The complex challenge
Page 55

Page 56
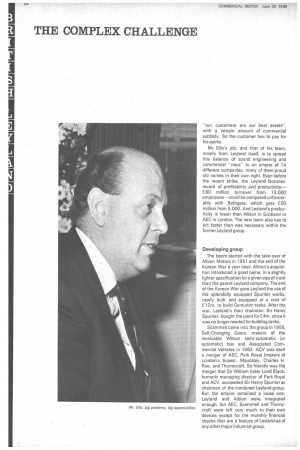
Page 57
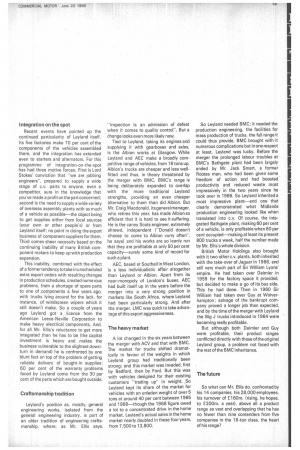
Page 58
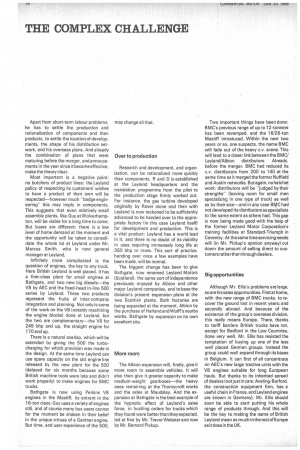
If you've noticed an error in this article please click here to report it so we can fix it.
British Leyland's truck and bus division empire, run from Leyland by Mr. Ron Ellis, former general manager of Leyland Motors itself is, at the moment, a complicated and slightly_ artificial structure. For Lord Stokes, as chief executive, had tofind some frontiers to demarcate his empire into manageable slices. So it is that truck and bus division does not include the vans made in the Midlands—both those derived from cars, which is reasonable enough, and, perhaps less sensibly, the purposedesigned larger units made from specially built components. This particular demarcation could well perpetuate one of the problems—formerly the biggest on BMC's truck side—that it was directed from the Midlands by men whose heart was in mass-produced private cars.
The other "artificiality" is on another side altogether. Scammell is in the construction equipment division, and although well known for its special trucksfor oilfields and the like, as well as trailers, the bulk of its production is in more normal commercial vehicles which compete with the truck and bus division's products.
But the division makes sense if it is looked at in terms of productive resources: the production of vans and Scarnrnells is physically separate from that of other trucks and buses: and the division's main lines are clear enough.
To make the most
Buses apart, it is aimed at producing a more complete range of vehicles than anyone else in Britain, and as complete as its only two equivalents in Europe. Fiat and Daimler-Benz. And indeed there is a curious resemblance between Mr. Ellis's division and Fiat and Daimler-Benz. All three are run by sales-orientated engineers with a strong inclination to make things that are practicable and profitable, rather than original for the sake of it. Even the provinces from which the three companies come, Piedmont, Swabia and Lancashire, are famous in their own countries for their hardheadedness and practicality, and these qualities admirably suit the business of making trucks and buses. All three companies have learnt
to balance the fact that, as Mr. Ellis says, Lord Stokes: frontiers had to be drawn,
"our customers are our best assets, with a certain amount of commercial subtlety. So the customer has to pay for his quirks.
Mr. Ellis's job, and that of his team, mostly from Leyland itself, is to spread this balance of sound engineering and commercial "nousto an empire of 14 different companies, many of them proud old names in their own right. Even before the recent strike, the Leyland factories' record of profitability and productivity— £80 million turnover from 13,000 employees--could be compared unfavourably with Bathgate, which gets £50 million from 5.000. And Leyland's productivity is lower than Albion in Scotland or AEC in London. The new team also has to act faster than was necessary within the former Leyland group.
Developing group The boom started with the take-over of Albion Motors in 1951 and the end of the Korean War a year later, Albion's acquisition introduced a good name, in a slightly lighter specification for a given size of truck than the parent Leyland company. The end of the Korean War gave Leyland the use of the splendidly equipped Spurrier works, newly built and equipped at a cost of £ 12m. to build Centurion tanks. After the war. Leyland's then chairman, Sir Henry Spurrier, bought the plant for £4m. since it was no longer needed for building tanks.
Scammell came into the group in 1955, Self-Changing Gears, makers of the invaluable Wilson semi-automatic (or automatic) box and Associated Commercial Vehicles in 1962. ACV was itself a merger of AEC, Park Royal (makers of London's buses), Maudslay, Charles H. Roe, and Thornycroft. So friendly was the merger that Sir William (later Lord) Black, formerly managing director of Park Royal and ACV, succeeded Sir Henry Spurrier as chairman of the combined Leyland group. But the empire remained a loose one: Leyland and Albion were integrated enough, but AEC. Scammell and Thornycroft were left very much to their own devices except for the monthly financial checks that are a feature of Leyland-as of any other major industrial group. Integration on the spot Recent events have pointed up the continued particularity of Leyland itself. Its five factories make 70 per cent of the components of the vehicles assembled there, and the integration has extended even to starters and alternators. For this programme of integration-on-the-spot has had three motive forces. First is Lord Stokes' conviction that "we are jobbing engineers", prepared to supply a wide range of c.v. parts to anyone, even a competitor, sure in the knowledge that you've made a profit on the pa rt concerned; second is the need to supply a wide variety of overseas assembly plants with as much of a vehicle as possible—the object being to get supplies either from local sources (your own or other people's) or from Leyland itself; no point in doing the export business of component suppliers for them. Third comes sheer necessity based on the continuing inability of many British component makers to keep up with production expansion.
This inability, combined with the effect of a formertendencytotake in unscheduled extra export orders with resulting changes in production schedules, created numerous problems, from a shortage of spare parts to one of components a few years ago, with trucks lying around for the lack, for instance, of windscreen wipers which it still doesn't make. So a couple of years ago Leyland got a licence from the American Leece-Neville Corporation to make heavy electrical components. And, for all Mr. Ellis's reluctance to get more integrated than he has to be (the capital investment is heavy and makes the business vulnerable to the slightest downturn in demand) he is confronted by one blunt fact on top of the problem of getting reliable delivery of bought-in supplies: 60 per cent of the warranty problems faced by Leyland come from the 30 per cent of the parts which are bought outside.
Craftsmanship tradition Leyland's position as, mostly, general engineering works, isolated from the general engineering industry, is part of an older tradition of engineering craftsmanship, where, as Mr. Ellis says, "inspection is an admission of defeat when it comes to quality control", But a change looks even more likely now.
Tied to Leyland, taking its engines and supplying it with gearboxes and axles, is the Albion works at Glasgow. While Leyland and AEC make a broadly competitive range of vehicles, from 16 tons up, Albion's trucks are cheaper and less wellfitted and thus, in theory threatened by the merger with BMC. BMC's range is being deliberately expanded to overlap with the more traditional Leyland strengths, providing an even cheaper alternative to them than did Albion. But Mr. Craig Macdonald, its general manager, who retires this year, has made Albion so efficient that it is hard to see it suffering. He is the canny Scots engineer, extremely shrewd, independent ("Donald doesn't choose to come to Albion vurry often", he says) and his works are so leanly run that they are profitable at only 50 per cent capacity—surely some kind of record for such a plant.
AEC, based at Southall in West London, is a less individualistic affair altogether than Leyland or Albion. Apart from its near-monopoly of London's buses, AEC had built itself up in the years before the merger into a very strong position in markets like South Africa, where Leyland had been particularly strong. And after the merger, LMC was quick totake advantage of this export aggressiveness.
The heavy market A lot changed in the six years between the merger with ACV and that with BMC. The market for trucks shifted dramatically in favour of the weights in which Leyland group had traditionally been strong: and this market was invaded, first by Bedford, then by Ford. But this was with vehicles designed for their existing customers "trading up" in weight. .So Leyland kept its share of the market for vehicles with an unladen weight of over 5 tons at around 40 per cent between 1965 and 1968—though the 1968 figure owed a lot to a concentrated drive in the home market. Leyland's actual sales in the home market nearly doubled in these four years, from 7.500 to 13,800. So Leyland needed BMC; it needed the production engineering, the facilities for mass production of trucks, the full range it could thus provide. BMC brought with it numerous complications but in one respect at least, Leyland was lucky. Before the merger the prolonged labour troubles at BMC's Bathgate plant had been largely ended by Mr. Jack Smart, a former Rootes man, who had been given some freedom of action and had boosted productivity and reduced waste most impressively in the two years since he took over in 1966. So Leyland inherited a most impressive plant—and one that clearly demonstrated what Midlands production engineering looked like when translated into c.v. Of course, the integrated Bathgate plant, making 60 per cent of a vehicle, is only profitable when 80 per cent occupied—making at least its present 800 trucks a week, half the number made by Mr. Ellis's whole division.
British Motor Holdings also brought with it two other c.v. plants, both inherited with the take-over of Jaguar in 1966, and still very much part of Sir William Lyons' empire, He had taken over Daimler in 1959 for the factory space it provided, but decided to make a go of its bus side. This he had done. Then in 1960 Sir William had taken over Guy at Wolverhampton; salvage of the bankrupt company proved a longer job than expected, and by the time of the merger with Leyland the Big J trucks introduced in 1964 were becoming really profitable.
But although both Daimler and Guy were profitable, their product ranges conflicted directly with those of the original Leyland group, a problem not faced with the rest of the BMC inheritance.
The future So what can Mr. Ellis do, confronted by his 14 companies, his 28,000 employees, his turnover of £160m. (rising, he hopes, to £200m. a year), above all a product range so vast and overlapping that he has no fewer than nine contenders from five companies in the 16-ton class, the heart of his range? Apart from short-term labour problems, he has to settle the production and rationalization of components and then products, to settle the location of developments, the shape of his distribution network, and his overseas plans. And already the combination of plans that were maturing before the merger, and annoucements in the year since it became effective, make the theory clear.
Most important is a negative point: no butchery of product lines: the Leyland policy of respecting its customers' wishes to have a product of their own will be respected—however much "badge engineering" this may imply in components. This suggests that even relatively small assembly plants, like Guy at Wolverhampton, will be viable for a long time to come. But buses are different: there is a low level of home demand at the moment and the opportunity will be taken to consolidate the whole lot at Leyland under Mr. Marcus Smith, who is now general manager at Leyland.
Infinitely more complicated is the question of engines, the key to any truck. Here British Leyland is well placed. It has a first-class plant for small engines at Bathgate, and two new big diesels—the V8 by AEC and the fixed-head in-line 500 series by Leyland. These two products represent the fruits of inter-company integration and planning. Not only is some of the work on the V8 (notably machining the engine blocks) done at Leyland, but the two are complementary the V8 for 249 bhp and up, the straight engine for 170 and up.
There is a natural overlap, which will be extended by giving the 500 the turbocharging for which provision was made in the design. At the same time Leyland can use spare capacity on the old engine line released by the new plant for the 500 (delayed for six months because some British machine tools were late and didn't work properly) to make engines for BMC trucks.
Bathgate is now using Perkins V8 engines in the Mastiff, its entrant in the 16-ton class: Guy uses a variety of engines still, and of course many bus users cannot for the moment be shaken in their belief in the unique virtues of a Gardner engine. But time, and user experience of the 500, may change all that.
Over to production Research and development, and organization, can be rationalized more quickly than components. R and D is established at the Leyland headquarters and the translation programme from the pilot to the production stage firmly worked out. For instance, the gas turbine developed originally by Rover alone and then with Leyland is now reckoned to be sufficiently advanced to be handed over to the appropriate factory (in this case Leyland itself) for development and production. This is a vital product: Leyland has a world lead in it, and there is no doubt of its viability in uses requiring immensely long life at 350 bhp or more. This sort of practice, handing over once a few examples have been made, will be normal.
The biggest change has been to give Bathgate, now renamed Leyland Motors (Scotland), the same sort of independence previously enjoyed by Albion and other major Leyland companies, and to base the division's present expansion plans at the two Scottish plants. Both factories are being expanded at the moment, Albion by the purchase of Harland and Wolff's nearby works, Bathgate by expansion on its own excellent site.
More room The Albion expansion will, firstly, give it more room to assemble vehicles. It will also then give it greater capacity to make medium-weight gearboxes—the heavy ones remaining at the Thornycroft works and the axles at Maudslay. And the expansion at Bathgate is the best example of the hypnotic effect of Leyland's sales force, in hustling orders for trucks which they found were better than they expected, led at first by Mr. Trevor Webster and now by Mr. Bernard Pickup. Two important things have been done: BMC's previous range of up to 12-tonners has been revamped, and the 16/26-ton Mastiff introduced. Within the next two years or so, one suspects, the name BMC will fade out of the heavy c.v. scene. This will lead to a closer link between the BMC/ Leyland/Albion distributors. Already, before the merger, BMC had reduced its c.v. distributors from 200 to 140 at the same time as it merged the former Nuffield and Austin networks, But again, no hatchet work: distributors will be "judged by their strengths" (leaving room for small men specializing in one type of truck) as well as by their size—and in any case BMC had not developed its distributors as specialists to the same extent as others had. This gap is now being made good with the help of the former Leyland Motor Corporation's training facilities at Standard-Triumph in Coventry. At the same time servicing needs will (in Mr. Pickup's opinion anyway) cut down the amount of selling direct to customers rathertha n through dealers.
Big opportunities Although Mr. Ellis's problems are large, soare hissales opportunities. First at home,, with the new range of BMC trucks, to recover the ground lost in recent years; and secondly abroad. And because of the existence of the group's overseas division, this really means Europe. There, thanks to tariff barriers British trucks have not, except for Bedford in the Low Countries, done very well. Mr. Ellis has resisted the temptation of buying up one of the less well placed German groups. Instead the group could well expand through its bases in Belgium. It can first of all concentrate on AEC's new large tractive units with the V8 engines suitable for long European hauls. But thanks to its inherited spread of dealers (not just in cars: Aveli ng-Barford, the construction equipment firm, has a useful chain in France, and Leyland engines are known in Germany), Mr. Ellis should soon be able to start putting his whole range of products through. And this will be the key to making the name of British Leyland mean as much in the rest of Europe as it does in the UK.