Put a brake on you.
Page 52
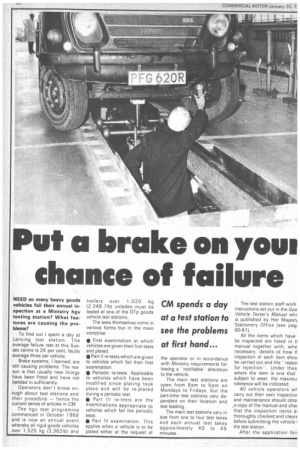
Page 54
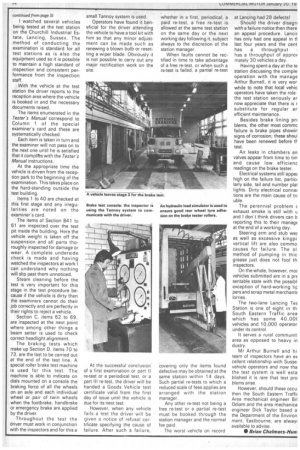
If you've noticed an error in this article please click here to report it so we can fix it.
chance of failure
NEED so many heavy goods vehicles fail their annual inspection at a Ministry hgv testing station? What features are causing the problems?
To find out I spent a day at Lancing test station. The average failure rate at this Sussex centre is 24 per cent; faults average three per vehicle.
Brake systems, I learned, are still causing problems. The reason is that usually new linings have been fitted and have not bedded in sufficiently.
Operators don't know enough about test stations and their procedure — hence the current series of articles in CM.
The hgv test programme commenced in October 1 968 and is now an annual event whereby all rigid goods vehicles over 1,525 kg (3,3621b) and trailers over 1,020 kg (2.248.7tb) unladen must be tested at one of the DTp goods vehicle test stations.
The tests themselves come in various forms but in the main comprise: • First examination at which vehicles are given their first tests and plated.
• Part 11 re-tests which are given to vehicles which fail their first examination.
• Periodic re-tests. Applicable to vehicles which have been modified since plating took place and will be re-plated during a periodic test.
• Part III re-tests are the examinations appropriate to vehicles which fail the periodic tests.
• Part IV examination. This applies when a vehicle is to be plated either at the request of the operator or in accordance with Ministry requirements following a "notifiable" alteration to the vehicle.
The main test stations are open from 8am to 5pm on Mondays to Fridays, but the part-time test stations vary dependent on their location and test loading.
The main test stations vary in size from one to four test lanes and each annual test takes approximately 40 to 45 minutes.
The test station staff work instructions set out in the Goo Vehicle Tester's Manual whi, is published by Her Majesty Stationery Office (see pag 60-61).
All the items which have be inspected are listed in tl manual together with, whe necessary, details of how ti inspection of each item shou be carried out and the "reasoi for rejection-. Under thes where the item is one that subject to wear, the maximu tolerance will be indicated.
All vehicle operators carry out their own inspectior and maintenance should obta , a copy of the manual and chec that the inspection items ai thoroughly checked and cleare before submitting the vehicle 1 the test station.
After the application fort I watched several vehicles being tested at the test station on the Churchill Industrial Estate, Lancing, Sussex. The method of conducting the examination is standard for all test stations as is also the equipment used so it is possible to maintain a high standard of inspection and consistent performance from the inspection staff.
With the vehicle at the test station the driver reports to the reception area where the vehicle is booked in and the necessary documents raised.
The items enumerated in the Tester's Manual correspond to Column 1 of the special examiner's card and these are systematically checked.
Each item is taken in turn and the examiner will not pass on to the next one until he is satisfied that it complfts with the Tester's Manual instructions.
At the appropriate time the vehicle is driven from the reception park to the beginning of the examination. This takes place on the hard-standing outside the test building.
Items 1 to 40 are checked at this first stage and any irregularities are noted on the examiner's card.
The items of Section B41 to 61 are inspected over the test pit inside the building. Here the vehicle weight is taken off the suspension and all parts thoroughly inspected for damage or wear. A complete underside check is made and having watched the inspectors at work I can understand why nothing will slip past them unnoticed.
Steam cleaning before the test is very important for this stage in the test procedure because if the vehicle is dirty then the examiners cannot do their job correctly and are perfectly in their rights to reject a vehicle.
Section C, items 62 to 69, are inspected at the next point where among other things a beam setter is used to check correct headlight alignment.
The braking tests which make up Section 0, items 70 to 73, are the last to be carried out at the end of the test line. A special roller brake test machine is used for this test. The machine is able to indicate on dials mounted on a console the braking force of all the wheels on an axle and each individual wheel or pair of twin wheels when the footbrake, handbrake or emergency brake are applied by the driver.
Throughout the test the driver must work in conjunction with the inspectors and for this a small Tannoy system is used.
Operators have found it beneficial for the driver attending the vehicle to have a tool kit with him so that any minor adjustment can be made such as renewing a blown bulb or resetting a wiper blade. Obviously it is not possible to carry out any major rectification work on the site.
At the successful conclusion of a first examination or part II re-test or a periodical test, or a part III re-test, the driver will be handed a Goods Vehicle test certificate valid from the first day of issue until the vehicle is due for its next test.
However, when any vehicle fails a test the driver will be given a notice of refusal certificate specifying the cause of failure. After such a failure, whether in a first, periodical, a paid re-test, a free re-test is allowed at the same test station on the same day or the next working day following it, subject always to the discretion of the station manager.
When faults cannot be rectified in time to take advantage of a free re-test, or when such a re-test is failed, a partial re-test covering only the items found defective may be obtained at the same station within 14 days. Such partial re-tests to which a reduced scale of fees applies are arranged with the station manager.
Any other re-test not being a free re-test or a partial re-test must be booked through the station manager and the normal fee paid.
The worst vehicle on record at Lancing had 28 defects!
Should the driver disagri with a failure notice then there an appeal procedure. Lancir has only had one appeal in ti last four years and the cent has a throughput has a throughput of appro> rnately 30 vehicles a day.
Having spent a day at the te station discussing the comple operation with the manage Arthur Burnell, it is very wor while to note that local vehic operators have taken the role the test station seriously ar now appreciate that there is r substitute for regular ar efficient maintenance.
Besides brake lining pr( blems, the other most commc failure is brake pipes showin signs of corrosion; these shoul have been renewed before tltest.
Air leaks in chambers an valves appear from time to tim and cause low efficienc readings on the brake tester.
Electrical systems still a ppez high on the failure list, partici larly side, tail and number plat lights. Dirty electrical connei tions are the main cause of tr( uble.
The perennial problem c exhaust smoke is still with u and I don't think drivers can b reporting this to their managE at the end of a working day.
Steering arm and stub we as well as excessive kingpi vertical lift are also commo causes for failure. The ol method of pumping in thic grease just does not fool th inspectors.
On the whole, however, mot vehicles submitted are in a prE sentable state with the possibl exception of hard-working tip pers and scrap metal merchant5 lorries.
The two-lane Lancing Tes Station is one of eight in th South Eastern Traffic area which has some 40,00( vehicles and 10,000 operator under its control.
It serves a rural communit area as opposed to heavy in dustry.
Mr Arthur Burnell and hi team of inspectors have an ex cellent relationship with Susse. vehicle operators and now tha the test system is well esta blished it is rare that test pro blems arise.
However, should these occu then the South Eastern Traffic Area mechanical engineer Bil Odiam and the area rnechanica engineer Dick Taylor based a the Department of the Environ ment, Eastbourne, are alwaw available to advise.
• Brian Chalmers-Huni