POWER ON DEMAND
Page 32
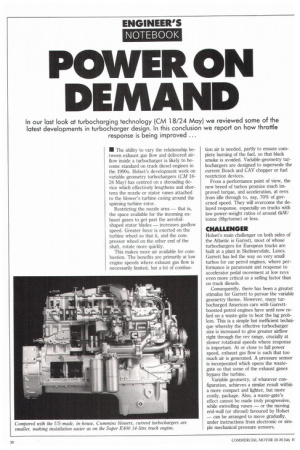
Page 33
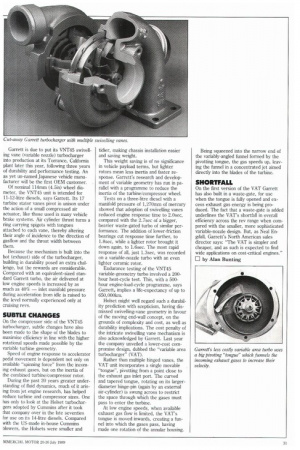
If you've noticed an error in this article please click here to report it so we can fix it.
In our last look at turbocharging technology (CM 18/24 May) we reviewed some of the latest developments in turbocharger design. In this conclusion we report on how throttle response is being improved ...
• 'rhe ability to vary the relationship between exhaust gas flow and delivered airflow inside a turbocharger is likely to become standard on truck diesel engines in the 1990s. Holset's development work on variable geometry turbochargers (CM 1824 May) has centred on a shrouding device which effectively lengthens and shortens the nozzle or stator vanes attached to the blower's turbine casing around the spinning turbine rotor.
Restricting the nozzle area — that is, the space available for the incoming exhaust gases to get past the aerofoilshaped stator blades — increases gasflow speed. Greater force is exerted on the turbine wheel so that it, and the compressor wheel on the other end of the shaft, rotate more quickly.
This makes more air available for combustion. The benefits are primarily at low engine speeds where exhaust gas flow is necessarily limited, but a lot of combus tion air is needed, partly to ensure complete burning of the fuel, so that black smoke is avoided. Variable-geometry turbochargers are designed to supersede the current Bosch and CAV chopper or fuel restriction devices.
From a performance point of view, the new breed of turbos promise much improved torque, and acceleration, at revs from idle through to, say, 70% of governed speed. They will overcome the delayed response, especially on trucks with low power-weight ratios of around 6kW/ tonne (8hp/tonne) or less.
CHALLENGER
Holset's main challenger on both sides of the Atlantic is Garrett, most of whose turbochargers for European trucks are built at a plant in Skehnersdale, Lancs. Garrett has led the way on very small turbos for car petrol engines, where performance is paramount and response to accelerator pedal movement at low revs even more critical as a selling factor than on truck diesels.
Consequently, there has been a greater stimulus for Garrett to pursue the variable geometry theme. However, many turbocharged American cars with Garrettboosted petrol engines have until now relied on a waste-gate to beat the lag problem. This is a simple but inefficient technique whereby the effective turbocharger size is increased to give greater airflow right through the rev range, crucially at slower rotational speeds where response is important. At or close to full power speed, exhaust gas flow is such that too much air is generated. A pressure sensor is incorporated which opens the wastegate so that some of the exhaust gases bypass the turbine.
Variable geometry, of whatever configuration, achieves a similar result within a more compact and lighter, but more costly, package. Also, a waste-gate's effect cannot be made truly progressive, while swivelling vanes — or the moving end-wall (or shroud) favoured by Holset — can be arranged to move gradually, under instructions from electronic or simple mechanical pressure sensors. Garrett is due to put its VNT45 swivelling vane (variable nozzle) turbocharger into production at its Torrance, California plant later this year, following three years of durability and performance testing. An as yet un-named Japanese vehicle manufacturer will be the first OEM customer.
Of nominal 114mm (4.5in) wheel diameter, the VNT45 unit is intended for 11-12-litre diesels, says Garrett. Its 17 turbine stator vanes pivot in unison under the action of a small compressed air actuator, like those used in many vehicle brake systems. Air cylinder thrust turns a ring carrying spigots with tongues attached to each vane, thereby altering their angle of incidence to the direction of gasflow and the throat width between them.
Because the mechanism is built into the hot (exhaust) side of the turbocharger, building in durability posed an extra challenge, but the rewards are considerable. Compared with an equivalent-sized standard Garrett turbo, the air delivered at low engine speeds is increased by as much as 40% — inlet manifold pressure during acceleration from idle is raised to the level normally experienced only at cruising revs.
SUBTLE CHANGES
On the compressor side of the VNT45 turbocharger, subtle changes have also been made to the shape of the blades to maximise efficiency in line with the higher rotational speeds made possible by the variable turbine geometry.
Speed of engine response to accelerator pedal movement is dependent not only on available "spinning force" from the incoming exhaust gases, but on the inertia of the combined turbine/compressor rotor.
During the past 20 years greater understanding of fluid dynamics, much of it arising from jet engine research, has helped reduce turbine and compressor sizes. One has only to look at the Holset turbochargers adopted by Cummins after it took that company over in the late seventies for use on its 14-litre diesels. Compared with the US-made in-house Cummins blowers, the Holsets were smaller and tidier, making chassis installation easier and saving weight.
This weight saving is of no significance in vehicle payload terms, but lighter rotors mean less inertia and faster response. Garrett's research and development of variable geometry has run in parallel with a programme to reduce the inertia of the turbine/compressor wheel.
Tests on a three-litre diesel with a manifold pressure of 1,270mm of mercury showed that adoption of swivelling vanes reduced engine response time to 2.0sec, compared with the 2.7sec of a bigger, heavier waste-gated turbo of similar performance. The addition of lower-friction bearings cut response time further, to 1.8sec, while a lighter rotor brought it down again, to 1.6sec. The most rapid response of all, just 1.3sec, was recorded on a variable-nozzle turbo with an even lighter ceramic rotor.
Endurance testing of the VNT45 variable-geometry turbo involved a 200hour heat-cycle test. This, with a 500hour engine-load-cycle programme, says Garrett, implies a life-expectancy of up to 650,0001cm.
Ho[set might well regard such a durability prediction with scepticism, having dismissed swivelling-vane geometry in favour of the moving end-wall concept, on the grounds of complexity and cost, as well as durability implications. The cost penalty of the intricate swivelling vane mechanism is also acknowledged by Garrett. Last year the company unveiled a lower-cost compromise design, dubbed the "variable area turbocharger" (VAT).
Rather than multiple hinged vanes, the VAT unit incorporates a single movable "tongue", pivotting from a point close to the exhaust gas inlet port. The curved and tapered tongue, rotating on its largerdiameter hinge-pin (again by an external air-cylinder) is swung across to restrict the space through which the gases must pass to enter the turbine.
At low engine speeds, when available exhaust gas flow is limited, the VAT's tongue is moved inwards, creating a funnel into which the gases pass, having made one rotation of the annular housing. Being squeezed into the narrow end of the variably-angled funnel formed by the pivotting tongue, the gas speeds up, leaving the funnel in a concentrated jet aimed directly into the blades of the turbine.
SHORTFALL
On the first version of the VAT Garrett has also built in a waste-gate, for use when the tongue is fully opened and excess exhaust gas energy is being produced. The fact that a waste-gate is added underlines the VAT's shortfall in overall efficiency across the rev range when compared with the smaller, more sophisticated variable-nozzle design. But, as Neal Engdall, Garrett's North American sales director says: "The VAT is simpler and cheaper, and as such is expected to find wide applications on cost-critical engines."
by Alan Bunting