Warehouse
Page 22
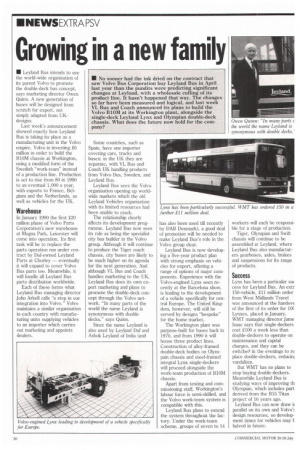
If you've noticed an error in this article please click here to report it so we can fix it.
In January 1990 the first .220 million phase of Volvo Parts Corporation's new warehouse at Magna Park, Leicester will come into operation. Its first task will be to replace the parts operation run under contract by Daf-owned Leyland Parts at Chorley — eventually it will expand to cover Volvo Bus parts too. Meanwhile, it will handle all Leyland Bus parts distribution worldwide.
Each of these forms what Leyland Bus managing director John Arkell calls "a step in our integration into Volvo." Volvo maintains a similar organisation in each country with manufacturing units supplying vehicles to an importer which carries out marketing and appoints dealers. Some countries, such as Spain, have one importer covering cars, trucks and buses; in the UK they are separate, with VL Bus and Coach UK handling products from Volvo Bus, Sweden, and Leyland Bus.
Leyland Bus sees the Volvo organisation opening up worldwide markets which the old Leyland Vehicles organisation with its limited resources had been unable to crack.
The relationship clearly affects its development programme. Leyland Bus now sees its role as being the specialist city bus builder in the Volvo group. Although it will continue to produce the Tiger coach chassis, city buses are likely to be much higher on its agenda for the next generation. And although VL Bus and Coach handles marketing to the UK, Leyland Bus does its own export marketing and plans to promote the double-deck concept through the Volvo network. "In many parts of the world the name Leyland is synonymous with double decks," says Quinn.
Since the name Leyland is also used by Leyland Daf and Ashok Leyland of India (and has also been used till recently by DAB Denmark), a good deal of promotion will be needed to make Leyland Bus's role in the Volvo group clear.
Leyland Bus is now developing a five-year product plan with strong emphasis on vehicles for export, offering a range of options of major components. Experience with the Volvo-engined Lynx seen recently at the Barcelona show, is leading to the development of a vehicle specifically for central Europe. The United Kingdom, however, will still be served by designs "bespoke" for the home market.
The Workington plant was purpose-built for buses back in 1970, and from 1990 it will house three product lines. Construction of alloy-framed double-deck bodies on Olympain chassis and steel-framed integral Lynx single-deckers will proceed alongside the work-team production of B1OM chassis.
Apart from testing and commissioning staff, Workington's labour force is semi-skilled, and the Volvo work-team system is compatible with this.
Leyland Bus plans to extend the system throughout the factory. Under the work-team scheme, groups of seven to 14 workers will each be responsible for a stage of production.
Tiger, Olympian and Swift chassis will continue to be assembled at Leyland, where Leyland Bus also manufacturers gearboxes, axles, brakes and suspensions for its range of products.
Success
Lynx has been a particular suu. cess for Leyland Bus. An ext. 150-vehicle, 211 million order from West Midlands Travel was announced at the handovt of the first of its order for 10€ Lynxes, placed in January. WMT managing director Jame Isaac says that single-deckers cost .E100 a week less than double-deckers to operate on maintenance and capital charges, and they can be switched in the evenings to re place double-deckers, reducip vandalism.
But WMT has no plans to stop buying double-deckers. Meanwhile Leyland Bus is studying ways of improving th Olympian, which includes part derived from the B15 Titan project of 16 years ago.
Leyland Bus can now draw ii parallel on its own and Volvo': design resources, so development times for vehicles may halved in future.