said.
The ramifications of containerization were not known and its benefits were uncertain, yet the concept would certainly have tremendous economic effects, said Mr. G. Downie. He believed great changes in national and international procedures were called for. Customs conventions and such things as border inspection of goods would, he felt, go by the board. An internationally agreed code of practice for container movements was urgently needed and he thought the United Nations—whose agencies had already looked at the problem in some detail—could usefully "tie up loose ends".
Mr. Downie suggested that the full commercial benefits of containerization would take five years to achieve. It was vital that container service operators loaded containers both ways. Suitable back traffic—possibly involving triangulated movements—would have to be found. A high standard of operational efficiency was imperative. Cleaning and sterilizing of containers was mandatory when foodstuffs were carried. Ever more stringent hygienic requirements were being laid down by many countries. Some cargoes sweated and were subject to infestation or left dangerous carcogenic moulds.
He felt new types of insulated containers would avoid many such hazards, and he stressed the availability of high-quality plywood in large sheets, 160ft by 13ft. Such sheets could be coated on both sides with glass-fibre, giving a total wall thickness of fin.
Mr. Downie said the British Standards for container designs were being revised to incorporate proposals made at the recent Moscow Conference on container specifications. A small 5-ton container was in the pipeline. Though no great demand was anticipated in the UK this size had export potential.
As regards container marking he believed an agreed international coding system would be published early next year.
The type approval scheme for containers initiated by the Ministry of Technology was likely to go through, said Mr. Downie. But a number of other Ministries such as the Ministry of Labour (whose Factory Inspectorate was concerned), the Board of Trade (concerned with safety at sea), the Ministry of Transport, and Customs authorities had all expressed their particular viewpoints.
He thought the certifying authority— possibly a joint association of the British Standards Institution and the Lloyd's Register of Shipping—would be set up and would act as the approval authority delegating to approved agencies. Clearly the type approval arrangements must be internationally acceptable.
Mr. Downie said Britain was not first in the field with containerization but our active participation could make this country the hub of route centres in Northern Europe. If all containers were ultimately on a common user basis a particular container need never get back to the originating base.
The problem of centralized control and the location recording of containers was vast, he accepted, but "it was not outside the wit of man to do it". A viable control system would minimize the capital invested in containerization.
Air cargo problems "If you end up confused about the potential for air cargo expansion in the next decade you will be in good company" said Mr. H. H. Pusey, in his talk on container movement by air. Spectacular developments in the complete computerization of imported customs clearance and the introduction of much larger freight carrying aircraft promised great expansion of air cargo; but many operational difficulties would have to be solved in the next few years.
Mr. Pusey said the cargo carrying version of the Boeing 747 would carry 80 tons of freight packed in containers of all sizes up to 80ft long. The problem would be to find traffic to fill such large aircraft—he understood that one potential customer of the all-cargo configuration had lost interest.
Mr. Pusey said aircraft were much more easily damaged than containers. All airlines found that most aircraft damage was due to loading vehicles or equipment on the ground.
' He showed some models of cargo loading equipment designed for use with the 747 Freighter. A tug and baggage train of six trolleys incorporated an ingenious steering linkage device enabling the whole train to be reversed away from the aircraft without "buckling". BOAC, he said, would shortly be evaluating the entries to their international competition for cargo handling equipment specially designed for use with the 747 Freighter.
The speaker said he was sure the airlines would not want to involve themselves with cargo consolidation work at airports where rents up to £8,500 per acre per year made such activities prohibitively expensive. He believed air /road containers would be interchangeable but doubted if this would be so with air /sea containers owing to the heavy construction of marine containers, built for more arduous transits.
Slides showing the testing ,rigs used for container testing by one of the two officially approved testing stations (the other station is run by BR at Derby) were shown to the study conference.
Major H. F. MacSwiney, test officer, bridging and structures wing, Military Engineering Experimental Establishment, Christchurch, said £600 to E700 was charged for testing standard containers. The tests could take from six to 10 days. The cost was greater and time longer when manufacturers required more sophisticated strain gauge testing.
The nine standard tests called for the overloading of containers to twice their rated capacity with a simulated stacking test applying a load of up to 180 tons.
A 40-ton "offset" load was applied to see if corner castings came adrift, and shock loads equal to 2g were simulated by allowing boxes weighing 25 tons to slide 30in. down the container body.
Container roofs were tested to simulate two men walking on them. Floor loading was tested by a fork-lift truck which applied a 12,000lb rolling load on timbers.
One test called for a 40-ton compression load applied lengthwise; another applied an opposite force, the two ends of a container being forced apart with a 40-ton jack.