GET YOUR SKATES OW
Page 42
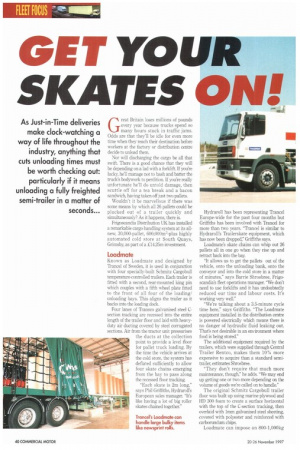
Page 43
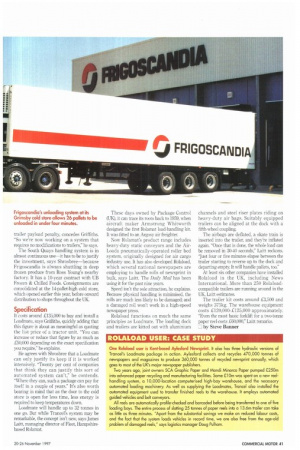
If you've noticed an error in this article please click here to report it so we can fix it.
As Just-in-Time deliveries make clock-watching a way of life throughout the industry, anything that cuts unloading times must be worth checking out: particularly if it means unloading a fully freighted semi-trailer in a matter of seconds...
Great Britain loses millions of pounds every year because trucks spend so many hours stuck in traffic jams. Odds are that they'll be idle for even more time when they reach their destination before workers at the factory or distribution centre decide to unload them.
Nor will discharging the cargo be all that swift. There is a good chance that they will be depending on a lad with a forklift. If you're lucky, he'll manage not to bash and batter the truck's bodywork to perdition. If you're really unfortunate he'll do untold damage, then scuttle off for a tea break and a bacon sandwich, having taken off just two pallets.
Wouldn't it be marvellous if there was some means by which all 26 pallets could be plucked out of a trailer quickly and simultaneously? As it happens, there is.
Frigoscandia Distribution UK has installed a remarkable cargo handling system at its allnew, 30,000-pallet, 600,000m3-plus highly automated cold store at South Quays, Grimsby, as part of a £14.25m investment.
Loadmate
Known as Loadmate and designed by Trancel of Sweden, it is used in conjunction with four specially-built Schmitz Cargobull temperature-controlled trailers. Each trailer is fitted with a second, rear-mounted king pin which couples with a fifth wheel plate fitted to the front of all four of the loading/ unloading bays. This aligns the trailer as it backs into the loading dock.
Four lanes of Transco galvanised steel Csection tracking are recessed into the entire length of the trailer floor and laid with heavyduty air ducting covered by steel corrugated sections. Air from the tractor unit pressurises the ducts at the collection point to provide a level floor for pallet truck loading. By the time the vehicle arrives at the cold store, the system has deflated sufficiently to allow four skate chains emerging from the bay to pass along the recessed floor tracking.
"Each skate is 2m long," says Phil Griffiths, Hvdraroll's European sales manager. "It's like having a lot of big roller skates chained together." Hydraroll has been representing Trance] Europe-wide for the past four months but Griffiths has been involved with Trancel for more than two years. "Trancel is similar to Hydraroll's Trailerskate equipment, which has now been dropped," Griffiths says.
Loadmate's skate chains can whip out 26 pallets all in one go when they rise up and retract back into the bay.
"It allows us to get the pallets out of the vehicle, onto the unloading bank, onto the conveyor and into the cold store in a matter of minutes," says Barrie Shrosbree, Frigoscandia's fleet operations manager. "We don't need to use forklifts and it has undoubtedly reduced our time and labour costs. It's working very well."
"We're talking about a 3.5-minute cycle time here," says Griffiths. "The Loadmate equipment installed in the distribution centre is powered electrically which means there is no danger of hydraulic fluid leaking out. That's not desirable in an environment where food is being stored."
The additional equipment required by the trailers, which were supplied through Central Trailer Rentco, makes them 10% more expensive to acquire than a standard semitrailer, estimates Shrosbree.
"They don't require that much more maintenance, though," he adds. "We may end up getting one or two more depending on the volume of goods we're called on to handle."
The original Schmitz Cargobull trailer floor was built up using marine plywood and HD 300 foam to create a surface horizontal with the top of the C-section tracking, then overlaid with lmm galvanised steel sheeting, covered with polyester and reinforced with carborundum chips.
Loadmate can impose an 800-1,000kg trailer payload penalty, concedes Griffiths. "So we're now working on a system that requires no modifications to trailers," he says.
The South Quays handling system is in almost continuous use—it has to be to justify the investment, says Shrosbree—because Frigoscandia is always shuttling in deep frozen produce from Ross Young's nearby factory. It has a 10-year contract with UB Frozen & Chilled Foods. Consignments are consolidated at the 14-pallet-high cold store, which opened earlier this year, before onward distribution to shops throughout the UK.
Specification
It costs around £135,000 to buy and install a Loadmate, says Griffiths, quickly adding that this figure is about as meaningful as quoting the list price of a tractor unit. "You can increase or reduce that figure by as much as ,C50,0tX) depending on the exact specification you require," he explains.
He agrees with Shrosbree that a Loadmate can only justify its keep if it is worked intensively. "Twenty per cent of companies that think they can justify this sort of automated system can't," he contends. "Where they can, such a package can pay for itself in a couple of years." It's also worth bearing in mind that as the door to the cold store is open for less time, less energy is required to keep temperatures down.
Loadmate will handle up to 32 tonnes in one go. But while Trancel's system may be remarkable, the concept isn't new, says James Laitt, managing director of Fleet, Hampshire. based Rolamat These days owned by Package Control (UK), it can trace its roots back to 1959, when aircraft maker Armstrong Whitworth designed the first Rolamat load-handling kit. It was fitted to an Argosy air freighter.
Now Rolamat's product range includes heavy-duty static conveyors and the AirLoada pneumatically-operated roller bed system, originally designed for air cargo industry use. It has also developed Rolaload, which several national newspapers are employing to handle rolls of newsprint in bulk, says Laitt. The Daily Mail has been using it for the past nine years.
Speed isn't the sole attraction, he explains. Because physical handling is minimised, the rolls are much less likely to be damaged; and a damaged roll won't work in a high-speed newspaper press.
Rolaload functions on much the same principles as Loadmate. The loading dock and trailers are kittec.1 out with aluminium channels and steel riser plates riding on heavy-duty air bags. Suitably equipped trailers can be aligned at the dock with a fifth-wheel coupling.
The airbags are deflated, a skate train is inserted into the trailer, and they're inflated again. "Once that is done, the whole load can be removed in 30-40 seconds," Laitt reckons. "Just four or five minutes elapse between the trailer starting to reverse up to the dock and departing empty. [twill handle pallets, too."
At least six other companies have installed Rolaload in the UK, including News International. More than 250 Rolaloadcompatible trailers are running around in the UK, Laitt estimates, The trailer kit costs around £3,500 and weighs 375kg. The warehouse equipment costs LI 20,000-L125,000 approximately, "Even the most basic forklift for a two-tonne paper reel costs £60,000," Laitt remarks.
E by Steve Banner
ROLALOAD USER; CASE STUDY
One Rololood user is Kent-based Aylesford Newsprint. It also has three hydraulic versions of Trancel's Loadmate package in action. Aylesford collects and recycles 470,000 tonnes of newspapers and magazines to produce 360,000 tonnes of recycled newsprint annually, which goes to most of the UK's major newspaper publishers.
Two years ago, joint owners SCA Graphic Paper and Mondi Minorco Paper pumped £250m into advanced paper recycling and manufacturing facilities. Some ZIOrn was spent on a new reelhandling system, o 10,000-location computerised high-bay warehouse, and the necessary automated loading machinery. As well as supplying the Loadmates, Trancel also installed the automated equipment used to transfer finished reels to the warehouse. It employs automated guided vehicles and belt conveyors.
All reels are automatically profile-checked and barcodecl before being transferred to one of five loading bays. The entire process of slotting 25 tonnes of paper reels into a 13.6m trailer can take as little as three minutes. "Apart from the substantial savings we make on reduced labour costs, and the fact that the system loads vehicles in record time, we are also free From the age-old problem of damaged reels," says logistics manager Doug Pulham.