What is the Ideal Stroke-Bore Ratio?
Page 40
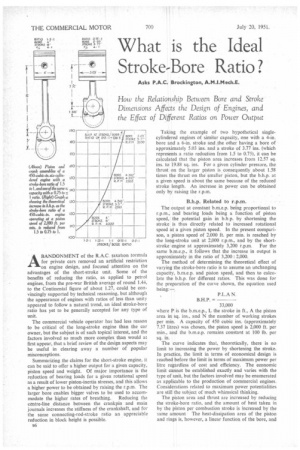
Page 41
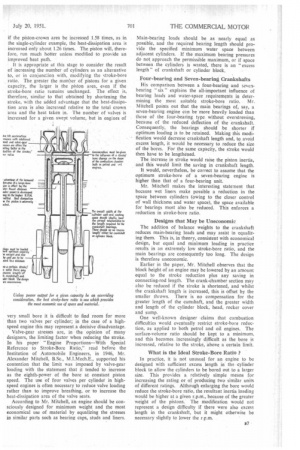
If you've noticed an error in this article please click here to report it so we can fix it.
Asks P.A.C. Brockington, A.M.I.Mech.E.
How the Relationship Between Bore and Stroke Dimensions Affects the Design of Engines, and the Effect of Different Ratios on Power Output
ABANDONMENT of the R.A.C. taxation formula for private cars removed an artificial restriction on engine design, and focused attention on the advantages of the short-stroke unit. Some of the benefits of reducing the ratio, as applied to petrol engines, from the pre-war British average of round 1.44, to the Continental figure of about 1.27, could be convincingly supported by technical reasoning, but although the appearance of engines with ratios of less than unity appeared to follow a natural trend, an ideal stroke-bore ratio has yet to be generally accepted for any type of unit.
The commercial vehicle operator has had less reason to be critical of the long-stroke engine than the car owner, but the subject is of such topical interest, and the factors involved so much more complex than would at first appear, that a brief review of the design aspects may be useful in clearing away a number of popular misconceptions.
Summarizing the claims for the short-stroke engine, it can be said to offer a higher output for a given capacity, piston speed and weight. Of major importance is the reduction of bearing loads for a given rotational speed as a result of lower piston-inertia stresses, and this allows a higher power to be obtained by raising the r.p.m. The larger bore enables bigger valves to be used to accommodate the higher rates of breathing. Reducing the centre-line distance between the crankpin and main journals increases the stiffness of the crankshaft, and for the same connecting-rod-stroke ratio an appreciable reduction in block height is possible.
a6 Taking the example of two hypothetical singlecylindered engines of similar capacity, one with a 4-in. bore and a 6-in, stroke and .the other having a bore of approximately 5.03 ins, and a stroke of 3.77 ins. (which represents a ratio reduction from 1.5 to 0.75), it can be calculated that the piston area increases from 12.57 sq. ins. to 19.88 sq. ins. For a given cylinder pressure, the thrust on the larger piston is consequently about 1.58 times the thrust on the smaller piston, but the b.h.p. at a given speed is about the same because of the reduced stroke length. An increase in power can be obtained only by raising the r.p.m.
B.h.p. Related to r.p.m.
The output at constant b.m.e.p. being proportional to r.p.m., and bearing loads being a function of piston speed, the potential gain in b.h p. by shortening the stroke is thus directly related to increased rotational speed at a given piston speed. In the present comparison, a piston speed of 2,000 ft. per min. is reached by the long-stroke unit at 2,000 r.p.m., and by the short stroke engine at approximately 3,200 r.p.m. For the same b.m.e.p., it follows that the increase in output is approximately in the ratio of 3,200: 2,000.
The method of determining the theoretical effect of varying the stroke-bore ratio is to assume an unchanging capacity, b.m.e.p. and piston speed, and then to calculate the b.h.p. for different ratios. This was done for the preparation of the curve shown, the equation used being:— P.L.A N.
B.H.P. –
33,000
where P is the b.m.e.p., L the stroke in ft., A the piston area in sq. ins., and N the number of working strokes per mm. A capacity of 450 cubic ins. (approximately 7.37 litres) was chosen, the piston speed is 2,000 ft. per min., and the b.m.e.p. remains constant at 100 lb. per sq. in.
The curve indicates that, theoretically, there is no limit to increasing the power by shortening the stroke. In practice, the limit in terms of economical design is reached before the limit in terms of maximum power per litre regardless of cost and efficiency. The economic limit cannot be established exactly and varies with the type of unit, but the factors involved may be enumerated as applicable to the production of commercial engines. Considerations related to maximum power potentialities are still the subject of much whimsical thinking.
The piston area and thrust are increased by reducing the stroke-bore ratio, and the amount of heat taken in by the piston per combustion stroke is increased by the same amount The heat-dissipation area of the piston and rings is, however, a linear function of the bore, and if the piston-crown area be increased 1.58 times, as in the single-cylinder example, the heat-dissipation area is increased only about 1.26 times. The piston will, therefore, run much hotter unless modified to provide an improved heat path.
it is appropriate at this stage to consider the result of increasing the number of cylinders as an alternative to, or in conjunc:ion with, modifying the stroke-bore ratio. The greater the number of pistons for a given capacity, the larger is the piston area, even if the stroke-bore ratio remains unchanged. The effect is, therefore, similar to that obtained by shortening the stroke, with the added advantage that the heat-dissipation area is also increased relative to the total crown area and the heat taken in. The number of valves is increased for a given swept volume, but in engines of
very small bore it is difficult to find room for more than two valves per cylinder; in the case of a highspeed engine this may represent a decisive disadvantage.
Valve-gear stresses are, in the opinion of many designers, the limiting factor when reducing the stroke. In his paper "Engine Proportions—With Special Reference to Stroke-Bore Ratio," read before the Institution of Automobile Engineers, in 1946, Mr. Alexander Mitchell, B.Sc., M.I.Mech.E., supported his contention that the limit was imposed by valve-gear loading with the statement that it tended to increase as the eighth-power of the bore at constant piston speed. The use of four valves per cylinder in highspeed engines is often necessary to reduce valve loading rather than to improve breathing, or to increase the heat-dissipation area of the valve seats.
According to Mr. Mitchell, an engine should be consciously designed for minimum weight and the most economical use of material by equalizing the stresses in similar parts such as bearing caps, studs and liners.
Main-bearing loads should be as nearly equal as possible, and the required bearing length should provide the specified minimum water space between adjacent cylinders. If the maximum bearing pressures do not approach the permissible maximum, or if space between the cylinders is wasted, there is an 'excess length" of crankshaft or cylinder block.
Four-bearing and Seven-bearing Crankshafts
His comparison between a four-bearing and seveabearing " six " explains the all-important influence of bearing loads and water-space requirements in determining the most suitable stroke-bore ratio. Mr. Mitchell points out that the main bearings of, say, a seven-bearing engine can be more heavily loaded than those of the four-bearing type without overstressing, because of the reduced deflection of the crankshaft. Consequently, the bearings should •be shorter if optimum loading is to be retained. Making this modification would decrease crankshaft length and, to avoid excess length, it would be necessary to reduce the size of the bores. For the same capacity, the stroke would then have to be lengthened.
The increase in stroke would raise the piston inertia, and this would limit the saving in crankshaft length.
It would, nevertheless, be correct to assume that the optimum stroke-bore of a seven-bearing engine is higher than that of a four-bearing unit.
Mr. Mitchell makes the interesting statement that because wet liners make possible a reduction in the space between cylinders (owing to the closer control of wall thickness and water space), the space available for bearings must also be reduced. This enforces a reduction in stroke-bore ratio.
Designs that May be Uneconomic
The addition of balance weights to the crankshaft reduces main-bearing loads and may assist in equalizing them. This is, in theory, consistent with economical design, but equal and minimum loading in practice results in an extremely low stroke-bore ratio, and the main bearings are consequently too long. The design is therefore uneconomic.
Earlier in the paper, Mr. Mitchell observes that the block height of an engine may be lowered by an amount equal to the stroke reduction plus any saving in connecting-rod length. The crank-chamber section may also be reduced if the stroke is shortened, and whilst the crankshaft length is increased, this is offset by the smaller throws. There is no compensation for the greater length of the camshaft, and the greater width and length of the cylinder block, head, rocker cover and sump.
One well-known designer claims that combustion difficulties would eventually restrict stroke-bore reduction, as applied to both petrol and oil engines. The surface-volume ratio should be kept to a minimum, and this becomes increasingly difficult as the bore is increased, relative to the stroke, above a certain limit.
What is the Ideal Stroke-Bore Ratio ?
In practice, it is not unusual for an engine to be designed with sufficient excess length in the cylinder block to allow the cylinders to be bored out to a larger size. This provides a relatively simple means for increasing the rating or of producing two similar units of different ratings. Although enlarging the bore would reduce the stroke-bore ratio, the resultant inertia loading would be higher at a given r.p.m., because of the greater weight of the pistons. The modification would not represent a design difficulty if there were also excess length in the crankshaft, but it might otherwise be necessary slightly to lower the r.p.m.