road and workshop
Page 35
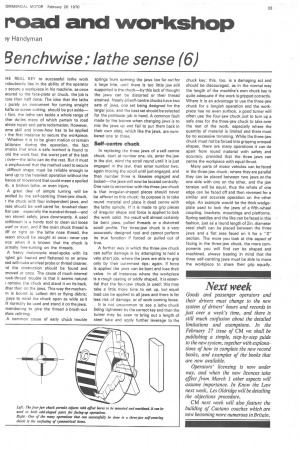
If you've noticed an error in this article please click here to report it so we can fix it.
w Handyman
genchwise lathe sense (6)
HE REAL KEY to successful lathe work ndoubtedly lies in the ability of the operator secure a workpiece in his machine, as once ecured to the face-plate or chuck, the job is lore than half done, The idea that the lathe 3 purely an instrument for turning straight hafts or screw cutting, should be put aside) fact, the lathe can tackle a whole range of ther duties many of which pertain to road ehicle repair and parts reclamation. However, ome skill and know-how has to be applied the first instance to secure the workpiece. Whether it is to be given motion or remain tationary during the operation, the fact ?.mains that once a safe method is found to old the work fast, the worst part of the task over—the lathe can do the rest. But it must e emphasized that the method used to secure difficult shape must be reliable enough to tand up to the heaviest operation without the hence of movement that could mean a spoiled )1a, a broken lathe, or even injury.
A great deal of simple turning will be andled by the self-centring three-jaw chuck, r the chuck with four independent jaws, and )ese should be well cared for, brushed clean fter use especially the mandrel thread—and ien stored safely, jaws downwards. A used )othbrush is a handy tool to clean out loose vvarf or dust, and if the main chuck thread is tiff or tight on the lathe nose thread, the 3ason should be sought at once; never use >rce when it is known that the chuck is ormally free-turning on the threads.
A heavy motorcycle steel-spoke with its ngled gib heated and flattened to an arrow ead will make an ideal probe or thread cleaner, id the obstruction should be found and moved at once. The cause of much internal luck-thread trouble is that it seems natural ) remove the chuck and stand it on its back, ither than on the jaws. This way the mechanm is bound to collect dirt or flying debris; pays to wind the chuck open as wide as it ill normally be used and stand it on the jaws, !membering to give the thread a brush-out afore refitting.
A common cause of early chack trouble springs from opening the jaws too far out for a large bite, until there is too little jaw still supported in the chuck—by this lack of thought the jaws can be distorted or their thread strained. Nearly all self-centre chucks have two sets of jaws, one set being designed for the larger jobs, and the best set should be selected for the particular job in hand. A common fault made by the trainee when changing jaws is to mix the jaws up and fail to put them back in their own slots, which like the jaws, are numbered one to three.
Self-centre chuck
In replacing the three jaws of a self-centre chuck, start at number one, vis, enter the jaw in the slot, wind the scroll round until it is just engaged in the jaw, then enter number two, again moving the scroll until just engaged, and then number three is likewise engaged and locked—the jaws will now be located centrally. One rule to remember with the three-jaw chuck is that irregular-shaped pieces should never be offered to this chuck: its purpose is to take round material and place it dead centre with the lathe spindle. If it is made to grip pieces of irregular shape and force is applied to lock the work solid, the result will almost certainly be bent jaws, pulled threads or a distorted scroll profile. The three-jaw chuck is a very accurately designed tool and cannot perform its true function if forced or pulled out of true.
A further way in which the three-jaw chuck can suffer damage is by attempting to hold a very short job, where the jaws are able to grip only by their outermost tips; again, if force is applied the jaws can be bent and lose their value. In all instances where the workpiece is a rough casting or oddly shaped, it is essential that the four-jaw chuck is used: this may take a little more time to set up, but equal load can be applied to all jaws and there is far less risk of damage, or of work coming loose.
It is not uncommon to see a lathe chuck being tightened by the correct key and then the turner may be seen to bring out a length of steel tube and apply further leverage to the
chuck key; this, too, is a damaging act and should be discouraged, as in the normal way the length of the machine's own chuck key is quite adequate if the work is gripped correctly. Where it is an advantage to use the three-jaw chuck for a longish operation and the workpiece has no even surface, a good turner will often use the four-jaw chuck just to turn up a safe area for the three-jaw chuck to take over the rest of the work, especially where the quantity of material is limited and there must be no excessive trimming. While the three-jaw chuck must not be forced into gripping unequal shapes, there are many operations it can do apart from round material with safety and accuracy, provided that the three jaws can centre the workpiece with equal thrust.
Many parts of motor vehicles can be faced in the three-jaw chuck; where they are parallel they can be placed between two jaws on the one side with one on the other, and the jaw tension will be equal, thus the whole of one edge can be faced off and then reversed for a similar and accurate operation on the other edge. An example would be the thick wedgeplate used to lock the jaws of a fifth-wheel coupling, brackets, mountings and platforms. Spring saddles and the like can be faced in this fashion, just as a round length of 2in. diameter steel shaft can be placed between the three jaws and a flat area faced on it for a –13" section. The more you look at this aspect of facing in the three-jaw chuck, the more components you will find can be shaped and machined, always bearing in mind that the three self-centring jaws must be able to move the workpiece to share their grip equally.