The Luton men reach
Page 136
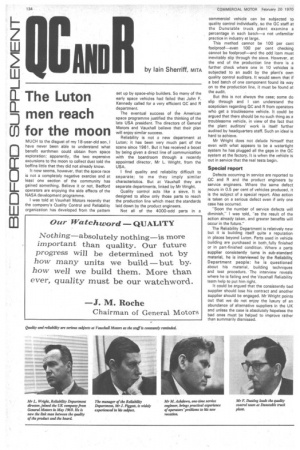
Page 137
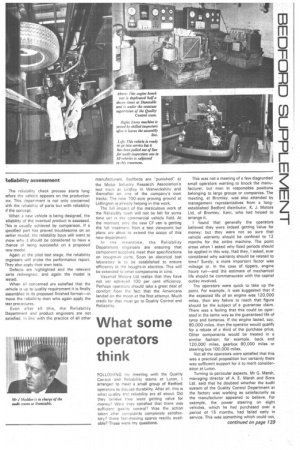
Page 141
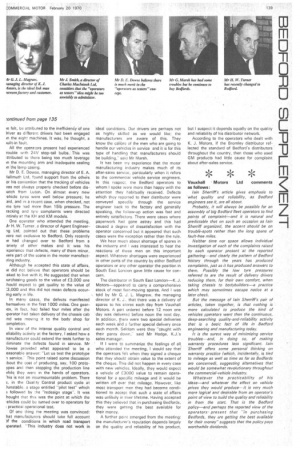
If you've noticed an error in this article please click here to report it so we can fix it.
U) for the moon
MUCH to the disgust of my 18-year-old son, I have never been able to understand what benefit earthmen could obtain from space exploration: apparently, the two expensive excursions to the moon to collect dust told the boffins little that they did not already know.
It now seems, however, that the space race is not a completely negative exercise and at least one section of the community has gained something. Believe it or not, Bedford operators are enjoying the side effects of the NASA development programme.
I was told at Vauxhall Motors recently that the company's Quality Control and Reliability organization has developed from the pattern set up by space-ship builders. So many of the early space vehicles had failed that John F. Kennedy called for a very efficient QC and R department.
The eventual success of the American space programme justified the thinking of the late USA president. The directors of General Motors and Vauxhall believe that their plan will enjoy similar success.
Reliability is not a new department at Luton; it has been very much part of the scene since 1961. But it has received a boost by being given a direct line of communication with the boardroom through a recently appointed director, Mr L. Wright, from the USA.
I find quality and reliability difficult to separate; to me they imply similar characteristics. But at Vauxhall they are separate departments, linked by Mr Wright.
Quality control acts like a sieve. It is designed to allow only those parts to reach the production line which meet the standards laid down by the product engineers.
Not all of the 4000-odd parts in a commercial vehicle can be subjected to quality control individually, so the QC staff at the Dunstable truck plant examine a percentage in each batch—a not unfamiliar practice in industry at large.
This method cannot be 100 per cant foolproof—even 100 per cent checking cannot be foolproof—and the odd item must inevitably slip through the sieve. However, at the end of the production line there is a further check where one in 10 vehicles is subjected to an audit by the plant's own quality control auditors. It would seem that if a bad batch of one component found its way on to the production line, it must be found at the audit.
But this is not always the case; some do slip through and I can understand the scepticism regarding QC and R from operators who get a troublesome vehicle. It could be argued that there should be no such thing as a troublesome vehicle, in view of the fact that the plant auditors work is itself further audited by headquarters staff. Such an ideal is hard to achieve.
Mr Wright does not delude himself that even with what appears to be a watertight system he has plugged all the gaps in the QC system at the factory. It is when the vehicle is Out in service that the real tests begin.
Special report
Defects occurring in service are reported to QC and R and the product engineers by service engineers. Where the same defect recurs in 0.5 per cent of vehicles produced, it is the subject of a special report. Also action is taken on a serious defect even if only one case has occurred.
"Soon the number of service defects will diminish," I was told, "as the result of the action already taken, and greater benefits will occur in the future."
The Reliability Department is relatively new but it is building itself quite a reputation in places beyond Luton, Parts used in vehicle building are purchased in both fully finished or in part-finished condition. Where a parts supplier consistently turns in sub-standard material, he is interviewed by the Reliability. Department people; he is questioned about his material, building techniques and test procedure. The interview reveals where he is failing and the Vauxhall Reliability team help to put him right.
It could be argued that the consistently bad supplier should lose his contract and another supplier should be engaged. Mr Wright points out that we do not enjoy the luxury of an abundance of alternative suppliers in the UK and unless the case is absolutely hopeless the bad ones must be helped to improve rather than summarily dismissed. The reliability check process starts long iefore the vehicle appears on the production ine. This department is not only concerned vith the reliability of parts but with reliability if the concept.
When a new vehicle is being designed, the .eliability of the eventual product is assessed. rhis is usually achieved by comparison. If a ipecified part has proved troublesome on an 3arlier model, the reliability boys will want to now why it should be considered to have a :hence of being successful on a proposed iew model.
Again at the pilot test stage, the reliability N-igineers will probe the performance report. They also apply their own tests.
Defects are highlighted and the relevant aarts redesigned, and again the model is tested.
When all concerned are satisfied that the vehicle is up to quality requirement it is finally assembled in its proposed finished format—in move the reliability men who again apply the test procedures.
Even after all this, the Reliability Department and product engineers are not satisfied. In line with the practice of all other manufacturers, Bedfords are "punished" at the Motor Industry Research Association's test track at Lindley in Warwickshire and thereafter on one of the company's own tracks, The new 700-acre proving ground at Lidlington is already helping in this work.
The full impact of the meticulous work of the Reliability team will not be felt for some time yet in the commercial vehicle field. At the moment, only the new CF van is getting the full treatment from a test viewpoint but plans are afoot to extend the scope of this new department.
In the meantime, the Reliability Department engineers are ensuring that component suppliers meet their specifications on bought-in parts. Soon an electrical test laboratory is to be established to ensure efficiency in the bought-in el.ectrics. This will be extended to other components in time.
Vauxhall Motors Ltd realize that they have not yet achieved 100 per cent efficiency. Perhaps operators should take a great deal of comfort from the fact that the Americans landed on the moon at the first attempt. Much credit for that must go to Quality Control and Reliability.
What some operators think
FOLLOWING my meeting with the Quality Control and Reliability teams at Luton, I arranged to meet a small group of Bedford operators to discuss durability. After all, this is what quality and reliability are all about. Did they believe they were getting value for money? Were they satisfied that there was sufficient quality control? Was the • action taken after complaints completely satisfactory? Were fast-moving spares readily available? These were my questions. This was not a meeting of a few disgruntled small operators wanting. to knock the manufacturer, but men in responsible positions belonging to large groups or companies. The meeting, at Bromley, was also attended by management representatives from a longestablished Bedford distributor, K. J. Motors Ltd, of Bromley, Kent, who had helped to arrange it.
I found that generally the operators believed they were indeed getting Lalue for money; but they were not so Sure that vehicle warranty should be confined to 12 months for the entire machine. The point arose when I asked why fixed periods should be applied in this way. Had they, I asked, ever considered why warranty should be related to time? Surely, a more important factor was mileage or, in the case of tippers, engine hours run—and the estimate of mechanical life should be commensurate with the capital outlay involved.
The operators were quick to take up the point. For example, it was Suggested that if the expected life of an engine was 120,000 miles, then any failure to reach that figure should be the subject of a guarantee claim. There was a feeling that this could be operated in the same way as the guaranteed life of tyres and batteries. If the engine lasted, say, 80,000 miles, then the operator would qualify for a rebate of a third of the purchase price. Other components would be treated in a similar fashion; for example, back end 120,000 miles, gearbox 80,000 miles or steering box 100,000 miles.
Not all the operators were satisfied that this was a practical proposition but certainly therewas sufficient support for it to merit consideration at Luton.
Turning to particular aspects, Mr G. Marsh, managing director of A. E. Marsh and Sons Ltd, said that he doubted whether the audit system of the Quality Control Department at the factory was working as satisfactorily as the manufacturer appeared to believe. For example, the power steering on eight vehicles, which he had purchased over a ,period of 15 months, had failed early in service. This was something which could not,
is felt, be attributed to the inefficienCy.of one Inver as different drivers had been engaged on the eight machines. It was, he thought, a milt-in fault.
All the operators present had experienced rouble with 24V stop-tail bulbs.. This was ittributed to there being too much -leverage in the mounting arm and inadequate sealing in the lamp casing.
Mr D. E. Dowse, managing director of E. A. iellmuth Ltd, found support from the others or his contention that the tracking of vehicles vas not always properly checked before disoatch from Luton. On almost every new *hide tyres were well below pressure, he aid, and in a recent case, when checked, not one tyre had more than 15Ib pressure. The racking and tyre complaints were directed intirely at the KH arid KM models.
One operator who attended the meeting, ilr H. W. Turner, a director of Agent Engineerrig Ltd, pointed out that these. problems vere not exclusive to Bedford. Only recently oe had changed over to Bedford from a ariety of other makes and it • was his ixperience that defects, many of them minor, vete part of the scene in the motor manUfactiring industry.
Although he accepted this state of affairs, oe did not believe that operators should be isked to live with it. He suggested that when aurchasing goods to the value of £3,000 one ;hould expect to get quality to the value of :3,000 and this did not mean defects =curing early in life.
In many cases, the defects manifested hemselves in the first 1000 miles. One gearsox, in fact, had failed four miles after the operator had taken delivery of the chassis cab ind was moving it to the body shop for :ompletion.
In view of the intense quality control and eliability activity at the factory, I asked how a nanufacturer could extend the tests further to ruminate the defects found in service. Mr }owse provided what appeared to be a easonable answer: "Let us test the prototype n service." This point raised some discussion ibout the cost of producing, say, 100 protoypes and then stopping the production line vhile. they were in the hands of .operators. "his is not an insurmountable problem. There s, in the Quality Control product cycle at }unstable, a stage entitled "pilot test" which s followed by the "redesign stage". It was bought that this was the point at whiCh the ,ehicles could be turned over to operators for
practical operational test.
Of one thing the meeting was Convinced: hat manufacturers should take full account if the conditions in which road transport operated. "This industry does not work in
ideal conditions. Our drivers are perhaps not as highly skilled as we would like; the manufacturers are aware of this. They know the calibre of the men who are going to ,handle our vehicles in service and it is for this .type of handling that manufacturers should be building," said Mr Marsh.
It has been my experience that the motor manufacturing industry makes much of its after-sales service, particularly when it refers to the commercial vehicle service engineers. In this respect, the Bedford operators to whom I spoke were more than happy with the attention they habitually received. Defects which they reported to their distributor were conveyed speedily through the service engineer back to the factory and generally speaking, the follow-up action was fast and entirely satsifactory. There were cases where paperwork had gone astray and this had caused a degree of dissatisfaction with the operator concerned but it appeared that such cases were the exception rather than the rule.
We hear much about shortage of spares in the industry and I was interested to hear the reactions of these men on this important aspect. Whatever shortages were experienced in other parts of the country by either Bedford operators or any other operator the position in South East London gave little cause for concern.
The distributor in South East London—K. J. Motors—appeared to carry a comprehensive stock of most fast-moving spares. And I was told by Mr G. J. L. Magraw, the managing director of K. J., that there was a delivery of spares to his stores each day from Vauxhall Motors. A part ordered before 12 noon one day was delivered before noon the next day. In addition, there were two special deliveries each week and a further special delivery once each month. Seldom were they "caught with their pants down," said Mr Hodge, K.J.'s sales manager.
If I were to summarize the feelings of all who attended the meeting, I Would say that the operators felt when they signed a cheque that they should obtain value to the extent of the cheque. This did not happen in every case with new vehicles. Ideally, they would expect a vehicle of £3000 value to remain operational for a specific mileage and it would be written off over that mileage. However, like most transport men they had become conditioned to accept that such a state of affairs was unlikely in their lifetime. Having accepted this they believed that in purchasing Bedfords, they were getting the best available for their money.
A further point emerged from the meeting: the manufacturer's reputation depends largely on the quality and reliability of his product, but I suspect it depends equally on the quality and reliability of his distributor network.
According to the operators who dealt with K. J. Motors, if the Bromley distributor reflected the standard of Bedford's distributors throughout the country, then those who used GM products had little cause for complaint about after-sales service.
Vauxhall 'Motors Ltd comments as follows: lain Sherrifrs article gives emphasis to what quality and reliability, as Bedford engineers see it, are all about.
Probably, it will always be possible for an assembly of big Bedford fleet operators to find points of complaint--and it is natural and predictable that on such an occasion as lain Sherriff organized, the accent should be on troub-spots rather than the long spans of fault-free miles.
Neither time nor space allows individual investigation of each of the complaints raised by each operator present at the reported gathering—and clearly the pattern of Bedford history through the years has produced complaints, just as it has produced answers to them. Possibly the low tyre pressures referred to are the result of delivery drivers reducing them, for their own comfort, when taking chassis to bodybuilders—a practice which may sometimes escape notice at a later check.
But the message of lain Sherriff's pair of articles, taken together, is that nothing is more calculated to produce the kind of vehicles operators want than the continuous, deep-searching quality-and-reliability activity that is a basic fact of life in Bedford engineering and manufacturing today.
It is the surest way of minimizing service troubles—and, in doing so, of making warranty procedures less significant. lain Sherriff offers some personal thinking on warranty practice (which, incidentally, is tied to mileage as well as time as far as Bedfords are concerned), suggesting alternatives that would be somewhat revolutionary throughout the commercial-vehicle industry.
Whatever the practicability of his ideas—and whatever the effect on vehicle prices they would produce—it is very much more logical and desirable from an operator's point of view to build the quality and reliability in from the start. That is the 'Bedford policy—and perhaps the reported view of the operatorspresent that "in purchasing Bedfords, they are getting the best available for their money" suggests that the policy pays worthwhile dividends.