t's
Page 32
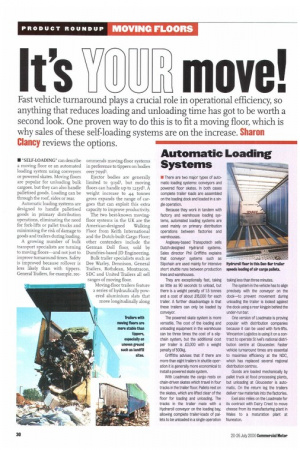
Page 33
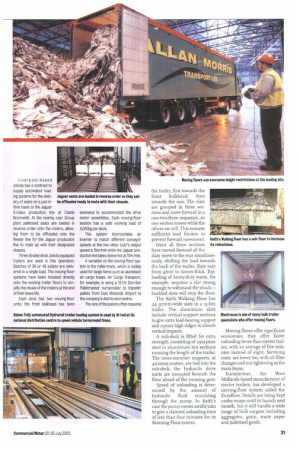
If you've noticed an error in this article please click here to report it so we can fix it.
ove!
• "SELF-LOADING" can describe a moving floor or an automated loading system using conveyors or powered skates. Moving floors are popular for unloading bulk cargoes, but they can also handle palletised goods. Loading can be through the roof, sides or rear.
Automatic loading systems are designed to handle palletised goods in primary distribution operations, eliminating the need for fork-lifts or pallet trucks and minimising the risk of damage to goods and trailers during loading.
A growing number of bulk transport specialists are turning to moving floors—and not just to improve turnaround times. Safety is improved because rollover is less likely than with tippers. General Trailers, for example, rec ommends moving-floor systems in preference to tippers on bodies over 70yd3.
Ejector bodies are generally limited to 9ryd3, but moving floors can handle up to 125yd3. A weight increase to 44 tonnes gross expands the range of cargoes that can exploit this extra capacity to improve productivity.
The two best-known movingfloor systems in the UK are the American-designed Walking Floor from Keith International and the Dutch-built Cargo Floor; other contenders include the German Doll floor, sold by Dumfries-based JD Engineering.
Bulk trailer specialists such as Dee Warley, Dennison, General Trailers, Rothdean, Montracon, S DC and United Trailers all sell ranges of moving floor.
Moving-floor trailers feature a series of hydraulically powered aluminium slats that move longitudinally along • There are two major types of automatic loading systems: conveyors and powered floor skates. In both cases complete trailer loads are assembled on the loading dock and loaded in a single operation.
Because they work in tandem with factory and warehouse loading systems, automated loading systems are used mainly an primary distribution operations between factories and warehouses.
Anglesey-based Transpotech sells Dutch-designed Hydraroll systems. Sales director Phil Griffiths explains that conveyor systems such as Slipchain are used mainly for intensive short shuttle runs between production lines and warehouses.
They are exceptionally fast, taking as little as 90 seconds to unload, but there is a weight penalty of 1.5 tonnes and a cost of about £15,000 for each trailer. A further disadvantage is that these trailers can only be loaded by conveyor.
The powered skate system is more versatile. The cost of the loading and unloading equipment in the warehouse can be three times the cost of a slipchain system, but the additional cost per trailer is £3,000 with a weight penalty of 500kg.
Griffiths advises that if there are more than eight trailers in shuttle operation it is generally more economical to install a powered skate system.
With Loadmate the cargo rests on chain-driven skates which travel in four tracks in the trailer floor. Pallets rest on the skates, which are lifted clear of the floor for loading and unloading. The tracks in the trailer mate with a Hydraroll conveyor on the loading bay, allowing complete trailer-loads of pallets to be unloaded in a single operation taking less than three minutes.
The system in the vehicle has to align precisely with the conveyor on the dock—to prevent movement during unloading the trailer is locked against the dock using a rear kingpin behind the under-run bar.
One version of Loadmate is proving popular with distribution companies because it can be used with fork-lifts. Wincanton Logistics Is using it on a contract to operate St Ivel's national distribution centre at Gloucester. Faster vehicle turnaround times are essential to maximise efficiency at the NDC, which has replaced several regional distribution centres.
Goods are loaded mechanically by pallet truck at food processing plants, but unloading at Gloucester is automatic. On the return leg the trailers deliver raw materials into the factories.
Exel also relies on the Loadmate for its contract with Dairy Crest to move cheese from its manufacturing plant in Wales to a maturation plant at Nuneaton. Liverpool-based Joloda has a contract to supply automated loading systems for the delivery of seats on a just-intime basis to the Jaguar S-Class production line at Castle Bromwich. At the nearby Lear Group plant palletised seats are loaded in reverse order onto the trailers, allowing them to be offloaded onto the feeder line for the Jaguar production line to mate up with their designated Chassis.
Three double-deck Joloda equipped trailers are used in this operation. Batches of 36 or 48 pallets are delivered in a single load. The moving-floor systems have been installed directly onto the existing trailer floors to simplify the resale of the trailers at the end of their lease life.
Each deck has two moving-floor units; the front bulkhead has been extended to accommodate the drive motor assemblies. Each moving-floor section has a safe working load of 4,000kg per deck.
This system incorporates an inverter to match different conveyor speeds at the two sites: Lear's output speed is 15rn/rnin white the Jaguar production line takes deliveries at 10m/min.
A variation on the moving-floor sYstern is the roller-track, wnich is widely used for large items such as aluminium• air cargo boxes. Air Cargo Transport, for example, is using a 13.7m Don-Bur Palletmaster curtainsider to transfer pallets from East Midlands Airport to the company's distribution centre.
The size of the pallets often requires
the trailer, first towards the front bulkhead; then towards the rear. The slats are grouped in three sections and move forward in a one-two-three sequence, so one section moves while the others are still. This ensures sufficient load friction to prevent forward movement.
Once all three sections have moved forward all the slats move to the rear simultaneously, shifting the load towards the back of the trailer. Slats vary from 4111111 to IOMM thick, Toploading of heavy-duty waste, for example, requires a slat strong enough to withstand the shock— buckled slats will stop the floor.
The Keith Walking Floor has 24 97mm-wide slats in a 13.6m trailer. The aluminium slats include vertical support sections to give extra load-bearing support and 19 mm-high ridges to absorb vertical impacts.
A sub-deck is fitted for extra strength, consisting of 25x25mm steel or aluminium box sections running the length of the trailer. The cross-member supports, at 400mm centres, are tied into the sub-deck; the hydraulic drive units are mounted beneath the floor ahead of the running gear.
Speed of unloading is determined by the amount of hydraulic fluid circulating through the pump. In Keith's case the pump moves 200lit/min to give a claimed unloading time of less than four minutes for its Running Floor system. Moving floors offer significant economies; they offer faster unloading times than ejector trailers, with an average of five minutes instead of eight. Servicing costs are lower too, with oil filter changes and nut tightening as the main items.
Euroejectors, the West Midlands-based manufacturer of ejector trailers, has developed a moving-floor system called the Eurofloor. Details are being kept under wraps until its launch next month, but it will handle a wide range of bulk cargoes including aggregates, grain, waste paper and palletised goods.