Fearless testing
Page 43
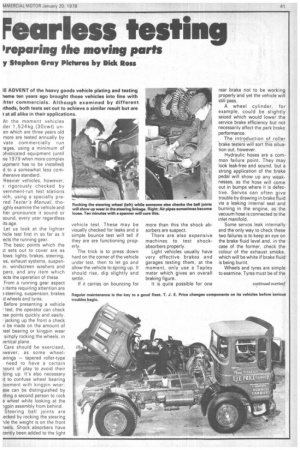
Page 44
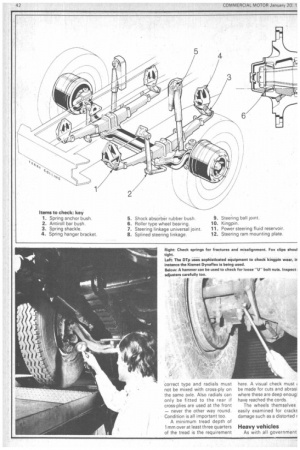
Page 45
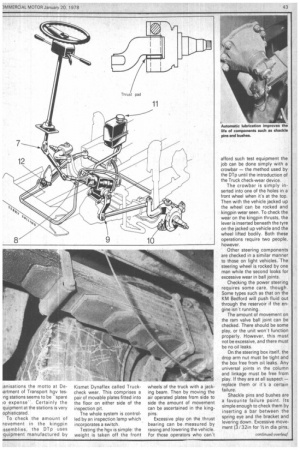
Page 46
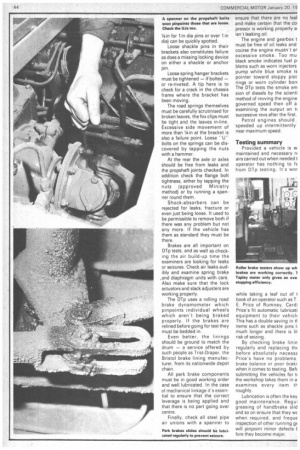
If you've noticed an error in this article please click here to report it so we can fix it.
Preparing the moving parts
y Stephen Gray Pictures by Dick Ross
IE ADVENT of the heavy goods vehicle plating and testing heme ten years ago brought those vehicles into line with ihter commercials. Although examined by different ?thods, both tests set out to achieve a similar result but are t at all alike in their applications.
At the moment vehicles der 1,524kg (30cwt) on'en which are three years old more are tested annually by vate commercially run rages, using a minimum of ohisticated equipment (until ne 1979 when more complex uipment has to be installed) d to a somewhat less cornahensive standard.
Heavier vehicles, however, a rigorously checked by vernment-run test stations iich, using a specially prered Tester's Manual, thoJghly examine the vehicle and her pronounce it sound or sound, every year regardless its age.
Let us look at the tighter hide test first in so far as it ects the running gear.
The basic points which the 3t sets out to cover are as lows: lights, brakes, steering, .es, exhaust systems, suspenin, windscreen washers and pers, and any item which 'ects the operation of these_ From a running gear aspect a items requiring attention are a steering, suspension, brakes d wheels and tyres.
Before presenting a vehicle test, the operator can check ase points quickly and easily. , jacking up the front a check n be made on the amount of ieel bearing or kingpin wear • simply rocking the wheels, in rertical plane.
Care should be exercised, )wever, as some wheelrings — tapered roller-type need to have a certain riount of play to avoid their izing up. It's also necessary it to confuse wheel bearing ovement with kingpin wear; ese can be distinguished by itting a second person to rock
e wheel while looking at the -igpin assembly from behind. Steering ball joints are lecked by rocking the steering iile the weight is on the front neels. Shock absorbers have cently been added to the light
vehicle test. These may be visually checked for leaks and a simple bounce test will tell if they are are functioning properly.
The trick is to press down hard on the corner of the vehicle under test then to let go and allow the vehicle to spring up. It should rise, dip slightly and settle.
If it carries on bouncing for
more than this the shock absorbers are suspect.
There are also expensive machines to test shockabsorbers properly.
Light vehicles usually have very effective brakes and garages testing them, at the moment, only use a Tapley meter which gives an overall braking figure.
It is quite possible for one rear brake not to be working properly and yet the vehicle will still pass.
A wheel cylinder, for example, could be slightly seized which would lower the service brake efficiency but not necessarily affect the park brake performance.
The introduction of roller brake testers•will sort this situation out, however.
Hydraulic hoses are a common failure point. They may look leak-free and sound, but a strong application of the brake pedal will show up any weaknesses, as the hose will come out in bumps where it is defective. Servos can often give trouble by drawing in brake fluid via a leaking internal seal and burning in the engine, as the vacuum hose is connected to the inlet manifold.
Some servos leak internally and the only way to check these two failures is to keep an eye on the brake fluid level and, in the case of the former, check the colour of the exhaust smoke, which will be white if brake fluid. is being burnt.
Wheels and tyres are simple to examine. Tyres must be of the correct type and radials must not be mixed with cross-ply on the same axle. Also radials can only be fitted to the rear if cross-plies are used at the front — never the other way round. Condition is all important too.
A minimum tread depth of 1 mm over at least three quarters of the tread is the requirement here. A visual check must be made for cuts and abrasi where these are deep enougl have reached the cords.
The wheels themselves easily examined for cracks damage such as a distorted r lanisations the motto at Deortment of Transport hgv tesng stations seems to be "spare io expense". Certainly the quipment at the stations is very ophisticated.
To check the amount of lovement in the kingpin ssemblies, the DTp uses .quipment manufactured by Kismet Dynaflex called Truckcheck wear. This comprises a pair of movable plates fitted into the floor on either side of the inspection pit.
Tne whole system is controlled by an inspection lamp which incorporates a switch.
Testing the hgv is simple: the weight is taken off the front wheels of the truck with a jacking beam. Then by moving the air operated plates from side to side the amount of movement can be ascertained in the kingpins.
Excessive play on the thrust bearing can be measured by raising and lowering the vehicle. For those operators who can't afford such test equipment the job can be done simply with a crowbar — the method used by the DTp until the introduction of the Truck check-wear device.
The crowbar is simply inserted into one of the holes in a front wheel when it's at the top. Then with the vehicle jacked up the wheel can be rocked and kingpin wear seen. To check the wear on the kingpin thrusts, the lever is inserted beneath the tyre on the jacked up vehicle and the wheel lifted bodily. Both these operations require two people, however.
Other steering components are checked in a similar manner to those on light vehicles. The steering wheel is rocked by one man while the second looks for excessive wear in ball joints.
Checking the power steering requires some care, though. Some types such as that on the KM Bedford will push fluid out through the reservoir if the engine isn't running.
The amount of movement on the ram valve ball joint can be checked. There should be some play, or the unit won't function properly. However, this must not be excessive, and there must be no oil leaks.
On the steering box itself, the drop arm nut must be tight and the box free from oil leaks. Any universal joints in the column and linkage must be free from play. If they are at all suspect — replace them or it's a certain failure.
Shackle pins and bushes are a favourite failure point. Its simple enough to check them by inserting a bar between the spring eye and the bracket and levering down. Excessive movement (3/ 32in for 1/2in dia pins, Yein for lin dia pins or over lin dia) can be quickly spotted.
Loose shackle pins in their brackets also constitutes failure as does a missing locking device on either a shackle or anchor pin.
Loose spring hanger brackets must be tightened — if bolted — or re-riveted. A tip here is to check for a crack in the chassis frame where the bracket has been moving.
The road springs themselves must be carefully scrutinised for broken leaves, the fox clips must be tight and the leaves in-line. Excessive side movement of more than 1/4in at the bracket is also a failure point. Loose " bolts on the springs can be discovered by tapping the nuts with a hammer.
At the rear the axle or axles should be free from leaks and the propshaft joints checked. In addition check the flange bolt tightness, either by tapping the nuts (approved Ministry method) or by running a spanner round them.
Shock-absorbers can be rejected for leaks, fracture or even just being loose. It used to be permissible to remove both if there was any problem but not any more. If the vehicle has them as standard they must be there.
Brakes are all important on Dip tests, and as well as checking the air build-up time the examiners are looking for leaks or seizures. Check air leaks audibly and examine spring brake sand diaphragm units with care. Also make sure that the lock actuators and slack adjusters are working properly,
The DTp uses a rolling road brake dynamometer which pinpoints individual wheels which aren't being braked properly. If the brakes are relined before going for test they must be bedded in.
Even better, the linings should be ground to match the drum — a service offered by such people as Trist-Draper. the Bristol brake lining manufacturer, from its nationwide depot chain.
All park brake components must be in good working order and well lubricated. In the case of mechanIcal linkage it's essential to ensure that the correct leverage is being applied and that there is no part going over centre.
Finally, check all steel pipe air unions with a spanner to
Park brakes slides should be lubricated regularly to prevent seizure.
ensure that there are no leak and make certain that the col pressor is working properly al isn't leaking oil.
The engine and gearbox t must be free of oil leaks and course the engine mustn't er excessive smoke. Too mu black smoke indicates fuel pi blerns such as worn injectors pump while blue smoke is pointer toward sloppy pist. rings or worn cylinder bor( The DTp tests the smoke em sion of diesels by the scienti method of revving the engine governed speed then off a examining the output on h successive revs after the first.
Petrol engines should speeded up intermittently near maximum speed.
Testing summary
Provided a vehicle is w maintained and necessary rE airs carried out when needed t operator has nothing to fE from DTp testing. It's wor while taking a leaf out of t book of an operator such as T. E. Price of Rumney, Cardi Price's fit automatic lubricati equipment to their vehicli This has a double saving in tf items such as shackle pins I; much longer and there is lit risk of seizing.
By checking brake linin regularly and replacing thE before absolutely necessE Price's have no problems brake balance or poor braki when it comes to testing. Be( submitting the vehicles for ti the workshop takes them in a examines every item th roughly.
Lubrication is often the key good maintenance. Regul greasing of handbrake slid and so on ensure that they wc when required, and freque inspection of other running gE will pinpoint minor defects I fore they become major.