Turbine set for take-off
Page 69
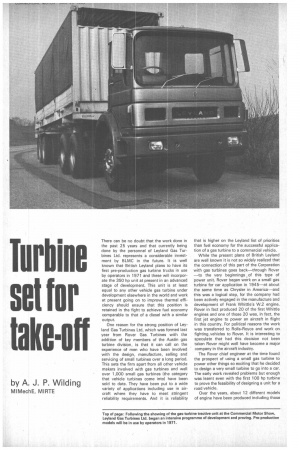
Page 70
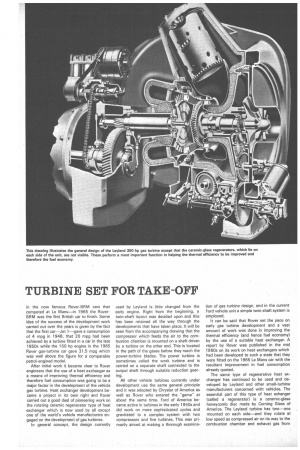
Page 71
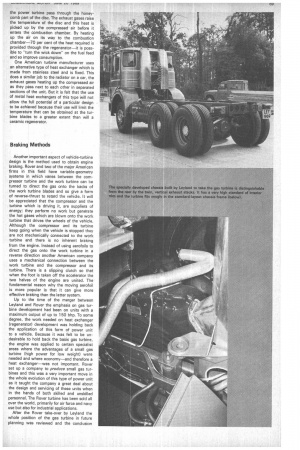
Page 72
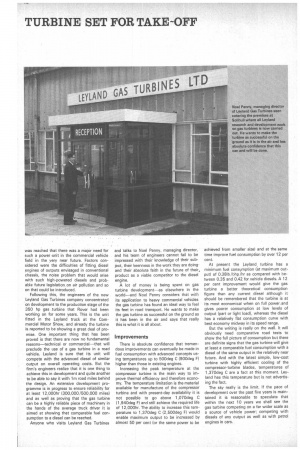
If you've noticed an error in this article please click here to report it so we can fix it.
by A. J. P. Wilding
MIMechE, MIRTE
There can be no doubt that the work done in the past 25 years and that currently being done by the personnel of Leyland Gas Turbines Ltd. represents a considerable investment by BLMC in the future, It is well known that British Leyland plans to have its first pre-production gas turbine trucks in use by operators in 1971 and these will incorporate the 350 hp unit at present in an advanced stage of development. This unit is at least equal to any other vehicle gas turbine under development elsewhere in the world and work at present going on to improve thermal efficiency should ensure that this position is retained in the fight to achieve fuel economy comparable to that of a diesel with a similar output.
One reason for the strong position of Leyland Gas Turbines Ltd, which was formed last year from Rover Gas Turbines with the addition of key members of the Austin gas turbine division, is that it can call on the experience of men who have been involved with the design, manufacture, selling and servicing of small turbines over a long period. This sets the firm apart from all other vehicle makers involved with gas turbines and well over 1,000 small gas turbines (the category that vehicle turbines come into have been sold to date. They have been put to a wide variety of applications including use in aircraft where they have to meet stringent reliability requirements. And it is reliability that is higher on the Leyland list of priorities than fuel economy for the successful application of a gas turbine to a commercial vehicle.
While the present plans of British Leyland are well known it is not so widely realized that the connection of this part of the Corporation with gas turbines goes back—through Rover —to the very beginnings of this type of power unit. Rover began work on a small gas turbine for car application in 1945—at about the same time as Chrysler in America and this was a logical step, for the company had been actively engaged in the manufacture and development of Frank Whittle's W.2 engine. Rover in fact produced 20 of the first Whittle engines and one of those 20 was, in fact, the first jet engine to power an aircraft in flight in this country. For political reasons the work was transferred to Rolls-Royce and work on fighting ,vehicles to Rover. It is interesting to speculate that had this decision not been taken Rover might well have become a major company in the aircraft industry.
The Rover chief engineer at the time found the prospect of using a small gas turbine to power other things so exciting that he decided to design a very small turbine to go into a car. The early work revealed problems but enough was learnt even with the first 100 hp turbine to prove the feasibility of designing a unit for a road vehicle.
Over the years, about 12 different models of engine have been produced including those in the now famous Rover-BRM cars that competed at Le Mans—in 1965 the RoverBRM was the first British car to finish. Some idea of the success of the development work carried out over the years is given by the fact that the first car—Jet 1—gave a consumption of 4 mpg in 1948, that 20 mpg had been achieved by a turbine fitted in a car in the late 1950s while the 150 hp engine in the 1965 Rover gas-turbine car gave 31.5 mpg which was well above the figure for a comparable petrol-engined model.
After initial work it became clear to Rover engineers that the use of a heat exchanger as a means of improving thermal efficiency and therefore fuel consumption was going to be a major factor in the development of the vehicle gas turbine. Heat exchanger development became a project in its own right and Rover carried out a good deal of pioneering work on the rotating ceramic regenerator type of heat exchanger which is now used by all except one of the world's vehicle manufacturers engaged on the development of gas turbines.
In general concept, the design currently used by Leyland is little changed from the early engine. Right from the beginning, a twin-shaft layout was decided upon and this has been retained all the way through the developments that have taken place. It will be seen from the accompanying drawing that the compressor which feeds the air to the combustion chamber is mounted on a shaft driven by a turbine on the other end. This is located in the path of the gases before they reach the power-turbine blades. The power turbine is sometimes called the work turbine and is carried on a separate shaft connected to the output shaft through suitable reduction gearing.
All other vehicle turbines currently under development use the same general principle and it was adopted by Chrysler of America as well as Rover who entered the "game" at about the same time. Ford of America became active in turbines in the early 1950s and did work on more sophisticated cycles and gravitated to a complex system with two compressors and five turbines. This was primarily aimed at making a thorough examina
tion of gas turbine design, and in the current Ford vehicle unit a simple twin-shaft system is employed.
It can be said that Rover set the pace on early gas turbine development and a vast amount of work was done in improving the thermal efficiency (and hence fuel economy) by the use of a suitable heat exchanger. A report by Rover was published in the mid 1960s on its work on heat exchangers which had been developed to such a state that they were fitted on the 1965 Le Mans car with the resultant improvement in fuel consumption already quoted.
The same type of regenerative heat exchanger has continued to be used and developed by Leyland and other small-turbine manufacturers concerned with vehicles. The essential part of this type of heat exhanger (called a regenerator) is a ceramic-glass honeycomb disc made by Corning Glass of America. The Leyland turbine has two one mounted on each side—and they rotate at low speed as compressed air on its way to the combustion chamber and exhaust gas from the power turbine pass through the honeycomb part of the disc. The exhaust gases raise the temperature of the disc and this heat is picked up by the compressed air before it enters the combustion chamber. By heating up the air on its way to the combustion chamber-70 per cent of the heat required is provided through the regenerator—it is possible to "turn the wick down" on the fuel feed and so improve consumption.
One American turbine manufacturer uses an alternative type of heat exchanger which is made from stainless steel and is fixed. This does a similar job to the radiator on a car, the exhaust gases heating up the compressed air as they pass next to each other in separated sections of the unit. But it is felt that the use of metal heat exchangers of this type will not allow the full potential of a particular design to be achieved because their se will limit the temperature that can be obtained at the turbine blades to a greater extent than will a ceramic regenerator.
Braking Methods
Another important aspect of vehicle-turbine design is the method used to obtain engine braking. Rover and two of the major American firms in this field have variable-geometry systems in which vanes between the compressor turbine and the work turbine can be turned to direct the gas onto the backs of the work turbine blades and so give a form of reverse-thrust to retard the vehicle. It will be appreciated that the compressor and the turbine which is driving it, are suppliers of energy; they perform no work but generate the hot gases which are blown onto the work turbine that drives the wheels of the vehicle. Although the compressor and its turbine keep going when the vehicle is stopped they are not mechanically connected to the work turbine and there is no inherent braking from the engine. Instead of using aerofoils to direct the gas onto the work turbine in a reverse direction another American company uses a mechanical connection between the work turbine and the compressor and its turbine. There is a slipping clutch so that when the foot is taken off the accelerator the two halves of the engine are united, The fundamental reason why the moving aerofoil is more popular is that it can give more effective braking than the latter system.
Up to the time of the merger between Leyland and Rover the emphasis on gas turbine development had been on units with a maximum output of up to 150 bhp. To some degree, the work needed on heat exchanger (regenerator) development was holding back the application of this form of power unit to a vehicle. Because it was felt to be undesirable to hold back the basic gas turbine, the engine was applied to certain specialist areas where the advantages of a small gas turbine (high power for low weight) were needed and where economy—and therefore a heat exchanger--was not important. Rover set up a company to produce small gas turbines and this was a very important move in the whole evolution of this type of power unit as it taught the company a great deal about the design and servicing of these units when in the hands of both skilled and unskilled personnel. The Rover turbine has been sold all over the world, primarily for air force and navy use but also for industrial applications.
After the Rover take-over by Leyland the whole position of the gas turbine in future planning was reviewed and the conclusion was reached that there was a major need for such a power unit in the commercial vehicle field in the very near future. Factors considered were the difficulties of fitting diesel engines of outputs envisaged in conventional chassis, the noise problem that would arise with such high-powered diesels and probable future legislation on air pollution and so on that could be introduced.
Following this, the engineers of the new Leyland Gas Turbines company concentrated on development to the production stage of the 350 hp gas turbine that Rover had been working on for some years. This is the unit fitted in the Leyland truck at the Commercial Motor Show, and already the turbine is reported to be showing a great deal of promise. One important thing that has been proved is that there are now no fundamental reasons—technical or commercial--that will preclude the use of a gas turbine in a road vehicle. Leyland is sure that its unit will compete with the advanced diesel of similar output on overall operating costs. But the firm's engineers realize that it is one thing to achieve this in development and quite another to be able to say it with 1m road miles behind the design. An extensive development programme is in progress to ensure reliability for at least 12,000hr (300,000 /500,000 miles) and as well as proving that the gas turbine can be a highly reliable piece of machinery in the hands of the average truck driver it is aimed at showing that comparable fuel consumption to a diesel can be reached.
Anyone who visits Leyland Gas Turbines and talks to Noel Penny, managing director, and his team of engineers cannot fail to be impressed with their knowledge of their subect, their keenness in the work they are doing' and their absolute faith in the future of their, product as a viable competitor to the diesel engine.
A lot of money is being spent on gas turbine development--as elsewhere in the world—and Noel Penny considers that with its application to heavy commercial vehicles the gas turbine has found an ideal way to feel its feet in road transport. He wants to make the gas turbine as successful on the ground as it has been in the air and says that really this is what it is all about.
I mprovemerrts
There is absolute confidence that tremendous improvements can eventually be made in fuel consumption with advanced concepts using temperatures up to 500cieg C I900deg F) higher than those in existing engines.
Increasing the peak temperature at the compressor turbine is the main way to improve thermal efficiency and therefore economy. The temperature limitation is the material available for manufacture of the compressor turbine and with present-day availability it is not possible to go above 1,070deg C I1,940deg Fl and still achieve the required life of 12,000hr. The ability to increase this temperature to 1,370deg C (2,500deg F) would enable maximum output to be increased by almost 50 per cent (or the same power to be achieved from smaller size) and at the same time improve fuel consumption by over 12 per cent.
At present the Leyland. turbine has a minimum fuel consumption (at maximum out
put) of 0.381h/bhp/hr as compared with be tween 0.35 and 0.42 for vehicle diesels. A 12 per cent improvement would give the gas turbine a better theoretical consumption figure than any current diesel although it should be remembered that the turbine is at its most economical when on full power and gives poorer consumption at low levels of output (part or light load), whereas the diesel has a relatively flat consumption curve with best economy midway in its speed range.
But the writing is really on the wall. It will obviously need comparative road tests to show the full picture of consumption but there are definite signs that the gas turbine will give at least a comparable fuel consumption with a diesel of the same output in the relatively near future. And with the latest simple, low-cost turbine with highly efficient cooling of the compressor-turbine blades, temperatures of 1,370deg C are a fact at this moment. Leyland has this temperature but is not advertising the fact.
The sky really is the limit. If the pace of development over the past five years is main tained it is reasonable to speculate that within the next 10 years we shall see the gas turbine competing on a far wider scale as a source of vehicle power; competing with diesels of any output as well as with petrol engines in cars.